- Speciální způsoby vstřikování
5.1. GIT – vstřikování plastů s podporou plynu
5.2. WIT – vstřikování plastů s podporou vody
5.3. Vstřikování sendvičů
5.4. Vícekomponentní nebo vícebarevné vstřikování
5.5. Intervalové vstřikování
5.6. Mramorové vstřikování
5.7. Vstřikování vlákny plněných termoplastů
5.8. Vstřikování reaktoplastů
5.9. Vstřikování pryží, elastomerů
5.10. Vstřikování plastů s prášky
5.11. Reakční vstřikování
5.12. Vstřikování s dolisováním, kompresní vstřikování
5.13. Tandémové vstřikování
5.14. Vstřikování taveninou o vysokém tlaku
5.15. Vstřikování strukturních pěn
5.16. Střídavé, cyklické, vstřikování
5.17. Nízkotlaké vstřikování
5.18. Technologie zastříkávání, hybridní technologie
5. SPECIální způsoby vstřikování
Kromě klasické technologie vstřikování
plastů, která byla probrána v předchozí kapitole, existuje mnoho
dalších způsobů vstřikování, které se řadí mezi speciální
způsoby. Liší se např. v parametrech procesu, v konstrukci
nástroje, v kombinaci materiálů, apod.
5.1. GIT – vstřikování plastů s podporou plynu
První ze speciálních technologií je technologie vstřikování s plynem (GIT), u
které se jedná o ekvivalent vstřikování termoplastů, vyvinutý
v osmdesátých letech s možností vyrábět
díly s uzavřenými dutinami, které jsou vytvořeny „ničím“,
kdy se do určitých míst výstřiku za
účelem vytvoření dutiny přivádí plyn, většinou dusík, čímž se
vytvoří výlisek o zdánlivě velkém průřezu, přičemž odpadne
nutnost chladit velké množství roztavené plastické hmoty. Jako
plynu je použito vysoce čistého dusíku (čistota min. 99,8
%) s možností jeho stlačování v rozsahu 10 až 30 MPa.
Výhodou GIT (gas injection technology) je snížení
uzavíracích sil, snížení smrštění, zkrácení délky cyklu
(zkrácení doby chlazení vlivem zmenšení tloušťky stěny při
zachování chladící plochy nástroje), snížení hmotnosti výrobku,
nízká deformace ploch výrobků, vysoký stupeň tuhosti u dílů s
žebry a zachování požadovaných mechanických vlastností a
minimalizace deformací výstřiku, vzniku staženin a snížení
spotřeby plastů včetně zlepšení poměru hmotnost – tuhost při
zachování vysoké kvality povrchu.
Dochází k redukci hmotnosti až o 50 % a ke zkrácení doby cyklu
také až o 50 %. Je možné počítat s poklesem výrobních nákladů o
30 až 50 %. Technologie GIT se dá použít pro většinu plastů,
např. pro PE, PP, PS, ABS, PA, SAN, PPO, PC, PBT, PC/PBT, TPU,
TPE, ale i pro plněné termoplasty. Nevýhodou technologie GIT je
vyšší cena nástroje a stroje, problematické chlazení v místech
kanálů, řízení procesu.
Vlastní proces vstřikování je obdobný jako u klasické
technologie vstřikování, tedy zavření formy, vstřik, dotlak,
chlazení, otevření formy a vyhození výrobku. Tlak plynu zde však
přebírá funkci dotlaku, je však nutné pomocí konstrukce tvaru
(geometrická opatření) kontrolovat směr pohybu plynu.
Žebra a rozdílné tloušťky stěn
potom slouží k vedení plynu.
Z hlediska technologie jsou možné dvě techniky tvorby dutiny.
První je tzv.
krátký vstřik, dofukovací
způsob, kdy je dutina formy naplněna jen částečně (objem
taveniny je 50 až 90 %) a následně je tlakem plynu zcela
vytvarována dutina formy (viz. obr. 5.1). Největším problémem je
zde objem dávky taveniny plastu. Druhý způsob je tzv.
dlouhý vstřik, vyfukovací
způsob, při kterém se plyn vstřikuje do dutiny formy až
po té, co plast úplně vyplní tvarovou dutinu a tavenina je
vytlačována buď zpět před čelo šneku a nebo do pomocné dutiny. U
krátkého vstřiku klesá tloušťka stěny se vzdáleností dráhy
plynu, u dlouhého vstřiku je rovnoměrnější po délce kanálu.
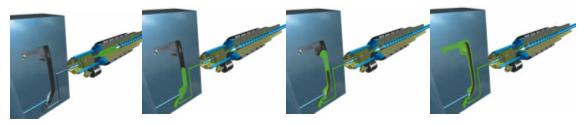
Postup vstřikování u GIT technologie – krátký vstřik
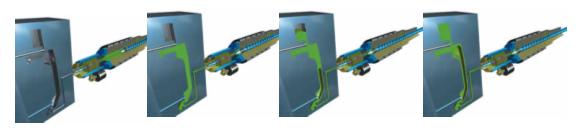
Postup vstřikování u GIT technologie – dlouhý vstřik
Při vstřikování s podporou plynu je nejdříve vstříknut plast (nejlépe
s pomocí horkých vtoků pro ideální homogenitu a teplotu
taveniny) a teprve potom plyn, protože při současném vstřikování
by se plyn dostal na povrch výstřiku. S ohledem na velký rozdíl
mezi viskozitou taveniny a plynu, vytváří se zcela jiný typ
proudění, než je klasické proudění taveniny plastu. Plyn musí
být přiveden do určeného místa výstřiku v přesně stanovený
okamžik, kdy plast ještě nestačil ztuhnout vlivem dotyku se
stěnou formy (důsledek chlazení) a nebo do míst, kde není
tavenina plastu v nečinnosti. To klade vysoké nároky na
konstrukci formy. Z počátku se přivádí plyn o nižším tlaku, aby
nedošlo ke vzniku povrchových vad (vytvoření dutiny). Po úplném
naplnění tvarové dutiny formy se tlak plynu zvýší, aby se
dosáhlo přesného dotvarování dílu. Kontrolu tlaku plynu provádí
tlaková jednotka, která je součástí vstřikovacího stroje, a může
být řízena jednak z hlediska kontroly objemu nebo tlaku.
