- Vytlačování
6.1. Vytlačování trubek a profilů
6.2. Výroba fólií a desek vytlačováním
6.2.1. Výroba tenkých fólií
6.2.2. Výroba orientovaných (dloužených) fólií
6.2.3. Výroba desek vytlačováním
6.2.4. Výroba fólií vyfukováním
6.3. Speciální způsoby vytlačování
6.3.1. Výroba pásků a vláken z fólií
6.3.2. Výroba vláken vytlačováním
6.3.3. Oplášťování vytlačováním
6.3.4. Tvorba povlaků vytlačováním
6.3.5. Granulace vytlačováním
6.3.6. Výroba napěněných trubek, profilů, desek, fólií
6.4. Stroje pro vytlačování
6.4.1. Šnekové vytlačovací stroje
6.4.2. Pístové vytlačovací stroje
6.4.3. Diskové a spirálové vytlačovací stroje
6.5. Konstrukce vytlačovacích hlav
6.5.1. Přímé vytlačovací hlavy
6.5.2. Nepřímé vytlačovací hlavy
6.5.3. Širokoštěrbinové vytlačovací hlavy
6.5.4. Speciální vytlačovací hlavy
Vytlačování je technologická operace, při které je tavenina plastu kontinuálně
vytlačována přes profilovací zařízení (vytlačovací hlavu) do
volného prostoru. Technologie vytlačování slouží k výrobě buď
konečných tvarů nebo k výrobě polotovarů. Podle tvaru konečného
výrobku nebo tvaru polotovaru se technologie vytlačování mohou
rozdělit do tří základních skupin:
Tyto technologické způsoby využívají hlavně
šnekové vytlačovací stroje, které však nepracují samostatně,
ale jsou součástí výrobních linek, kde ostatní stroje a zařízení
zajišťují
odtah,
kalibraci, doplňkovou úpravu tvaru nebo povrchu, apod.
Linka na vytlačování uzavřených i otevřených
profilů a
trubek se skládá ze šnekového vytlačovacího stroje,
vytlačovací hlavy a ze zařízení měřicího, kalibračního,
chladicího, odtahovacího, dělicího a navíjecího resp.
odkládacího. Běžně se používají
jednošnekové vytlačovací stroje, neměkčený PVC se vytlačuje
na
dvoušnekovém vytlačovacím stroji. K výrobě trubek se obvykle
používá PVC, HDPE a LDPE, méně PP a PA.
Profily se vyrábějí z PVC, PS a jejich kopolymerů, PMMA, PC,
POM, apod.
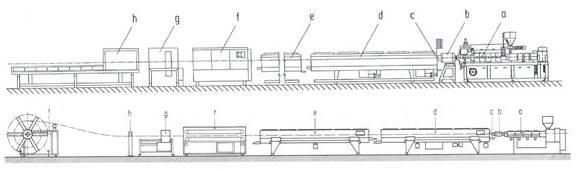
Linka na výrobu trubek z PVC (nahoře) a PP (dole)
a – vytlačovací stroj, b –vytlačovací hlava, c – kalibrace, d – kalibrační jednotka, e – chlazení,
f – měřící zařízení, g – dělící zařízení, h – odkládací zařízení, i – navíjení

Linka na výrobu profilů z neměkčeného PVC
a – násypka, b – dvoušnekový vytlačovací stroj, c – kontrola, d –vytlačovací hlava a kalibrace,
e – kalibrační podtlaková jednotka, e – chlazení, f – měřící zařízení, g – dělící zařízení, h – kontrola, i – odkládací zařízení
Účelem
kalibračního zařízení je ochladit vytlačovaný profil nebo
trubku tak, aby získal požadovaný stabilní tvar a rozměr.
Kalibrační zařízení pro výrobu trubek a profilů je buď
přetlakové, podtlakové nebo průvlakové. Přetlaková kalibrace se
používá pro kalibraci trubek větších průměrů nebo uzavřené
profily, které příliš nemění svůj tvar. Vzduch o přetlaku okolo
0,075 MPa se přivádí přes rozdělovač a trn do trubky a ta je
tímto přitlačována k chlazenému kalibračnímu pouzdru. V trubce
je umístěna zátka, která je uchycena k hlavě mechanicky drátem,
lankem nebo řetězem, resp. elektromagnetem a která umožňuje malý
průnik vzduchu, aby se trubka chladila také z vnitřku. Přetlak
vzduchu je pro malé trubky větší, než pro velké trubky. Při
přetlakové kalibraci je přetlakové pouzdro připojeno k čelu
hlavy. Ke zmenšení tření se používá tzv. mazací vzduch.
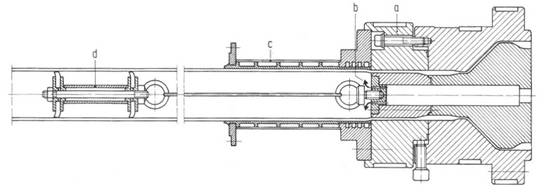
Přetlaková kalibrace
a – vytlačovací hlava, b – přívod vzduchu, c – kalibrační pouzdro, d - zátka
Přetlaková kalibrace a podtlaková kalibrace je také vhodná pro
výrobu
zvlněných trubek, kde kalibrační pouzdro tvoří řetězy
s tvárnicemi.
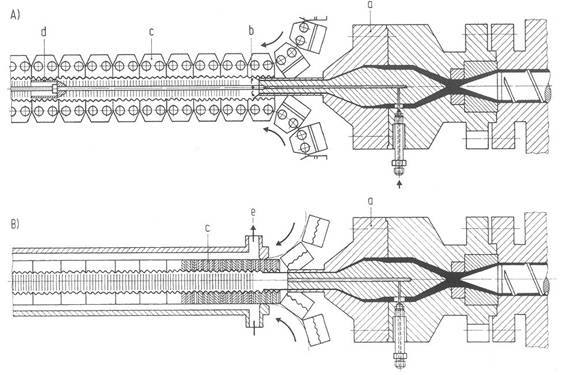
Vytlačování vlnitých trubek s přetlakovou (nahoře) a podtlakovou kalibrací (dole)
a – vytlačovací hlava, b – trubka, c – články s půlkruhovýmí žlábky (negativ tvaru), d – zátka, e – odsávání vzduchu
Nejběžněji používaným typem kalibračního zařízení je vakuová
(podtlaková) kalibrace, neboť odpadají problémy s uzavíráním
trubky. Kalibrace nastává přisáváním trubky ke kalibračnímu
pouzdru. Povrch trubky se dotykem s pouzdrem ochladí a tvar
zůstává zachován.
