- Vyfukování, výroba dutých těles
7.1. Vstřikovací vyfukování (předlisek vyráběný vstřikováním)
7.2. Vytlačovací vyfukování (předlisek vyráběný vytlačováním)
7.3. Vyfukování s dloužením
7.4. Speciální způsoby výroby dutých těles
7.4.1. Rotační natavování
7.4.2. Vyfukování z fólií
7.4.3. Rotační navíjení
7.5. Stroje a zařízení pro výrobu dutých těles
7.6. Nástroje pro vyfukování
7.
vyfukování, výroba dutých těles
Vyfukováním se rozumí takový postup, při kterém je polotovar
(předlisek) tvarován ve vyfukovací formě přetlakem vzduchu
do tvaru více méně uzavřeného tělesa. Materiál se musí zahřát do
plastického stavu, kdy hmota vykazuje potřebnou
tvarovatelnost, ale přitom si ještě udržuje dostatečnou soudružnost. Polotovarem může být
předlisek vyráběný vstřikováním, vytlačováním nebo i
fólie. Vyfukováním se zpracovávají hlavně PE a PP (asi ¾
produkce), PVC a jeho kopolymery a v poslední době PET. V malé
míře jsou zastoupeny další termoplasty, jako např. POM, PC,
kopolymery PS a jiné.
Rozdíly mezi nejrozšířenější technologií – vstřikováním a
vytlačováním jsou následující:
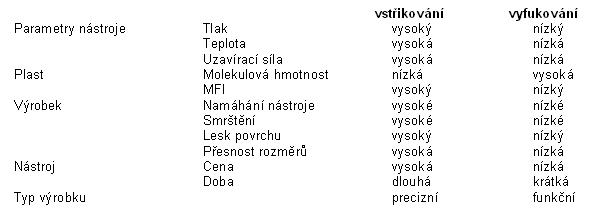
7.1.
Vstřikovací vyfukování
(předlisek vyráběný vstřikováním)
Vstřikovací vyfukování
se používá k výrobě dutých těles menších rozměrů a s velmi
členitým tvarem. Postup je následující: ve
vstřikovací formě se
nastříkne na speciálně upravený, obvykle ocelový, trn
v dutině vstřikovací formy tavenina vhodného plastu. Tím je
vytvořen polotovar a to včetně dna a kompletního hrdla, např. se
závity budoucí láhve. Dále se postup liší podle toho, zda je
výlisek tvářen ihned nebo je proces vyfukování zcela oddělen.
V prvém případě se ihned po nastříknutí plastu, dokud je hmota
ještě v plastickém stavu, trn přenese do formy nebo se naopak
forma přisune k předlisku po odsunutí vstřikovací formy.
Následuje vyfouknutí stlačeným vzduchem do tvaru tvarové dutiny
formy, ochlazení a ztuhnutí plastu,
otevření nástroje a vyhození (sejmutí) z trnu stlačeným
vzduchem a celý cyklus se opakuje. Tento postup má výhody v tom,
že pokud se používá živý vtok, tak neexistuje technologický
odpad, hrdlo se závitem i dno mají vysokou kvalitu, neboť
neobsahují svar; lze vyrábět předlisky s proměnnou tloušťkou
stěny a tak dosáhnout u odstupňovaných výrobků rovnoměrnou
tloušťku stěny, lepší vzhled, tuhost a biaxiální orientace
zlepšuje mechanické vlastnosti a snižuje propustnost pro plyny.
Nevýhodou je potřeba dvou forem, složité výrobní zařízení a
plast musí být vhodný jak pro vyfukovaní, tak i pro vstřikování.
Velikost
výrobků je omezena velikostí
předlisku. Ve druhém případě lze proces oddělit.
Vstřikováním se vyrobí předlisky, normálně se ochladí a v druhé
firmě se potom opět ohřejí do plastického
stavu a vyfouknou. Oblast hrdla se závitem se nezahřívá.
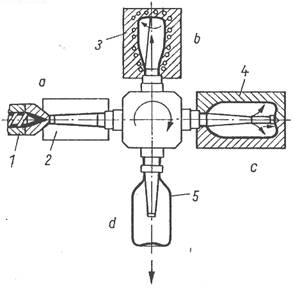
Princip vstřikovacího vyfukování s okamžitým vyfouknutím
1 – vstřikovací stroj, 2 – vstřikovací forma, 3, 4 – vyfukovací forma, a – vstřikování, b – vyfukování, c – chlazení, d – vyhození
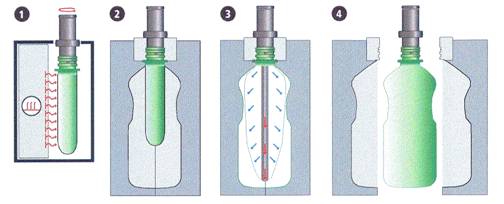
Princip vstřikovacího vyfukování s přerušovaným procesem
1 – ohřev tvarové části předlisku, 2 – přesun do vstřikovací formy, 3 – vyfukování,
4 – chlazení, vyhození
7.2.