V zásadě však platí, že pro tekutější hmoty je potřeba nižší
tlak a naopak.
Možnosti přívodu plynu za účelem vytvoření dutiny jsou
v podstatě dvě, tryskou nebo injektorem s průměrem
jehly 3 až 5 mm. U injektoru je nebezpečí ucpání jehly zbytky
tavenin termoplastů při zpětném odsávání plynu.
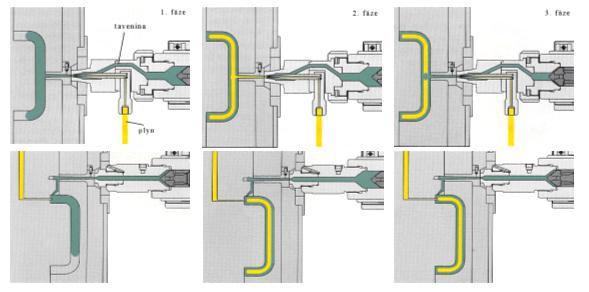
Varianty přívodu plynu (nahoře – tryskou, dole – jehlou, injektorem)
Důležitým parametrem u technologie GIT je doba prodlevy mezi vstřikováním
taveniny a přívodem plynu, protože s rostoucí dobou prodlevy
roste i tloušťka stěny výrobku vlivem chlazení. Stejné závěry
platí i pro teplotu taveniny a teplotu formy, které také
ovlivňují hmotnost výrobku a tloušťku stěny.
5.2. WIT – vstřikování plastů s podporou vody
Kromě technologie vstřikování plastů s podporou plynu (dusíku) se
v dnešní době začíná prosazovat technologie vstřikování, kdy
k výrobě
dutých těles se nepoužívá plyn, ale voda. Mluvíme o
technologii vstřikování s podporou vody – WIT (water
injection technology). Voda je vstřikována jednou nebo více
pumpami do tekuté taveniny za účelem vytvoření dutiny.
Vstřikování vody se provede tak, aby se voda
neodpařovala. Tedy teplota přivedené vody musí být volena
podle zpracovávaného plastu. Čelo vody pak působí na plastické
jádro jako vtlačovaný píst. Účinek je navíc podpořen tím, že
v oblasti (na čele) přechodu vody a taveniny ztuhne tenká
plastová membrána. Nakonec může být voda vytlačena z dílce
tlakovým vzduchem, nebo odsáta zpět a nebo se vylévá mimo formu
a přes zásobník se vrací zpátky do oběhu. Vstříknutí vody se
musí provést dostatečně rychle, aby se zabránilo hydrolytickému
rozkladu plastu.
Technologické principy vstřikování vody jsou obdobné jako u
vstřikování plynu.
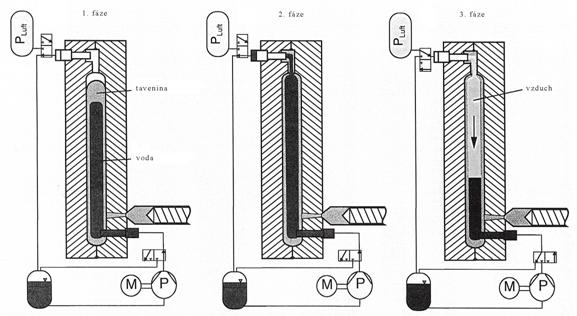
Princip WIT technologie – krátký vstřik
V důsledku
většího chladicího účinku vody oproti plynu se zkrátí
doba chlazení i doba celého cyklu zhruba na 10 až 20 % doby
u klasické technologie vstřikování. Výhody technologie WIT jsou
srovnatelné s výhodami technologie GIT a technologii WIT lze
použít i na výrobu dílců, které metodou GIT nelze realizovat.
Zároveň mají vnitřní stěny výrobků velmi hladký povrch. Na druhé
straně je technologie WIT použitelná jen u určitých tvarů
plastových dílů.
5.3. Vstřikování sendvičů
Vývojem a zavedením sendvičového
vstřikování bylo možno zpracovávat recyklované materiály
jako jádra vstřikovaných dílů. Sendvičové vstřikování dostalo
název podle struktury vyráběných
dílů - vnější stěny jsou z jednoho (prvního) materiálu a
představují „slupku“, zatímco vnitřek dílu se skládá z druhého
materiálu a představuje jádro. Tato struktura se vytváří
v důsledku procesů proudění, při kterých se využívá laminárního
proudění taveniny v dutině formy (technologie pomalého
laminárního toku). Povrchová vrstva materiálu po prvním vstřiku
se po ochlazení dotykem se stěnou formy již neposunuje a tím je
vlastně uzavřen materiál jádra do materiálu povrchu. Plasty jsou
však ještě dostatečně plastické na to, aby došlo ke spojení.
Povrchový materiál může být rozdílný od materiálu jádra, ale musí být
vzájemně mísitelný. Při sendvičovém vstřikování se používají
stroje se dvěma vstřikovacími jednotkami. Přitom technolog musí
mít rozsáhlé znalosti o vstřikovacím procesu, aby nastavil
vstřikovací proces tak, že se dosáhne stálého a postupného
plnění formy. Proces z hlediska jednotlivých kroků je shodný se
standardním vstřikováním.