Trubky se vytlačují o 1 až 3 % větší, než je požadovaný
průměr. Vakuová kalibrace je vhodná pro menší průměry a pro
výrobky s tenčí stěnou.
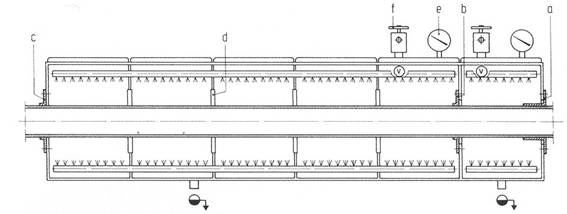
Vakuová kalibrace s kalibračními pouzdry
Novější systém pracuje s kalibračními pouzdry, rozdělenými do
více částí. V první části je na vstupu do komory předchlazení
kruhovým prstencem následované nestejnoměrně rozmístěnou sadou
deskových průvlaků nebo trubkovým kalibračním pouzdrem. V druhé
části komory je opět rozmístěna sada průvlaků, ale stejnoměrně a
ve větších vzdálenostech mezi sebou.
Průchody trubky mezi částmi komory a ven z komory jsou utěsněny
elastickými manžetami nebo zahlceny vodou. Trubka je chlazena
vodou sprchováním z trysek pootočených proti sobě o 120o
a osově přesazených. Víka obou částí kalibrační komory jsou
utěsněna vzniklým podtlakem. Délka kalibrační komory je různá a
závisí na tvaru výrobku, tloušťce stěny, průměru trubky a
dosahovaném výkonu vytlačovacího stroje. Běžně se používají šest
metrů dlouhé kalibrační komory, kde vstupní část je dlouhá okolo
jednoho metru.
Pro výrobu plných
profilů se používá průvlaková kalibrace, která se
konstrukčně řeší tak, že kalibrační pouzdro je opatřeno
šroubovou drážkou, kterou protiproudně prochází chladicí voda a
ta ochladí povrch profilu natolik, že si uchová požadovaný tvar
a rozměr. Místo pouzdra se šroubovitým kanálkem lze ke kalibraci
použít sadu průvlaků s odstupňovanými rozměry. Tuto kalibraci
lze použít i pro kalibrování tlustostěnných
trubek a otevřených profilů.
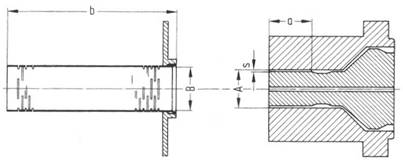
Průvlaková kalibrace
Kalibrační zařízení se obvykle doplňuje o
chladicí zařízení, ve kterých se výrobek dochlazuje na
takovou teplotu, aby nedocházelo k jeho nevratným deformacím v
dalších zařízeních vytlačovací linky. Chlazení se provádí buď
ponorem ve vodě, nebo sprchováním jako v kalibrační komoře.
Rychlost posuvu vytlačovaného profilu se nastavuje a reguluje
odtahovacím zařízením, které k odtahování používá řetězy,
kotouče, pásy nebo článkové pásy, kdy každý článek je na
pracovní ploše opatřen vrstvou pryže. Odtahovací zařízení jsou
konstrukčně řešena tak, aby se jejich výška od základny dala
seřizovat podle ostatních strojů v lince, které se ovšem také
seřizují, a to podle výšky vytlačovací hlavy (osy profilu) od
základny.
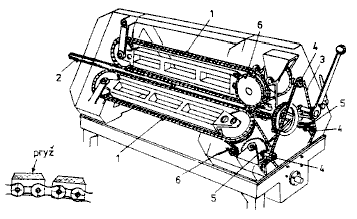
Řetězový odtah
Dělící nebo řezací zařízení bývá řešeno buď pomocí kotoučové
pily nebo sekáním tvarovaným nožem. Tvar nože závisí na tom, zda
je jeho pohyb posuvný nebo rotační. Pokud nedochází k dělení
výrobků na konečnou délku, tak např. u pružných výrobků, u
kterých nedochází při ohnutí k trvalé deformaci, následuje
navíjení na bubny nebo kotouče. Průměr navíjení by měl být
20krát větší, než průměr trubky.
Do vytlačovací linky zařazujeme
také zařízení, sloužící k měření, značení, manipulaci a k
úpravám výrobku. Z měřicích zařízení se většinou linka osazuje
délkoměrem (mechanickým nebo elektronickým), který slouží i k
ovládání dělicího zařízení. U linek na výrobu trubek se ve stále
větší míře začínají používat přístroje na měření průměru a
tloušťky stěny. Značící zařízení se používají pro označování
výrobku kvůli jeho identifikaci. Používají se přístroje typu ink-jet,
vytápěné kolečko, tisk přes pásku aj. Do linky se podle typu
výrobku zařazují ústrojí na tvarování (hrdlování trubek),
vysekávání, apod.
Desky jsou plošné útvary s tloušťkou větší, než jeden milimetr, tenčí jsou
fólie. Pro desky a fólie se k vytlačování používají
širokoštěrbinové hlavy, pro výrobu
fólií vyfukováním se používají tzv.
vyfukovací hlavy (příčné). Výrobky jsou buď konečné produkty
nebo polotovary a mohou se vyrábět i jako vícevrstvé. Fólie se
vyrábějí vytlačováním z PP, HDPE, PC, PA a PVC. Desky se
vyrábějí z PE, PP, ABS, PVC, PMMA.
Linka na vytlačování fólií je schematicky znázorněna na obrázku
viz níže. Skládá se z vytlačovacího stroje s
širokoštěrbinovou vytlačovací hlavou a vytlačovaný pás je
dále odtahován tříválcovým chladicím strojem. Fólie se vytlačuje
na chladicí válec. Podle polohy vytlačovací hlavy k chladicímu
válci lze měnit délku chladící dráhy. Povrch válců je leštěn
nebo chromován. Válce jsou temperovány na teplotu, která je
závislá na druhu zpracovávaného materiálu. Vnitřní vestavba
chladicích válců se řeší různými způsoby, které musí zajistit
rovnoměrné rozložení teplot po délce válce.