Vytlačovací vyfukování
(předlisek vyráběný vytlačováním)
Je to nejrozšířenější způsob výroby dutých těles. Na vytlačovacím
stroji s přímou
nebo
příčnou vytlačovací hlavou se vytlačí polotovar –
parizon. Tato trubka, schopná plastického přetvoření, se
odstřihne v okamžiku, jakmile dosáhne požadované délky. Střižné
nůžky jej buď podrží do okamžiku, dokud nepřijede vyfukovací
forma nebo jej přenese do formy, kde je nasazen na trn. Zavřením
formy dojde k vylisování hrdla a vnitřního průměru a ke svaření
dna. Následně se přivede stlačený vzduch a dojde k vyfouknutí.
Po
ochlazení a ztuhnutí se výrobek sfoukne a odstraní se
přetoky od svarových ploch. Kromě možnosti používání
vyfukovacího trnu se v omezené míře používá i vyfukovací jehla,
která se zapíchne do parizonu. Tato část se později odstraní.
Nevýhodou vytlačovacího vyfukování je malá přesnost výrobků a
poměrně velký odpad, vznik svaru. Výhodou je ekonomie provozu a
možnost vyrábět výrobky o mnohem větším objemu.
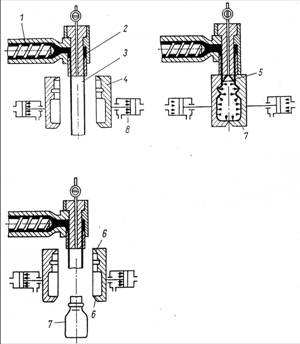
Princip vytlačovacího vyfukování
1 – vytlačovací stroj, 2 – příčná hlava, 3 – parizon, 4 – vyfukovací forma, 5 – vzduch, 6 – svařovací hrany,
7 – výrobek, 8 – uzavírací mechanismus
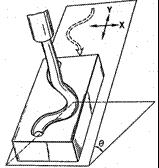
Princip podtlakového ukládání parizonu do tvarové dutiny formy
Dále se používají metody „ukládání“ parizonu pomocí podtlaku do
tvarové dutiny formy a dodatečného tvarování za účelem výroby
nepravidelného dutého tvaru. V prvém případě je vytlačený
parizon přisáván podtlakem do tvarově složité formy, neboť
samotný parizon by nebyl schopen po vytlačení zaujmout tak
proměnný tvar. Ve druhém případě je postup zcela odlišný.
V prvním kroku dojde k vytlačení parizonu, jehož konec je
rozdílnými způsoby „svařen“. Následuje přivedení vzduchu o
přesně stanoveném tlaku a vyfouknutí do rukávu, aby nedošlo ke
slepení stěn.
V posledních krocích je výrobek dotvarován pomocí nástroje.
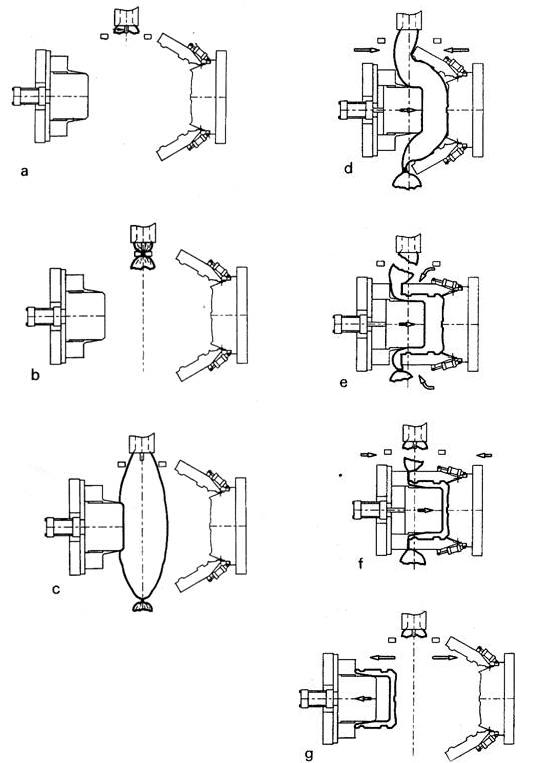
Princip vytlačovacího vyfukování s dotvarováním
Vzduch může být do formy přiváděn buď hrdlem láhve, dutým
trnem hlavy vytlačovacího stroje nebo jehlou.