Výsledný tvar komponentu (jádra a povrchu) závisí hlavně na
tokových vlastnostech materiálu, na geometrii výrobku a na
umístění vtokového systému.
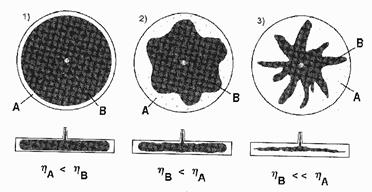
Vliv viskozity materiálu povrchu a jádra na rozdělení složek
Sendvičové díly jsou zásadně srovnatelné
se standardními výstřiky. Většina dnes realizovaných dílů
původně byla standardními díly. Změna sendvičové techniky na
standardní je zpětně bezproblémová, ale zpravidla z technických
nebo ekonomických důvodů není účelná.
Sendvičové produkty mohou být tenko i tlustostěnné. Tlustá
stěna však ještě neznamená větší podíl jádrové složky, např.
regenerátu. Technologií
vstřikování sendvičů se vyrábějí hlavně výrobky, u kterých je
možné použít recyklátu nebo vyztužit výrobek. Velký počet dnes
realizovaných aplikací je založen na kombinaci technických
vlastností rozdílných plastů, např. jádro obsahuje skleněná
vlákna a povrch je z kvalitního nevyztuženého plastu. Jiným
příkladem je elektricky vodivá povrchová slupka ve spojení
s levným standardním materiálem v jádru, apod.
Postup, který je rozdělen do dvou nebo tří kroků, je
následující: do vstřikovací formy je nejdříve vstříknuta hmota
(přesně definované množství), která tvoří kvalitní povrchovou
vrstvu výstřiku a vzápětí je do plastického jádra vstříknuta
hmota, tvořící jádro výrobku (dvoustupňový proces) resp. nakonec
hmota, která uzavře povrch plastového dílu (třístupňový proces).
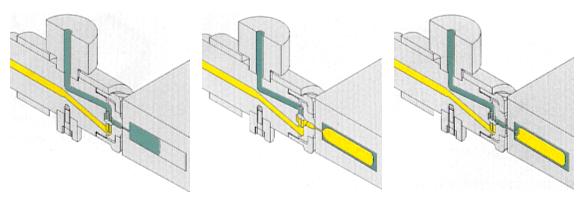
Princip sendvičového vstřikování – třístupňový proces
Vše je řízeno speciální
tryskou stroje, která spojuje dvě vstřikovací komory a
dávkuje taveninu plastu do dutiny formy pomocí nucených
(hydraulicky) nebo tlakově řízených mechanismů, které ovládají
jehlu trysky v závislosti na tlakových poměrech. Při výrobě
sendvičového dílu je vždy důležité nalézt správný okamžik, kdy
se přepíná složka, tvořící slupku, na složku, tvořící jádro.
Jiný technologický způsob je založen na tom, že se před zplastikovaný
materiál, který tvoří jádro sendviče, natlačí z pomocného
extruderu povrchový materiál přímo před šnek a klasickým
vstřikem dojde k vytvoření sendvičové struktury. Vždy se dávkuje
přesně definované množství.
Monosystém se dvěma plastikačními jednotkami
5.4. Vícekomponentní nebo vícebarevné
vstřikování
Technologie vícekomponentního nebo vícebarevného
vstřikování umožňují na jednom
výlisku kombinovat buď dva nebo více materiálů nebo dvě nebo
více barev od jednoho druhu plastu. Tato technologie se
rozvíjela postupně nejdříve od vstřikování více barev až po
dnešní vstřikování dvou nebo více
druhů polymerů, a to i nemísitelných. V případě nedostatečné
adheze se musí provést úprava geometrie dílu tak, aby došlo „k
zastříknutí“ spojovaných částí (závisí to na geometrii dílů). U
těchto technologií nepřejímá funkci dotlaku plyn, voda nebo
vnitřní materiál, ale dotlak je shodný s klasickou technologií
vstřikování. Technologie vícekomponentního vstřikování se liší
od klasického vstřikování pouze tím, že ke vstřikovací formě
jsou připojeny dvě (dvoukomponentní
vstřikování) nebo tři (tříkomponentní
vstřikování) resp. čtyři (čtyřkomponentní
vstřikování) vstřikovací jednotky.
Nejrozšířenější a zároveň nejjednodušší variantou je
dvoukomponentní vstřikování. V první fázi je nastříknut
první materiál (nebo barva), ve druhé fázi, po přemístění
výrobku do druhé pozice, se vstřikuje druhý materiál a dochází
ke spojení dílu.
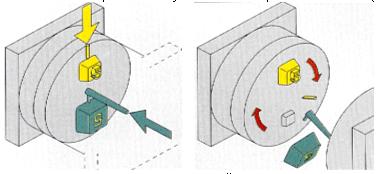
Princip dvoukomponentního vstřikování
Nejčastější uspořádání vstřikovacích jednotek je jedna horizontální a druhá vertikální.
Mohou být však uspořádány i paralelně.

Příklad uspořádání vstřikovacích jednotek pro dvoukomponentní vstřikování
Tříkomponentní nebo tříbarevné výlisky jsou zhotovovány ve
vícepolohových formách, přičemž úhel pootočení záleží pouze na
tom, kolik pracovních pozic má vstřikovací forma (dvoukomponentní
forma má dvě – pootočení o 180o, tříkomponentní má
dvě – pootočení o 180o nebo tři - pootočení o 120o
a čtyřkomponentní dvě - pootočení o 180o, tři -
pootočení o 120o nebo čtyři pozice - pootočení o 90o).