Rychlost ochlazování má vliv na kvalitu fólie, tj. na mechanické
vlastnosti, lesk, optické vlastnosti, apod. Proto je nutné
zajistit dobrý kontakt mezi plastem a válcem pomocí přítlačných
válců, vzduchovými noži, odsáváním vzduchu, elektrostaticky,
apod. U tenkých fólií (do tloušťky 0,2 mm) stačí kontakt
s chladícím válcem. U tlustších fólií (0,2 až 2 mm) je chlazení
oboustranné. Deska se dále dochlazuje na
válečkovém dopravníku. Ochlazená fólie prochází měřicím
zařízením. Okraje fólie se ořezávají kotoučovými ořezávacími
noži a fólie nebo desky se buď navíjejí, nebo sekají. Oříznuté
okraje se vracejí zpět ke zpracování. Měření tloušťky je
mechanické nebo bezkontaktní.
Navíjecí zařízení musí umožňovat změnu otáček při
narůstajícím objemu navinuté fólie. Všechna zařízení za
vytlačovacím strojem se obvykle ukládají na kolejnice z důvodu
snadné údržby jednotlivých strojů, snadného čistění vytlačovací
hlavy a demontáže šneku.
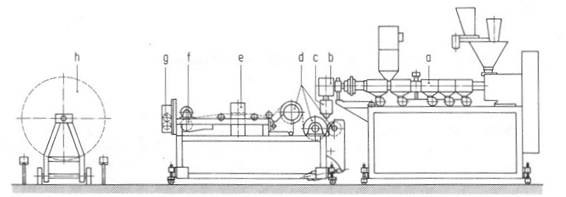
Linka pro výrobu tenkých fólií vytlačováním
a – vytlačovací stroj, b – adaptér, c – vytlačovací hlava, d – chladící válce s odtahem,
e – měření tloušťky, f – úprava povrchu, g – řezací zařízení, h - navíjení
Pro výrobu monoaxiálně nebo biaxiálně
orientovaných fólií se do linky zařazuje za chladicí válce
zařízení na monoaxiální (podélný směr) nebo biaxiální (podélný i
příčný směr) dloužení fólie. Fólie je předehřáta na vhodnou
teplotu, naorientována a ochlazena. Orientace je buď součástí
linky nebo je samostatnou operací. Při monoaxiálním dloužení se
znovu nahřátá fólie dlouží různou obvodovou rychlostí válců, což
způsobuje nárůst pevnosti ve směru dloužení. Výroba biaxiálně
dloužených fólií se provádí buď jednostupňovým nebo
dvoustupňovým procesem.
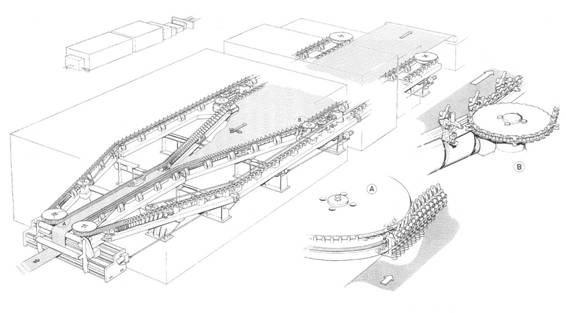
Dvoustupňový proces dloužení biaxiálních fólií
Při dvoustupňovém procesu se předehřátá monoaxiálně orientovaná
fólie zachycuje do svěrek, které jsou symetricky uchyceny na
dvou nekonečných řetězech a které dále fólii dopravují.
Zvětšováním vzdálenosti mezi řetězy se fólie dlouží v příčném
směru a následně v podélném směru. Příklad teplotních profilů je
ukázán na obrázku. Výhodou dvoustupňového procesu je možnost
rozdílného dloužení v podélném a příčném směru, automatizace a
jednoduchost linky.
Při jednostupňovém procesu se zvětšuje nejenom vzdálenost mezi
řetězy, ale i vzdálenost mezi jednotlivými svěrkami a tím se
dosahuje biaxiálního dloužení. Výhodou je izotropní struktura,
bezkontaktní proces a nižší spotřeba energie.
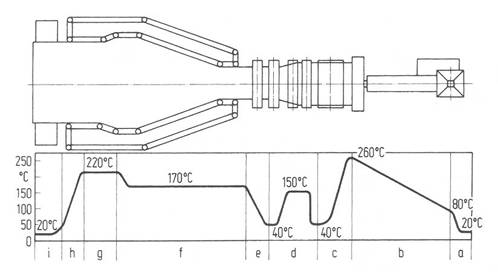
Teplotní profily při výrobě biaxiálně orientovaných PP fólií
a - předehřev, b – vytlačování, c - chlazení, d – podélné dloužení, e – ohřev, f – příčné dloužení, g – tepelná stabilizace,
h – chlazení, i - navíjení
Linka pro výrobu desek je svou konstrukcí blízká linkám na
výrobu fólií a tenkých desek.
Skládá se z vytlačovacího stroje s vytlačovací hlavou.
Vytlačovaný pás je odtahován většinou tříválcovým chladicím
strojem. Povrch válců je přizpůsoben požadované kvalitě povrchu
desek (leštěný nebo leskle chromovaný, dezénovaný, matovaný,
atd.). Válce jsou obvykle temperovány horkou tlakovou vodou na
teplotu, která je závislá na druhu zpracovávaného materiálu.
Režim chlazení musí být přísně řízen kvůli minimálnímu vnitřnímu
pnutí. Deska se dále dochlazuje na válečkovém dopravníku, před
odtahem ořezává, a za ním příčně dělí a ve stohovacím zařízení
ukládá na paletu.
Speciální technologií je vytlačování desek resp.
fólií do vodní lázně, ale její použití je omezené v důsledku
nedokonalého povrchu vlivem pohybu povrchu chladící vody.
Technologie výroby fólií vyfukováním je založena tom, že trubka
s tloušťkou stěny 0,5 až 2 mm je ještě v plastickém stavu
nafouknuta stlačeným vzduchem (zvětšení 2krát až 5krát) a
zároveň protažena odtahovacím zařízením (až 5ti násobné podélné
protažení).
Vyfouknutá fólie, o běžné tloušťce stěny 0,015 až 0,3 mm, je
ochlazena a navinuta.
Vyfukováním
se vyrábějí fólie z LDPE, HDPE a PP, PVC, PA a PET.