Podle umístění to může být buď shora, zdola nebo
z boku. U vyfukování zdola se šnek vytlačovacího stroje
neustále otáčí a vytlačuje další
parizon. Proto musí být fáze vytlačování a fáze vyfukování
přesně sladěny, aby v okamžiku, kdy se uvolní forma, dosáhla
délka parizonu optimální délky (minimální odpad). Jinak by došlo
k protažení parizonu a ztenčení stěny. U vyfukování shora forma
sevře parizon a svaří ho dole. Nahoře je volná část parizonu, do
které se zatlačí trn a kalibruje ho. Při vyfukování zdola je
kvalitnější hrdlo, při vyfukování shora je kvalitnější dno
v důsledku protahování parizonu.
K nejdůležitějším technologickým parametrům vyfukování patří
teplota a tlak. Z hlediska vlastností výrobků je
vhodné používat teplotu co nejvyšší, ale dochází k velkému
protahování parizonu, nárůstu
smrštění a doby chlazení. Při nízké teplotě není záruka
kvalitního svaru ve dně a zhoršují se mechanické vlastnosti.
Tlak vzduchu při vyfukování bývá v rozmezí 0,4 až 1 MPa a
stlačený vzduch musí působit na vyfouknutý parizon po celou dobu
chladnutí, aby nedošlo k deformacím. Teplota formy se udržuje
mezi 30 až 60 oC. Typická provozní data pro šnekový
vytlačovací stroj jsou uvedena v tabulce.
Doporučené technologické parametry pro vytlačovací stroj a technologii vyfukování
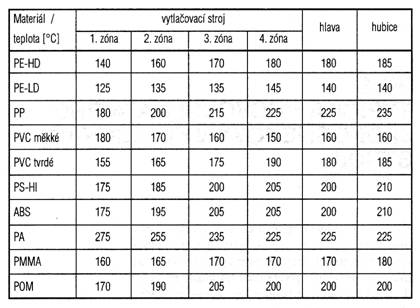
Speciálním případem vytlačovacího vyfukování je výroba
vícevrstvých dutých těles, jejichž stěna se skládá
alespoň ze dvou plastů. Princip je založen na koextruzi, kdy
samostatné šnekové plastikační jednotky přivádějí taveniny
plastů do
společné vytlačovací hlavy tak, aby nedošlo ke smísení
tavenin polymerů a aby se vyrobil vícevrstvý parizon. Další
technologií je výroba spotřebních výrobků z lehčeného PS.
Zde se používají fyzikální i chemická nadouvadla. Pro chlazení
se kvůli špatnému odvodu tepla používá kapalný dusík.
7.3.
vyfukování s dloužením
Tato technologie využívá výhody, které byly popsány při
orientaci
fólií.
Dloužením lze zvýšit průhlednost, pevnost, houževnatost
a snížit propustnost pro plyny a páry. Princip výroby spočívá
v tom, že
předlisek (ať už vstřikovaný nebo vytlačovaný) je před
vyfouknutím temperován na vhodnou teplotu v kaučukovité oblasti
(pro PP 150 až 155 oC, pro PET 90 až 95 oC,
atd.), poté je nadloužen (naorientován) a vyfouknut. Tato
technologie slouží především pro výrobu lahví o malých objemech.
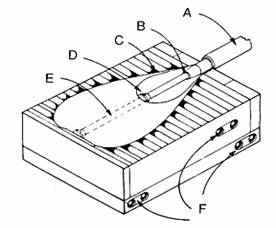
Výroba dutých těles dloužením
A - vyfukovací a dloužící jehla, B – přívod vzduchu, C – odvzdušnění nástroje, D – předlisek, E – nadloužený tvar. F – chladící kanály
7.4.
Speciální způsoby výroby dutých těles
Mezi speciální způsoby výroby dutých těles patří rotační
natavování, vyfukování z fólií, rotační navíjení.
7.4.1.
Rotační natavování
Dutá tělesa velkých objemů, až několika set litrů, se s
výhodou vyrábějí rotačním spékáním práškových polymerů.
Do
dvoudílné kovové formy, která může být jen z plechu, protože
není vystavena žádnému zvláštnímu namáhání, se odměří potřebné
množství práškového termoplastu, např. PE, ale i PP, PVC, EVA,
PS, atd. Potom se forma uvede do rotačního pohybu kolem dvou na
sebe kolmých os. Tím se prášek rovnoměrně rozděluje po vnitřním
povrchu formy.