Tomu potom odpovídá i počet otevření vstřikovací formy během
celkového cyklu.
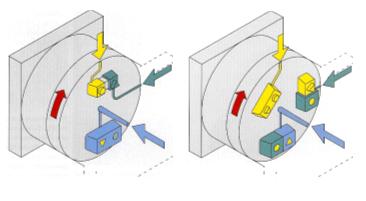
Princip tříkomponentního vstřikování
vlevo – dvoupolohová forma, vpravo – třípolohová forma
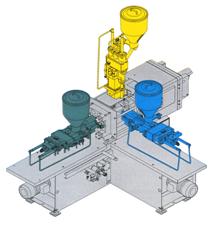
Ukázka rozmístění vstřikovacích jednotek u tříkomponentního vstřikování
Obdobně jako u tříkomponentního vstřikování lze i u
čtyřkomponentního vstřikování nejenom provést vlastní
sekvenci výroby, ale i uspořádání vstřikovacích jednotek. Tímto
způsobem lze vyrábět např. vrstvené plastové díly, zpracovávat
regranulát, vytvářet odolné vrstvy, apod.
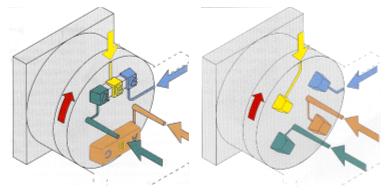
Princip čtyřkomponentního vstřikování
vlevo – dvoupolohová forma, vpravo – čtyřpolohová forma
Vstřikovací jednotky pro
všechny výše uvedené principy mají samostatně ovládáné nejenom
vytápění, ale i dávkování a technologické parametry. Umístění
vstřikovacích jednotek je konstrukčně odlišné podle druhu a
počtu komponentů. Nejrozšířenější je tzv.
„L“ pozice, ale vstřikovací jednotky mohou být i pod
rozdílnými úhly, než 90o.
Mezi nejdůležitější
činnosti u technologie vícebarevného nebo vícekomponentního
vstřikování patří překládání výlisků z jedné pozice do
další. Všechny procesy (vstřik, transport, vyhazování, atd.)
jsou zajišťovány automaticky během pracovního cyklu. Z hlediska
transportu (překládání) výlisků se mohou použít následující
způsoby:
V prvním
případě je část nástroje (tvárník nebo tvárnice) rotačně
pohyblivou částí vstřikovací formy, která se natáčí
k jednotlivým vstřikovacím jednotkám. Po prvním vstřiku a po
určité chladící době se forma otevře, je vyhozen vtok a
následuje pootočení formy spolu s výstřikem k další vstřikovací
jednotce. Tam je výstřik znovu uzavřen do nepohyblivé části
formy a je dostříknut do konečného tvaru. Rotační pohyby mohou
být buď alternující (při dvoupolohovém vstřikování) nebo spojité
u třípolohové technologie.
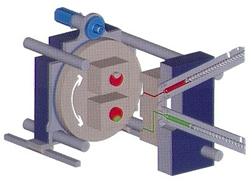
Princip překládání výrobků pomocí rotace formy
V druhém případě dochází k otočení stolu kolem vertikální osy k druhé polovině
vstřikovací formy. Vstřikovací jednotky vstřikují proti sobě a
odděluje je jen tloušťka otočné desky (tvárník nebo tvárnice).
Výhodou je snížení uzavíracích sil (kolem 30 až 50 %) zvláště u
shodných objemů prvního a druhého vstřiku, protože taveniny
působí tlakem proti sobě.
Ve
třetím případě je otočná pouze část pohyblivé poloviny
vstřikovací formy – indexová deska. Princip a ovládání jsou
shodné s rotačně otočnou částí vstřikovací formy.
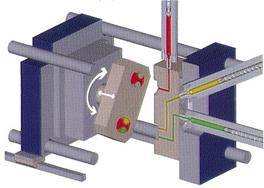
Princip horizontální rotace části vstřikovací formy
Ve čtvrtém případě, při použití posuvné části formy, se
použití šoupátka aplikuje hlavně u velkých výlisků při kombinaci
měkkého materiálu (gumy, termoplastického elastomeru) na tvrdý
plast (PP, PC, PA, …) např. při zhotovování těsnění. Šoupátko
uzavírá nebo otevírá tu část dutiny formy, která se má zaplnit
taveninou plastu. Technologie může být použita i pro větší počet
komponentů, ale s tím roste i konstrukční složitost formy. Musí
zde být brána v úvahu adheze jednotlivých složek. Nevýhodou je
někdy delší vstřikovací cyklus, protože se v určitých případech
jednotlivé komponenty vstřikují postupně a ne najednou, jako
tomu bylo u předchozích případů.
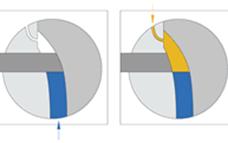
Princip použití posuvné části formy, šoupátka
Za páté, roboty se používají hlavně u větších výlisků nebo u
výlisků, u kterých nevadí delší čas pro přemístění a nebo při
použití dvou strojů. V současné době patří použití robotů mezi
nejrozšířenější způsoby transformace výlisků z jedné pozice do
druhé. Touto technologií se vyrábějí např. světla, ovládací
prvky na palubní desce a v okolí volantu, vícebarevné aplikace,
zpětná zrcátka (nemísitelné plasty, je zachován kloub), nářádí,
apod.