Vyfukováním se vyrábějí i
vícevrstvé fólie o různé materiálové skladbě. Dnes se
vyrábějí až sedmivrstvé fólie. Konstrukčně jsou vytlačovací
hlavy pro vícevrstvé fólie velmi složité a také výroba fólií na
nich je velmi náročná na dodržování technologické disciplíny. V
současnosti se na trhu objevilo konstrukční řešení, umožňující s
jedním vytlačovacím strojem vyrábět vícevrstvé fólie. Linka na
výrobu fólií vyfukováním může mít v podstatě tři varianty viz
obrázek.
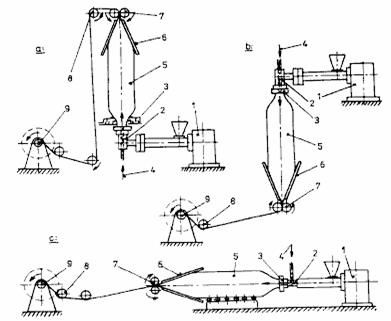
Výroba fólií vyfukováním
a – horní odtah, b – spodní odtah, c – horizontální odtah, 1 - vytlačovací stroj, 2 - hlava, 3 - chladící prstenec,
4 - vstup přetlakového vzduchu, 5 - fólie, 6 - skládací desky, 7 - odtahovací válce, 8 - vodící válečky, 9 – navíjení
Nejčastěji se používá varianta s horním
odtahem fólie. Vytlačovací stroj je osazen
vyfukovací hlavou. Vytlačovaná fólie se určeným přetlakem
(0,15 až 1 kPa) vyfoukne a chladí vzduchem, který se přivádí
chladicím prstencem a rovnoměrně ofukuje fólii po celém obvodu.
Získání rovnoměrné tloušťky je podmíněné bezproblémovým
chlazením. Vzduch do rukávu se přivádí přes vytlačovací hlavu.
Vyfouknutý rukáv se postupně ochlazuje a zplošťuje mezi
skládacími deskami a uzavírá
odtahovacími válci. Vzdálenost mezi odtahovými válci a
vytlačovací hlavou je nastavitelná a závisí na tloušťce
vyfukované fólie a typu zpracovávaného materiálu. Odtahovací
válce jsou obvykle opatřeny vrstvou vodivé pryže, aby bylo možno
odvádět statický elektrický náboj. Odtahovou rychlost je možno
regulovat a tím ovlivňovat tloušťku a podélnou orientaci fólie.
Na vodicím válci se může fólie jednostranně nebo oboustranně
ořezávat. Před vodicí válec se někdy zařazuje zařízení na
povrchovou úpravu fólie pro potiskování. Na konci linky se
umísťuje
navíjecí ústrojí. Uspořádání linky umožňuje manipulaci s
vytlačovacím strojem a navíjením v jedné rovině. Nevýhodou je
složitější zavádění fólie a horší chlazení v důsledku působení
tepla od vytlačovací hlavy, které se zvyšuje jak úpravami pro
chlazení rukávu z vnějšku, tak i z vnitřku. Konstrukčně se
účinnost chlazení zvyšuje, např. vodou chlazenými deskami nebo
prstenci umístěnými vně rukávu, chlazením chladicího vzduchu
nebo odsáváním ohřátého vzduchu z vnitřku rukávu.
Obdobné uspořádání má linka se
spodním odtahem, obvykle v nižším podlaží. Toto uspořádání
usnadňuje zavádění fólie a výhodou je i dokonalejší chlazení
rukávu samovolným prouděním vzduchu. Jinak linka obsahuje stejné
součásti jako linka s odtahem nahoře.
Linka s odtahem v horizontální rovině se používá především pro
zpracování materiálů citlivých na teplotu. Uspořádání linky
umožňuje jednoduchou konstrukci vytlačovací hlavy, na druhé
straně však musí být vyfouknutá fólie podpírána vodicími válci.
Tíhové zatížení a nerovnoměrné ochlazování rukávu zapříčiňuje
větší kolísání tloušťek fólie. Snaha odstranit nerovnosti v
tloušťce fólie vedla k aplikaci rotačního pohybu, a to i u
vertikálně situovaných linek. Rotačního nebo oscilačního pohybu
lze docílit buď natáčením vytlačovacího stroje, vytlačovací
hlavy, nebo odtahovým ústrojím. Z technických důvodů se rotace
vyvolává nejčastěji plynulým otáčením odtahového ústrojí nebo
konstrukčním řešením vytlačovací hlavy.
V této kapitole budou uvedeny ostatní vybrané
technologické způsoby vytlačování, jako je výroba vláken,
oplášťování, granulace, apod.
Pro výrobu vláken z HDPE, ale především z PP, se používá
následující technologický postup, využívající monoaxiálně
orientované fólie. Z vyfouknuté fólie nebo z fólie vytlačované
širokoštěrbinovou hlavou jsou na řezacím stroji nařezány
pásky, které se temperují a orientují v
dloužícím zařízení v poměru 1:7 až 9 na vysoce pevné pásky o
tloušťce v rozmezí 10 až 30
mm
a šířce v rozmezí 2 až 10 mm. Takto orientované pásky se
mechanicky štěpí na vlákna . Rozvlákňování je snazší pro
profilované pásky, pro hladké pásky je vhodné použít
válec s jehlami.
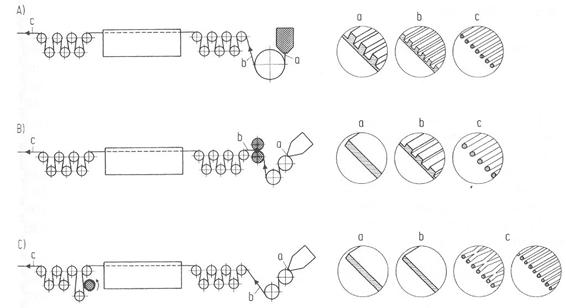
Technologie výroby vláken rozvlákňováním
A – vytlačená profilovaná fólie, B – profilování dezénovacími válci, C – rozvláknění ostrými jehlami
Linky na výrobu vláken vytlačováním jsou rozdílně sestavovány, a
to především podle typu zpracovávaného materiálu. Tímto způsobem
se vyrábějí silná vlákna z taveniny PP, HDPE, PA, PBT, PET, PMMA,
apod. Vytlačovací stroj je osazený
vytlačovací hlavou na vlákna. Z ní se vlákna vytlačují do
chladicí lázně, za kterou následuje první odtahovací zařízení.