Forma se ve vytápěné komoře ohřívá vzduchem na teplotu
vyšší, než je teplota tání příslušného plastu. Vzduch mívá
teplotu 260 až 450
0C.
Z prášku se postupným tavením a spékáním vytváří souvislá vrstva
o tloušťce 1,5 až max. 30 mm.
Formy rotují poměrně pomalu, kolem menší osy rychlostí asi
40 ot.min-1, kolem větší osy asi 12 ot.min-1.
Po dokonalém protavení a spečení prášku se forma přesune do
chladicí komory, kde se ochlazuje např. zkrápěním vodou. Pracovní cyklus
je poměrně pomalý a závisí na velikosti výrobku a na tloušťce
jeho stěny. U malých nádob trvá několik minut, u nádob s objemem
500 l asi jednu a půl až dvě hodiny. K přednostem této metody
patří levné strojní zařízení, laciná forma a možnost vyrábět i
tvarově členité výrobky. Nevýhodou je dlouhý výrobní cyklus a
vysoká cena práškových polymerů.
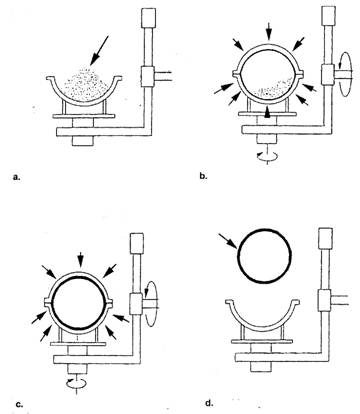
Princip, schéma rotačního natavování
a – plnění, b – ohřev a rotace formy, c – chlazení, d – vyjmutí výrobku
7.4.2. Vyfukování z fólií
Výroba
dutých těles z fólií je založena na následujícím
principu: Dvě fólie z termoplastu jsou pevně sevřeny čelistmi
kovové formy a mezi ně se přivádí pod tlakem horký vzduch nebo
horká vodní pára. Teplem se plast převede do plastického stavu a
tlakem se fólie vytvarují podle dutiny formy. Po okrajích se
současně svaří. Tlustší fólie se mohou zahřát ještě před
vložením do formy. Tímto způsobem se vyrábějí obaly např. pro
čisticí prostředky. Pro obaly je charakteristický podélný svar
buď po celém obvodu, nebo jen na třech stranách, jestliže se
použije jedné fólie, která se před vložením do formy podélně
ohne. Způsob má řadu variant. Místo celoplastové fólie se
používají kombinované materiály, např. papír s jednou vrstvou
polyetylénu. U systému Tetra-Pack se nejprve podélným svarem
vytváří trubka, která se uzavře příčným svarem. Potom se plní
obsahem a uzavře se druhým příčným svarem, který je proti prvému
otočen o 900. Plášť obalu je tvořen čtyřmi
trojúhelníky a tvoří čtyřbokou pyramidu. Podobně se vyrábějí pro
stejné účely i hranaté krabice.
7.4.3. Rotační
navíjení
Jedná se v podstatě o výrobu
laminátu, kdy mohou být aplikovány dva rozdílné postupy.
V prvním případě jsou na rotační formu navíjena výztužná vlákna
(ideálně pod úhlem 45o), která jsou následně
impregnována a vytvrzována pro vytvoření dostatečné vrstvy.
V druhém případě je na nosné těleso navíjena výztuž, která je
naimpregnovaná pryskyřicí, která se dále vytvrzuje.
7.5.
Stroje a zařízení pro výrobu dutých těles
Požadavky na strojní zařízení jsou následující: regulovatelná
teplota komory a co nejmenší kolísání teploty taveniny,
vytlačovací hlava musí umožňovat správné nastavení tloušťky,
snadná výměna hubice, šnek musí pracovat bez pulsací, aby nebyly
v parizonu bubliny a byl konstantní průřez a zavírací
mechanismus musí umožňovat co nejjednodušší výměnu forem a nesmí
pootevřít nástroj během vyfukování. Zařízení pro vyfukování
dutých těles se skládá ze
šnekového vytlačovacího stroje – viz kap. 6 (většinou
horizontálního) vybaveného
příčnou vytlačovací hlavou s kruhovou hubicí a z vyfukovací
jednotky, sestávající ze zavíracího (mechanické způsoby
uzavírání – klika, zuby, hřeben, páka, klíny, hydraulický způsob
uzavírání) a vyfukovacího mechanismu včetně formy.