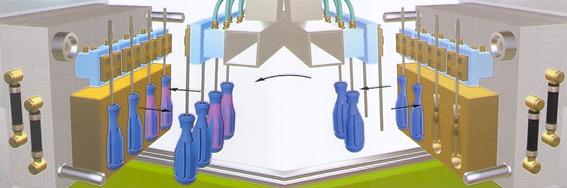
Princip použití robotů k překládání výlisků
5.5. Intervalové vstřikování
Zvláštním případem vícebarevného
vstřikování je
intervalové vstřikování, které je založeno na míchání
dvou
barevných odstínů ve speciální míchací trysce před vstřikem
do dutiny nástroje. Na rozdíl od dvoukomponentního vstřikování
zde nejsou jasné hranice mezi oběma odstíny, ale je docíleno
smíchání dvou barev podle předchozích návrhů. Vstřikovací
jednotky zde neústí přímo do vstřikovací formy, jako tomu bylo u
vícebarevného vstřikování, ale přímo do míchací trysky.
Vstřikovací jednotky jsou spárovány dohromady pomocí speciální
intervalové jednotky, uvnitř které je umístěna speciální míchací
tryska (stroje bez intervalové jednotky jsou potom používány pro
dvoubarevné vstřikování). Zbarvení (promíchání barev) je
ovlivněno nastaveným sekvenčním cyklem, tvarem vstřikovaného
dílu, umístěním vtokového systému a tokovými vlastnostmi vstřikovaného
materiálu.
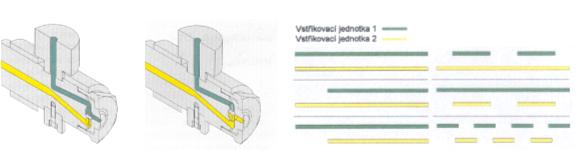
Princip intervalového vstřikování a příklad činnosti vstřikovacích jednotek během intervalového vstřikování
5.6. Mramorové vstřikování
Mramorování je výroba multikomponentních nebo
multibarevných výrobků nehomogenním mísením polymerů. Namísto
klasické šnekové plastikace je zde použit speciální hmětací
člen, který má částečně tvar pístu, částečně tvar šneku.
Plastikace je dosaženo postupným posouváním materiálu vpřed v
tavící komoře bez intenzívního promíchání. Kvůli nehomogenitě
jednotlivých tavenin se na výrobku objevují různě
intenzívní barevné oblasti. Nejčastěji se používá více barev od
jednoho druhu polymeru.
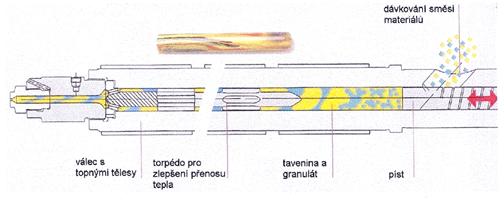
Konstrukce vstřikovací jednotky u mramorového vstřikování
5.7. Vstřikování vlákny plněných termoplastů
Termoplasty, plněné minerálními plnivy (krátkými nebo dlouhými
vlákny), mají díky netavitelnému podílu anorganického materiálu
v plastickém stavu větší vnitřní tření taveniny, než neplněné
plasty. Ke vstřikování jsou nezbytné teploty nejméně o 10 oC
vyšší. Rovněž tlaky, teplota formy a rychlost vstřikování jsou
doporučovány vyšší, neboť taveniny plněných termoplastů rychle
tuhnou a nedoporučuje se vyrábět díly s tloušťkou menší, než 2
mm. Délky šneků se doporučují v poměru 26 D.
V současné době se začínají
prosazovat plněné plasty dlouhými vlákny (10 až 12 mm), což
výrazně zvyšuje tuhost vyráběných dílů a s tím spojené i ostatní
výhody, které přinášejí dlouhá vlákna. Při zpracování (šnekování,
plastikaci) sice dochází k rozlámání granulí, ale i přes tento
nedostatek jsou výsledná vlákna mnohem delší, neži u materiálu
s krátkými vlákny (zhruba desetkrát). Plastikace se musí
provádět velmi šetrně speciálně provedeným šnekem, který se může
otáčet oběma směry.
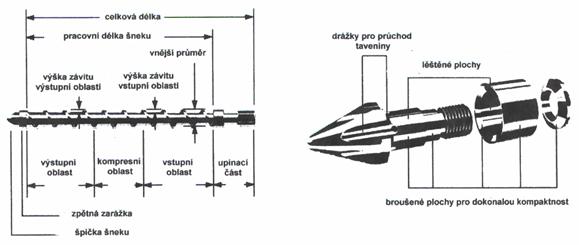
Konstrukce šneku pro plastikaci dlouhovláknových kompozitů
Výrobky, které byly získány touto technologií, mají zvýšenou
tuhost, vysokou rázovou houževnatost, výbornou rozměrovou
stabilitu a tyto vlastnosti si podržují i při extrémních
teplotách.
5.8. Vstřikování reaktoplastů
Kromě vstřikování termoplastů se mohou vstřikovat i
reaktoplasty. V současné době se zpracovává asi 30 %
reaktoplastů vstřikováním. Vstřikováním lze prakticky
zpracovávat veškeré druhy reaktoplastů. Oproti lisování
reaktoplastů má vstřikování tyto výhody: předehřev hmoty,
dávkování, plastikace a vstřikování se uskutečňuje v jedné
jednotce, proces lze automatizovat, použití mnohem kratších
vytvrzovacích časů, není zde technologický odpad.
Hlavní rozdíl mezi zpracováním termoplastů a reaktoplastů
spočívá jednak v rozdílné závislosti viskozity na teplotě a
jednak na tom, že místo doby chlazení je zde doba vytvrzování.