Potom vlákna vstupují do temperační jednotky, kde se temperují
na teplotu vhodnou k jejich orientaci (dloužení) mezi
válci orientačního zařízení. Těchto temperačních a
dloužících jednotek může být do linky zařazeno i několik.
Orientační poměr se dá nastavovat. Běžně se pohybuje až do
hodnoty 1 : 9. Před navíjením se musí zorientované vlákno
rozměrově stabilizovat. Stabilizace se dosahuje ve stabilizační
lázni, ve které jsou vlákna udržována pod napětím druhým
odtahovacím zařízením. Za ním už následuje
navíjecí zařízení na cívky. Návin bývá buď válcový nebo
kuželový, nebo se vlákna navíjejí do přaden.
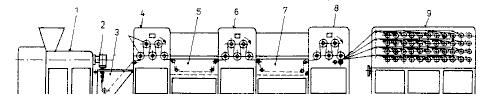
Linka na výrobu vláken vytlačováním
1 - vytlačovací stroj, 2 - vytlačovací hlava, 3 - chladicí lázeň, 4 - první odtahovací zařízení,
5 - temperační lázeň, 6 - orientační zařízení, 7 - stabilizační lázeň, 8 - druhé odtahovací zařízení, 9 - cívky
Uspořádání linky na
oplášťování se řeší s ohledem na druh zpracovávaného
materiálu a typ oplášťovaného předmětu. Většinou se oplášťují
vodiče a kabely, ale i ocelové trubky pro rozvody plynu, kovová
nebo polyamidová lanka jako prádelní šňůry nebo struny do žacích
strojků. Schéma linky na oplášťování vodičů termoplastickou
izolací je na obrázku. Vodič je z cívky odvíjen přes vodicí
kladky do předehřívacího zařízení. Nahřátý vodič vstupuje do
příčné oplášťovací hlavy. Vzniklý plášť se kalibruje,
ochlazuje v chladicí vaně, měří a kontroluje se soustřednost
pláště, průměr a jeho izolační vlastnosti. Oplášťovaný vodič je
odtahován synchronizovanými odtahovacími válci a přes vodicí
kladky je navíjen na cívku v navíjecím ústrojí. Při oplášťování
trubek PE a PP se do linky zařazuje před předehřev ústrojí,
které povrch trubky očistí a odmastí a opatří jej vrstvou
adheziva. Dále se do linky obvykle zařazují značící přístroje.
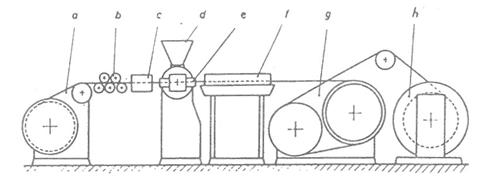
Linka na oplášťování vodičů
a - odvíjení, b - vodící kladky pro vedení a rovnání drátu, c – předehřev drátu, d - vytlačovací stroj,
e – oplášťovací hlava, f - chladící vana, g - odtah, h - navíjení
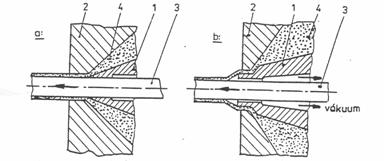
Kalibrace u technologie oplášťování
a – podtlaková kalibrace, b – přetlaková kalibrace, 1, 2 – vytlačovací hlava, 3 – drát, 4 – tavenina plastu
Kromě oplášťování drátů a vodičů lze nanášet povlaky z plastů i na
rozličné materiály, jako např. kovové fólie, textilie, jiné
plastové fólie, papír, apod. Stejně jako u vytlačování fólií
nebo vícevrstvých fólií i tady se využívá současného vytlačování
(koextruze) taveniny plastu (nejčastěji PE) na povrch nosného
materiálu, který má být povlakován. Následně je vytlačená
tavenina plastu slisována s nosným materiálem mezi chlazeným
bubnem a přítlačným pryžovým válcem. Předehřátý nosný materiál
je ve styku s přítlačným válcem, zatímco tavenina plastu je
chlazena na povrchu leštícího válce.
Schéma povlakování
6.3.5. Granulace vytlačováním
Výroba
granulátu se může uskutečňovat v podstatě dvěma způsoby,
které již byly částečně probrány v kapitole 3. a které se od
sebe liší zvolenou metodou granulace. Jedná se buď o granulaci z
vytlačovaných strun (pásku) nebo o tzv. granulaci na hlavě.
Granulace na hlavě je založena na tom, že vytlačovací stroj,
obvykle
dvoušnekový, je osazen tzv. vytlačovací
nožovou hlavou, což je v podstatě děrovaná deska, přes
kterou je materiál vytlačován a taky jsou na ní rotačním nožem
ořezávány granule (asi jako u mlýnku na maso). Granule jsou pak
ochlazovány vzduchem nebo vodou tak, aby nedocházelo k jejich
vzájemnému slepování. Obvykle se těchto chladicích médií využívá
i k transportu vyrobených granulí k jejich dalšímu zpracování.
Granule vyrobené tímto způsobem mají svůj charakteristický tvar
čoček nebo pecek.
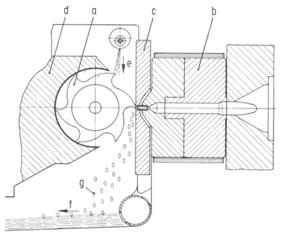
Granulace na hlavě
a – sekací nožová hlava, b – vytlačovací hlava, c – děrovaná deska, d – granulační zařízení,
e – ochlazovací směs, f – pásový dopravník, g - granule

Granulace ze strun (za studena)
A – schéma linky: a – vytlačovací hlava, b – chladící vana, c – vedení strun, d – termostat, e – sušící vzduch,
f – sekání strun, B – detail granulace: a – sekací rotor, b – statorové nože, c – válečky pro vedení, d - přítlačné válečky, e - motor
Schéma linky na
výrobu granulátu ze strun je znázorněno na obrázku.
Vytlačovací stroj vytlačuje přes strunovou vytlačovací hlavu
struny o průměru (tloušťce) cca 3 mm, které jsou vedeny přes
chladicí lázeň k odtahovacímu zařízení a následně
granulovány. Typ granulovacího stroje musí být zvolen podle
toho, zda se vytlačuje struna nebo pásek. Granule vyrobené ze
strun mají svůj charakteristický tvar válečku (krychle).
Problémem je zde vysoký obsah vlhkosti v granulátu, který se
musí sušit.