Stroje pro vyfukování se dělí na stroje se zásobníkem (přerušovaný provoz -
poloautomatický) a stroje bez zásobníku (automatický provoz). Podle pohybu
formy se vyfukovací stroje dělí na stroje s vertikálním pohybem nebo
horizontálním pohybem se statickou nebo pohyblivou formou pro oba směry. Pro
vytlačování plastů s malou teplotní stabilitou, např. PVC, je výhodnější
vertikální stroj, který je ukončen přímou hlavou, kde jsou poměry pro tečení
příznivější. Šneky mívají jen krátkou dopravní a kompresní část, ale dlouhou
část hnětací. Celková délka šneku je 15 až 20 D. Plastikační kapacita
vytlačovacího stroje musí být v souladu s kapacitou vyfukovací jednotky.
Množství vytlačeného plastu závisí na konstrukci stroje, geometrii šneku,
plastu a technologických podmínkách.
U moderních strojů je možné měnit tloušťku stěny parizonu
v závislosti na jeho délce – duté těleso nepravidelného tvaru
nebo těleso s proměnnou tloušťkou stěny. Tu lze měnit buď
axiálním pohybem trnu v hubici nebo naopak pohybem hubice při
konstantní poloze trnu, což je řízeno mikroprocesorem. Další
možností je přitlačování prstenců v hubici na parizon a tím
změna tloušťky. Při nastavování rozměru
parizonu se musí pamatovat na to, že tavenina plastu vlivem
stlačitelnosti zvětšuje svůj objem, což se projeví zvětšením
objemu i tloušťky. To závisí na technologických podmínkách –
teplotě a tlaku. Zvětšení rozměrů dosahuje až několika desítek
procent.
7.6. nástroje pro vyfukování
Vyfukovací formy je možné podle velikosti výrobku a
použitého materiálu a zařízení konstruovat jako jednonásobné
nebo vícenásobné. Formy pro menší výrobky jsou dvoudílné a pro
větší výrobky mají tvarové díly složeny z více částí. Příklad
vyfukovací formy je na obrázku. Protože z celkové doby
pracovního cyklu představuje doba chlazení nejdelší úsek (uvnitř
výrobku není dobrý vodič tepla), chlazení je provedeno buď
cirkulující vodou, nebo pomocí vnitřního chlazení vodní mlhou,
kapalným dusíkem, CO2, apod.
Odvzdušnění forem je nutné kvůli malým vyfukovacím tlakům a dělá
se proto, aby nedocházelo k vadám – nedotvarování tvaru, matný
lesk, nepravidelné důlky, apod. Ve většině případů stačí
k odvzdušnění netěsnosti v dělící rovině. Pro lepší odvzdušnění
se do vyfukovací formy umísťují odvzdušňovací štěrbiny nebo
odvzdušňovací válcové vložky se sraženou hranou nebo
šestihranem.
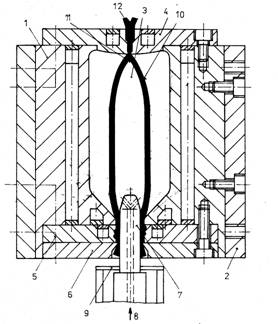
Příklad vyfukovací formy
1 – tvárnice, 2 – upínací deska, 3 – dělící rovina, 4 – dno, 5 – hrdlo, 6 – kalibrační deska, 7 – trn, 8 – vzduch,
9 – stírací deska, 10 – parizon, 11 – svar, 12 – přetok
Samostatnou část v konstrukci vyfukovacích forem představují
svařovací plochy (hrany), které vytvářejí svary u dna a
hrdla dutých výrobků. Vzniklý svar musí být dostatečně pevný.
Dosahuje se toho tak, že se vhodně upravuje úhel a tvar
svařovací částí formy. Velký úhel a široká plocha nedávají dobré
svary. Vhodný úhel způsobuje, že se část hmoty vtlačuje zpět do
formy – dochází k zesílení a ke zvýšení plochy pro zatížení. Pro
LEPE bývá úhel 12 až 15° zatímco pro POM je úhel 35 až 45°.
Minimální úhel musí být 5°. Šířka svařovacích ploch bývá 0,2 až
3 mm podle velikosti dílů a podle plastu. Mezi svařovacími
hranami musí po zavření formy zůstat mezera 0,2 až 0,5 mm
vyplněná stlačeným plastem – zde se oddělí
přetok.
Svařovací hrany jsou vytvářeny na kalených vložkách, které
se šrouby a kolíky upevňují na formy.
.: Jdi na začátek stránky :.
|