Forma se nechladí, ale je vyhřívána na vytvrzovací teplotu (dle
druhu reaktoplastu na 150 až 190 oC) a doba cyklu je
v podstatě dána dobou vytvrzování, kdy hmoty s lepší tekutostí
potřebují delší vytvrzovací časy. Kromě těchto rozdílů se liší
hlavně šnek, který má potlačenu kompresní část, aby nedošlo
k přílišnému smykovému namáhání a tím k předčasnému vytvrzení.
Reaktoplasty jsou plastikovány při relativně nízkých teplotách
(45 až 115 oC) a poměr
L / D šneku je v rozmezí 12:1 až 15:1.
Důležitou činností při zpracování je velmi dobré odvzdušnění
formy, neboť plyny, které vznikají při ohřevu reaktoplastů, se
musí odvést z tvarové dutiny nástroje. Kromě klasických
odvzdušňovacích kanálů a způsobů odvzdušnění se používá
způsob pootevírání formy po vstřiku, kdy během fáze
vstřikování je do dutiny formy vstříknut objem taveniny
80 až 95 % objemu dutiny, následuje redukce uzavírací síly
(otevření o 0,1 až 0,2 mm), odvzdušnění, opětovné uzavření a
doplnění objemu.
5.9. Vstřikování pryží, elastomerů Elastomery,
stejně jako termoplasty a reaktoplasty, mohou být vstřikovány do
forem. Jsou plastikovány, stejně jako reaktoplasty, také při
relativně nízkých teplotách a vstřikovány do elektricky
vyhřívaných forem. V důsledku dodaného tepla dochází
k vulkanizaci a k vytvoření zesíťované struktury. Kompresní
poměr šneku je kolem 1,5:1 a nebo s nulovou kompresní částí a poměr
L / D je obvykle 14:1.
5.10. Vstřikování plastů s prášky
Vstřikování plastů s prášky
- PIM (powder injection moulding) na bázi
kovů, skla nebo keramiky, apod. se používá k výrobě vysoce
přesných
dílů s výbornou kvalitou povrchu, kdy polymer se používá
pouze jako nosné pojivo - „lepidlo“ v prvních fázích
vstřikovacího procesu. Touto technologií se vyrábějí díly pro
automobilový a textilní průmysl, elektrotechniku, zdravotnictví,
apod.
Základním materiálem (plnivem) pro technologii vstřikování
plastů s prášky jsou tvrdé kovy, oceli, karbidy křemíku, oxidy
hliníku, porcelán, ale i měď, atd. Tyto prášky se musí smíchat
s plastem – pojivem, což je první fází výroby daného dílu, která
končí spékáním.
Jednotlivé
fáze procesu jsou následující: míchání prášku a pojiva,
granulace, vstřikování (výsledkem je tzv. zelený výrobek),
odstranění plastu (výsledkem je tzv. hnědý produkt), spékání a
korekce povrchu. V první fázi procesu se tedy musí smíchat a
zhomogenizovat potřebný prášek s plastem a následně se této
směsi musí předat tvar v míchací a granulační jednotce. Objem
plastu je v rozsahu 35 až 50 %. Tato směs je následně
zplastikována v tavící komoře vstřikovacího stroje a vstříknuta
pod vysokým tlakem a při vysoké teplotě do tvarové dutiny
vstřikovací formy. Po ochlazení je výrobek, zelený produkt,
vyjmut a přenesen do pece k vypálení polymeru. Vypálení polymeru
se provádí v pecích při teplotě zhruba 450 oC a
výsledkem je výrobek, hnědý produkt, s minimálním objemem
plastu. Následuje spékání kovového nebo keramického prášku
v pecích při teplotách (do 2000 oC), odpovídajících
použitému druhu prášku. Výsledné díly jsou homogenní a vykazují
izotropní smrštění, které je výrazně vyšší, než u klasické
technologie vstřikování.
5.11. Reakční vstřikování
Reakční vstřikování – RIM
(reaction injection moulding)
spočívá ve vstříknutí kapalné směsi (monomerní stádium) do
uzavřené dutiny formy, kde proběhne polymerace materiálu
(exotermická reakce a expanze) s vytvrzením složek.
Reakční vstřikování je výrazně odlišné od klasické
technologie vstřikování, protože reakční směsi (např. isokyanát
a polyol) jsou nízkoviskózní hmoty. Výhodou tohoto principu je:
-
nízká viskozita hmoty a z toho plynoucí možnost výroby
velkých dílů nízkými tlaky při nízkých investicích do
výroby (nízká cena forem),
- díly bez vnitřního pnutí, dodatečných deformací a propadlin i pro rozdílné tloušťky stěny,
- vlastnosti materiálu (mechanické vlastnosti, tečení, vytvrzovací doba) lze ovlivnit dle požadavků výroby,
- vstřik hmoty v monomerním stavu, čímž nedochází k deformaci polymerních řetězců a tedy k deformacím výrobků a k velkým smrštěním,
- vstřik hmoty do formy o vyšší teplotě, neži je teplota hmoty, v důsledku čehož nedochází ke zvyšování viskozity hmoty během procesu.
Rozdíly v technologických parametrech mezi technologií RIM a
klasickým vstřikováním
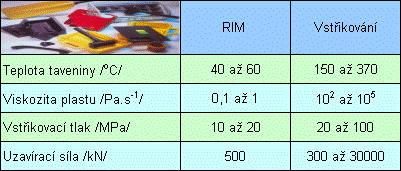
Hlavním materiálem, který se používá pro reakční vstřikování, je
polyuretan (PUR), ale např. i polyamid nebo různé směsi PUR,
protože jejich vysokoteplotní vlastnosti jsou lepší, než
vlastnosti samotného PUR. PA byl používán i v minulosti a
v současné době byly vyvinuty nové postupy zpracování PA. Rovněž
se dají použít složení na bázi epoxidů.