6.3.6. Výroba napěněných
trubek, profilů, desek, fólií
Vytlačováním se připravují napěněné produkty z PS,
LDPE, PP a PVC ve formě většiny typů polotovarů a výrobků, které
slouží jako izolační materiály. Jako přísada do plastů se
používají různá fyzikální nebo chemická nadouvadla. Proces může
být buď jednostupňový, kdy granulát obsahuje již nadouvadlo a
k výrobě bude použit vlastní proces vytlačování, nebo
dvoustupňový, kdy nejdříve dochází ke smíchání plastu a
nadouvadla a teprve potom ve druhém kroku nastává vytlačování.
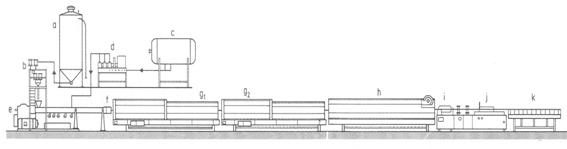
Linka na výrobu vypěňovaných trubek
a – silo z plastem, b – míchací jednotka, c – tank s nadouvadlem, d – dávkovač nadouvadla, e – vytlačovací stroj,
f – vytlačovací hlava, g – chladící lázně, h – sušení, i – kontrola rozměrů, j – řezání, k – stohování
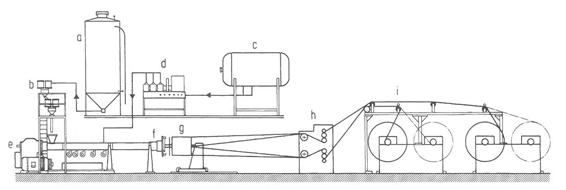
Linka na výrobu vypěňovaných desek
a – plast, b – míchací jednotka, c – tank s nadouvadlem, d – dávkovač nadouvadla, e – vytlačovací stroj, f – vytlačovací hlava,
g – kalibrace, h – čtyřválec, i – navíjení
Vlastní napěnění nejčastěji nastává snížením tlaku
taveniny při výstupu z vytlačovací hlavy, kdy se může projevit
narůstání objemu, ke kterému by mělo dojít ve všech směrech.
Pro snížení tření při kalibraci se používá vzduch. Někdy se
aplikují postupy dodatečné expanze při zahřátí vytlačených
výrobků ve vypěňovacích komorách. Vyrábět lze i vícevrstvé
produkty nebo laminované výrobky.
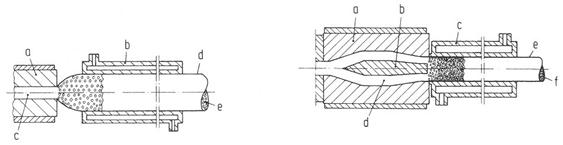
Výroba plných (vlevo)
a – vytlačovací hlava, b – kalibrace, c - tavenina s nadouvadlem, d – povrch, e – napěněné jádro
Výroba
dutých napěněných výrobků (vpravo)
a - vytlačovací hlava, b – torpédo, c - kalibrace, d - tavenina s nadouvadlem, e – kompaktní povrch, f – napěněné jádro
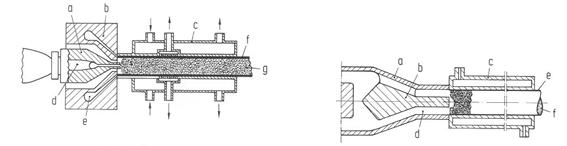
Výroba vícevrstvých výrobků (vlevo)
a, b – vytlačovací hlava, c – kalibrace, d – tavenina s nadouvadlem, e - tavenina bez nadouvadla, f – povrch z plastu, e – napěněné jádro
Výroba profilů (vpravo)
a - vytlačovací hlava, b – torpédo, c - kalibrace, d - tavenina s nadouvadlem, e – kompaktní povrch, f – napěněné jádro
6.4.
Stroje pro vytlačování
Pro vytlačování se používají stroje různé konstrukce, kdy se mění pracovní člen
v tavící komoře. Potom rozeznáváme stroje
pístové,
šnekové a
diskové. Požadavky na vytlačovací
stroj jsou následující: vysoký
vytlačovací výkon úměrný otáčkám šneku a co nejméně závislý na
protitlaku, rovnoměrná doprava taveniny bez pulzací, vytlačování
taveniny bez orientace, homogenní zamíchání polymeru se všemi
případnými aditivy bez těkavých podílů, místně a časově
rovnoměrná teplota taveniny, která je optimální z hlediska
výkonu stroje, zpracovávaného polymeru a kvality vytlačovaného
výrobku.
Vytlačovací stroje se také dělí na rychloběžné a
pomaloběžné. Zatímco u rychloběžných strojů v důsledku
vysokých otáček šneku (250 až 1500 min-1) stačí
vytápět pouze na začátku, neboť vzniklé teplo třením stačí
k roztavení materiálu, u pomaloběžných strojů musí být ohřev
tavící komory neustálý. Rychloběžné stroje mají krátké šneky
s délkou 10 až 17 D.
6.4.1. Šnekové vytlačovací stroje
Schéma uspořádání
vytlačovacího stroje je na obrázku. Ve vstupní části se musí
většinou granulovaný nebo aglomerovaný polymer zachytit,
předehřát a za odplynění stlačit. V kompresní části je polymer
dále stlačován, plastikován a homogenizován s případnými
přísadami. Ve výstupní části je již ve formě tepelně i
materiálově homogenní taveniny pod tlakem kontinuálně vytlačován
do „nástroje“ –
vytlačovací hlavy. Ke zpracování plastů se používají
především
jednošnekové vytlačovací stroje, ale pro různé aplikace se
konstruují i
dvoušnekové vytlačovací stroje,
stroje na kaučuky, apod.
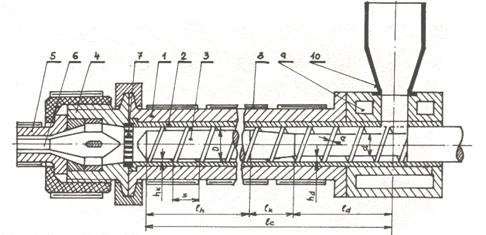
Jednošnekový vytlačovací stroj
1 – pracovní válec, 2 – pouzdro, tavící komora, 3 – šnek, 4 – vytlačovací hlava, 5 –
hubice, 6 – trn, 7 – lamač, 8 – topení, 9 – chlazení, 10 – násypka
Šnek je nejvýznamnějšífunkční částí vytlačovacího stroje. Teoreticky by každý plast
vyžadoval svůj speciální šnek, ale v praxi se používá několik
ověřených konstrukcí šneku, které buď výrobce vytlačovacího
stroje, nebo dodavatel polymeru pro jeho optimální zpracování
doporučí.