V technologii reakčního vstřikování jsou hmoty připravovány
odděleně a k jejich smíchání dojde před vstřikováním do vyhřáté
formy. Tlak vstřikování je velice malý (okolo 0,35 MPa), takže
uzavírací síly jsou mnohem menší a formy jsou obvykle mnohem
lehčí a levnější, než formy pro „klasické“ vstřikování. Polymer
je buď vytvrzen ve formě a nebo je částečně vytvrzován ve formě
a následně se vytvrzování dokončí na odděleném netlakovém
upínacím přípravku, zatímco pokračuje nový cyklus. Typický
cyklus je 50 % pro vytvrzování ve formě a 50 % pro vytvrzování
na vzduchu.
Kromě technologie RIM se používá i technologie reakčního
vstřikování s vyztužením (RRIM),
která se liší v tom, že jsou před vstřikováním na jedné straně
přívodu monomeru přidávány do hmoty tuhé vyztužující částice
(skleněná vlákna, minerální plniva, aj.), aby se zlepšila
pevnost a tuhost, zmenšilo se poměrné prodloužení nebo, aby se
vylepšila tepelná odolnost. Dalším zlepšením technologie RIM je
strukturní reakční vstřikování (SRIM),
kde je jako výztuhy použita obalová látka nebo preforma vložená
do formy.
Zařízení a formy pro technologii RIM jsou levnější, než
v případě vstřikování, protože se pracuje s nižšími tlaky.
Náklady na nástroje jsou nižší, protože se dají použít levné,
snadno tvarovatelné materiály, což tyto postupy činí přitažlivé
pro výrobu dílů v malých sériích.
Nástroje mají míchací jednotku
pro oba dva komponenty, plnící část a hlavně velmi dobré
odvzdušnění kvůli nízkým tlakům plnění.
Avšak nevýhodou těchto technologických postupů jsou někdy
poměrně dlouhé doby cyklů a obtíže při dosažení kvalitního
povrchu po aplikaci laků.
5.12. Vstřikování s dolisováním, kompresní vstřikování
Vstřikování s dolisováním
– CIM (compress injection moulding) je
technologie, u které je tavenina vstřikována do pootevřené
vstřikovací formy a následně je materiál dotvarován, dotlačen,
vyvozením programově řízené uzavírací síly. V první fázi proces
začíná otevřením formy do předem stanovené pozice. Ve druhé fázi
probíhá vlastní vstřikování a potom následuje po naplnění formy
stanoveným objemem dotlaková fáze, a to vyvozením plné uzavírací
síly. Uzavírací systém přejímá funkci dotlaku. Tato technologie
má poměrně dost alternativ a používá se např. k výrobě
CD nebo DVD. Technologie vstřikování s dolisováním umožňuje
dosahnout vysokých přesností rozměrů, nízkých hodnot smrštění,
deformací a vnitřních pnutí, protože tlak působí přímo na
materiál a to v celém objemu najednou.
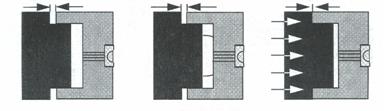
Princip technologie vstřikování s dolisováním
5.13. Tandémové vstřikování
Princip tandémového vstřikování spočívá v tom, že ve
vstřikovací formě jsou dvě protilehlé dutiny s výrobky,
které jsou v přesně stanovených
cyklech plněny, dotlačovány a chlazeny, stejně jako u
klasického vstřikování, ale pomocí samostatných vstřikovacích
jednotek. Princip je tedy založen na tom, že zatímco v jedné
dutině probíhá proces otevření, vyhození výrobku a zavření
formy, plnění a dotlaku, tak ve druhé dutině probíhá proces
chlazení Vstřikovat můžeme výrobky stejného objemu, ale i objemu
rozdílného.
5.14. Vstřikování taveninou o vysokém tlaku
Tento proces vstřikování je založený na vstřikování
taveniny, která je pod vysokým tlakem, do uzavřené dutiny
formy. V první fázi je tryska stroje, která je vybavena
pneumatickou jehlou, uzavřena a plastikační jednotka stroje
plastikuje materiál stejně, jako u konvenčního vstřikování. Ve
druhé fázi, po skončené plastikaci, je tavenina stlačována mezi
uzavřenou tryskou a čelem šneku pohybem šneku vpřed do dosažení
předem stanovené pozice. Kompresní tlak je v závislosti na
výrobku v rozsahu 100 až 250 MPa, nastává zmenšení objemu.
Tavenina je udržována pod vysokým tlakem i z hlediska dosažení
teplotní homogenity. Ve třetí fázi je tryska otevřena, tavenina
relaxuje a zvětšuje svůj objem, tedy dochází k plnění dutiny
formy. Působením dotlaku dochází k redukci smrštění.
5.15. Vstřikování strukturních pěn
Výrobky ze strukturních pěn mají kompaktní povrchovou
vrstvu a napěněné jádro. Plasty pro výrobu strukturních pěn jsou
nadouvány přídavkem 0,7 až 3 % chemického nadouvadla nebo
fyzikálně přídavkem uhlovodíků a výrobky jsou ve fázi plnění
dutiny formy asi o 10 % vypěněny. Plasty, používané pro
strukturní pěny, jsou ABS, PA, PEI, LDPE, HDPE, PPE, PPO, PC, PP,
PS, PBT. Objemem přidaného nadouvadla lze získat buď lehký nebo
těžký výstřik. Kromě toho se vylepšila tato technologie tak, že
dle nového způsobu se při použití vhodné konstrukce formy
vstřikuje tvrdá pěna do měkké pěny, čímž se dosáhne různého
složení na místech, kde je to potřeba.