Velikost vytlačovacího stroje se určuje průměrem
šneku D a jeho účinnou délkou L,
která se obvykle vztahuje k průměru poměrem L / D.
Pro zpracování termoplastů se používají většinou šneky s poměrem
L / D = 20 a vyšším. Běžně jsou používány
jednochodé šneky s úhlem stoupání 17,7o, což odpovídá
stoupání závitu rovnému jednomu průměru. Šířka hřbetu závitu
bývá obvykle 0,1 D, vůle mezi hřbetem závitu a válcem 0,002 až
0,005 D. Dále jsou šneky pro zpracování polymerů
charakterizovány tzv. kompresním poměrem. Pro granuláty
termoplastů se pohybuje v rozmezí 1,8 až 4.
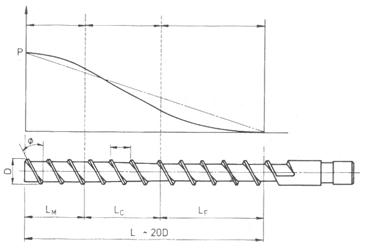
Průběh tlaku ve šnekovém vytlačovacím stroji
Doposud se nepodařilo zkonstruovat univerzální šnek pro všechny
termoplasty. Obvykle se upravuje vzájemný poměr tří částí šneku
tak, aby co nejlépe zpracovával daný polymer – tlakový profil
šneku. Na horním obrázku je ukázán průběh tlaku ve šnekovém
vytlačovacím stroji a na dolním obrázku průběh tlaku na šneku
s odplyňovací zónou. V odplyňovací části jsou z taveniny
odstraňovány těkavé podíly, voda, apod. Délka odplyňovacích
šneků je kolem 25 až 35 D.
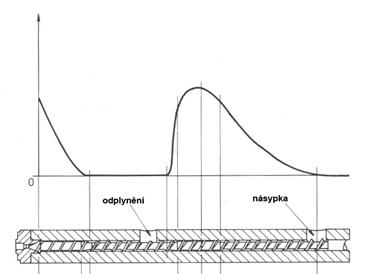
Průběh tlaku na stroji s odplyněním
6.4.2. Pístové vytlačovací stroje
Vytlačovací stroje
pístové mají jako hlavní funkční část píst. Pohon pístu bývá
hydraulický nebo mechanický. Pracovní část je tvořena válcem s
pístem a vytlačovací hlavou. Materiál pro vytlačování se vkládá
do pracovního válce. Velikost pístového vytlačovacího stroje je
určena maximální vytlačovací silou, průměrem pracovního válce a
zdvihem pracovního pístu. Pístové vytlačovací stroje se
nejčastěji používají k vytlačování materiálů citlivých na
teplotu, jako je např. PF nebo materiálů se špatnými tokovými
vlastnostmi, jako je např. PTFE. Vytlačovaný materiál není
namáhán vysokým smykovým zatížením a lze takto vyrábět profily v
poměrně úzkých výrobních tolerancích. Nevýhodou pístových
vytlačovacích strojů je jejich cyklický výrobní proces.
6.4.3. Diskové a spirálové vytlačovací stroje
Vytlačovací stroje
diskové jsou založeny na tzv. Weissenbergově efektu, který
je podmíněn visko-elastickými vlastnostmi zpracovávaného
materiálu. Výkon diskového vytlačovacího stroje závisí na
průměru a tvaru disku, smykové rychlosti a druhu zpracovávaného
polymeru. Konstrukčně jsou diskové vytlačovací stroje velmi
jednoduché. Disk vytváří proti čelní desce štěrbinu, do které
přes chlazenou násypku vstupuje materiál a účinkem elastických
napětí se dopravuje v radiálním směru k hubici. Potřebné teplo k
tavení vzniká v důsledku smykového namáhání materiálu ve
štěrbině a také je dodáváno topnými tělesy. Nevýhodou takto
řešeného diskového vytlačovacího stroje jsou nízké vytlačovací
tlaky, které lze v určitém rozsahu ovlivňovat změnou otáček
disku nebo nastavením velikosti štěrbiny. Výhodami diskových
vytlačovacích strojů je, že dosahují rychlé plastikace polymeru
při vysoké homogenitě taveniny, mohou zpracovávat práškové i
granulované materiály, tavenina se dá snadno odplynit a
plastikační proces lze snadno ovládat. Vytlačovací stroje
spirálové tvoří přechod mezi stroji diskovými a šnekovými.
Rozdíl spočívá v tom, že pohyb materiálu nastává v kanálku,
který má tvar spirály, vlivem účinku rychlostních složek a ne
účinkem visko-elastických vlastností plastu.
6.5. Konstrukce vytlačovacích hlav
Vytlačovací hlava je část stroje, ve které dopravovaný
materiál získává definitivní, ale nezafixovaný tvar. Hlava musí
mít takový profil, aby zaručovala pravidelný a trvalý tok
taveniny. Nesmí v ní existovat tzv. mrtvé prostory, ve kterých
by se materiál mohl zastavit a zůstat tak dlouho v kontaktu s
vyhřívaným tělem hlavy, až by degradoval. Zvláště nebezpečné
jsou mrtvé prostory při zpracovávání PVC. Mezi konec šneku a
vytlačovací hlavu se vkládá lamač, což je děrovaná deska
s otvory (3 až 8 mm) pro konečnou homogenizaci taveniny a jako
opěra pro čistící síta. Hlava bývá připojena k válci šnekového
vytlačovacího stroje několika způsoby. U menších strojů se někdy
šroubuje na konec válce, jinak se používá bajonetové nebo
objímkové uchycení nebo přírubové uchycení sklápěcími šrouby.
Podle konstrukčního uspořádání rozdělujeme
vytlačovací hlavy na hlavy přímé, nepřímé, širokoštěrbinové
a speciální. Rozdělení může být i podle druhu vyráběných
výrobků a polotovarů.
6.5.1. Přímé
vytlačovací hlavy
Hlavy přímé jsou především určené pro vytlačování uzavřených
symetrických profilů - jako jsou např.
trubky, hadice nebo uzavřených nesymetrických
profilů, jako je např.
okenní profil. Konstrukce
hlavy pro uzavřené profily by měla zabezpečit volný přívod
vzduchu do dutin profilu obzvlášť u navíjených profilů. Dále se
přímé hlavy používají k vytlačování otevřených profilů, jako je
např. okapový žlab, apod. Hlavy pro vytlačování profilů jsou
konstrukčně mnohem složitější. Hubice i trn jsou výrazně delší
kvůli relaxaci napětí v tavenině.
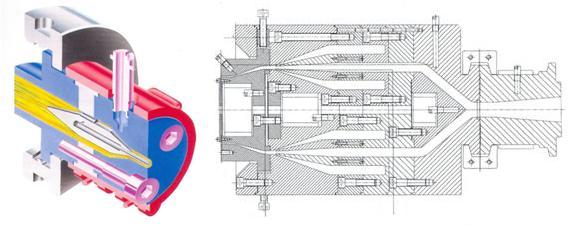
Přímé hlavy na trubky
vlevo - schéma, vpravo - hlava pro vícevrstvé trubky
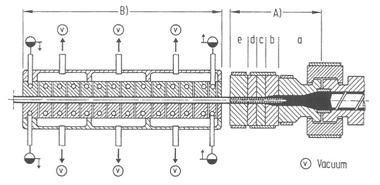
Přímá hlava na profily
A – nevytápěná část, B – vytápěná část, v - vakuum
Při konstrukci a návrhu hlavy se musí počítat s narůstáním
taveniny za hubici, smrštěním při chlazení a se změnou rozměrů
vlivem protažení. U tenkých stěn bývá hubice zvětšena o 5 až 10
%, u tlustých stěn bývá cca o 10 % zmenšena. Podle tvaru trubky
nebo profilu se mění hubice a trn. Hubicí lze posouvat v ose
trnu. Nevýhodou přímé hlavy jsou oblasti, ve kterých se spojují
proudy taveniny. Tuto nevýhodu odstraňuje
spirálový rozdělovač.
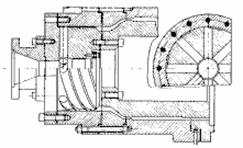
Schéma hlavy pro výrobu trubek se spirálovým rozdělovačem
6.5.2. Nepřímé
vytlačovací hlavy
Hlavy
nepřímé tj. hlavy příčné a šikmé se používají pro
oplášťování vodičů, kabelů nebo kovových profilů,
vyfukování fólií nebo
dutých předmětů. Hlavy pro oplášťování vodičů mají vrtaný
trn, kterým prochází vodič a tím se vyhýbáme vedení přes šnek.
Nepřímé hlavy mají různý úhel odklonu od osy šnekového
vytlačovacího stroje. U příčných hlav je tento úhel 90o,
u šikmých hlav je 30 až 60o. Čím větší je úhel
odklonu, tím větší jsou problémy s nerovnoměrností toku
taveniny.
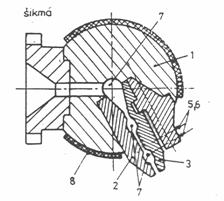
Šikmá plochá hlava
1 – těleso hlavy, 2 – spodní pevná čelist, 3 – horní stavitelná čelist, 5, 6 – stavěcí šrouby, 7 – příčné rozvodné kanály, 8 – topení
Technicky náročné jsou
hlavy pro vyfukování fólií. Vytlačovaná trubka musí mít
nejen naprostou rovnoměrnou tloušťku stěny, ale také stejnou
viskozitu a teplotu. Jsou možné dva způsoby konstrukce: hlava
s radiálním vtokem a hlava s axiálním vtokem. U radiálních hlav
je rovnoměrnost rozdělení taveniny zajišťována tvarem trnu,
který reguluje velikost mezery na straně šneku a na opačné
straně. U axiálních hlav se regulování tloušťky provádí
radiálním posuvem hubice. Stále častěji se používá spirálový
rozdělovač.
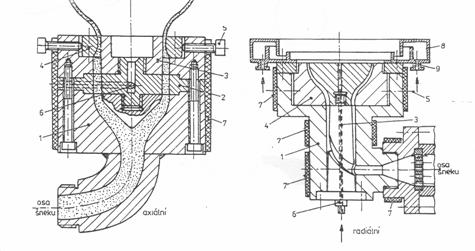
Radiální a axiální příčná hlava
1 – hlava, 2 – rozvod vzduchu, 3 – trn, 4 – hubice, prstenec, 5 – šrouby, 6 – přívod vzduchu, 7 – topení
6.5.3.
Širokoštěrbinové vytlačovací hlavy
Širokoštěrbinové hlavy rozvádějí materiál pomocí kanálů do
široké štěrbiny. Odpor toku a tedy množství hmoty na výstupu se
řídí stavěcími šrouby. Nejčastější tvar širokoštěrbinových hlav
je tvar „rybího ocasu“, který nemá mrtvé prostory, ale u kterého
je problematické nastavení při změně tokových vlastností plastu.
Proto se pro vytlačování
fólií používají hlavy s tvářecí lištou.
6.5.4. Speciální
vytlačovací hlavy
Mezi speciální vytlačovací hlavy patří hlavy pro ostatní aplikace, jako např.
granulační hlava, hlava pro výrobu vláken, hlava pro
vytlačování sítí,hlavy pro
vícevrstvé materiály, střižná hlava, hlavy pro kaučuky, apod.
Vytlačovací širokoštěrbinové hlavy pro výrobu vícevrstvých fólií a desek (A, B, C)
Širokoštěrbinová hlava s tvářecí lištou - pozice a (vpravo)
Hlava pro výrobu vláken (vlevo)
Hlava pro vytlačování sítí má proti sobě otáčející se trn i hubici, které
vytlačují struny a v místě setkání strun dochází ke spojení.
Střižná hlava má rotující pouze trn, což se projevuje tvorbou
tepla v tavenině plastu a regulací otáček je možné regulovat
ohřev taveniny. Tento typ hlavy se používá hlavně u kaučuků,
napěňovaných profilů, plněných materiálů, apod. Hlavy pro
vícevrstvé materiály se používají u společného vytlačování,
koextruze, kdy více vytlačovacích strojů je připojeno
k jedné hlavě. Konstrukce hlav pro kaučuky je obdobná
termoplastům, ale je nutné pamatovat na separační prostředky.
.: Jdi na začátek stránky :.
|