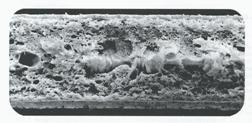
Řez stěnou napěněného dílu
Strukturní pěny lze zpracovávat na běžných vstřikovacích
strojích s dostatečnou vstřikovací rychlostí buď nízkotlakým
nebo vysokotlakým způsobem. Tlak plynu u nízkotlakého způsobu
je v rozmezí 2,1 až 3,4 MPa. Proces plnění je analogií krátkého
vstřiku (objem taveniny je v rozmezí 80 až 90 %) a plný objem
výrobku vzniká v důsledku expanze plynu. Oproti vstřikování
termoplastů jsou v tomto případě chladící doby mnohem delší
v důsledku špatného přenosu tepla. Kromě nízkotlakého procesu
s krátkým vstřikem existuje i vysokotlaký proces
s plným vstřikem. Tlak plynu je vyšší, než 3,4 MPa. Nevýhodou
jsou vzhledové vady na povrchu a poměrně dlouhý čas pro vytěkání
zbytku nadouvadla (24 až 48 hodin) před započetím doplňkových
operací.
Mezi velmi známé způsoby výroby strukturních pěn patří použití
fyzikálního nadouvadla, pentanu, v polystyrénu (PS) –
strukturní polystyrén. Hustota konečného výrobku je kolem 10
kg.m-3. Rozeznáváme dva způsoby výroby konečných
polotovarů nebo dílů: V prvním případě jsou kuličky PS ohřívány
horkou párou na teplotu 100 °C, při které dochází k jejich
předpěnění. Následuje plnění dutiny uzavřené formy, kde se
předpěněné kuličky dopění pod účinkem teploty kolem 120 °C.
Druhý způsob je založen na plném vypěnění v dutině nástroje.
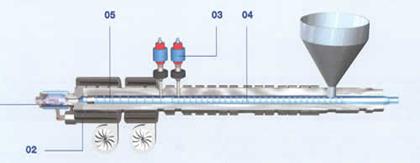
Detail a popis speciální plastikační jednotky pro technologii Mucell
01 – uzavřená tryska, 02 – topné jednotky s přídavným chladícím ventilátorem pro kontrolu teploty,
03 – přívod plynu jehlou, 04 – speciální šnek (L = 28 D), 05 – míchací zóna pro homogenizaci směsi plyn – polymer
Dalším speciálním procesem výroby strukturních pěn je použití
dusíku –
technologie „Mucell“, kterou je možné aplikovat pouze
se
speciálním vybavením. Výhodou tohoto systému je rovnoměrnost
rozložení a velikost jednotlivých dutin ve struktuře
strukturních pěn oproti klasické technologii výroby strukturních
materiálů.
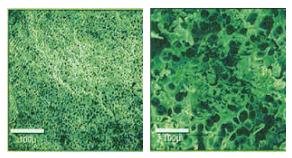
Porovnání struktury při použití dusíku (vlevo) a klasického nadouvadla (vpravo)
5.16. Střídavé, cyklické, vstřikování
Vysoké požadavky na kvalitu plastových dílů vedou k použití
střídavého vstřikování - MLFM (multi live feed
injection moulding), které se používá hlavně u materiálů
plněných vyztužujícím (ale i nevyztužujícím) plnivem, u blendů,
atd. Tato technologie snižuje počet vad na výrobku, zvyšuje
pevnost u vyztužených plastů, snižuje vnitřní pnutí a efekt
studených spojů.
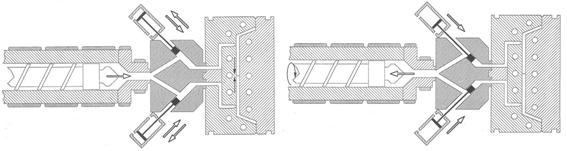
Proces střídavého, sekvenčního, vstřikování
vlevo – vstřikování, vpravo - dotlak
Technologie je založena na kontrolovaném smyku (tečení) taveniny
plastu v dutině vstřikovací formy během fáze plnění a dotlaku.
Jednoduše řečeno, dochází k promíchávání taveniny v dutině
vstřikovací formy během jednoho cyklu, když předtím došlo
k rozdělení taveniny plastů do dvou proudů. Vše je řízeno
programem v jednotlivých sekvencích. Pokud jeden píst vstřikuje,
druhý dotlačuje a naopak. V poslední fázi provádí dotlak oba
najednou.
5.17. Nízkotlaké vstřikování
Nízkotlaké vstřikování
je alternativou klasického vysokotlakého vstřikování. Nízký tlak
je jak na straně vstřiku, tak i na straně uzavírací jednotky.
Výhodou je snížení velikosti stroje, nízké napětí a vnitřní
pnutí ve výrobku, dostatečná velikost dílů, nízká cena nástroje.
S výhodou se používá
vícepolohových strojů s několika samostatnými nástroji,
které se otáčejí k jednotlivým pozicím. Každý nástroj má vlastní
uzavírací systém. Použití je vhodné pro delší vstřikovací
cykly.
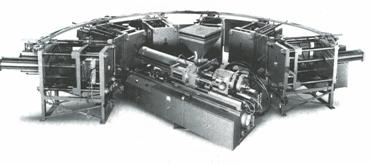
Vícepolohový vstřikovací stroj
5.18. Technologie zastříkávání, hybridní
technologie
Principem hybridních technologií (in-mould technolgy) je ta
skutečnost, že
tavenina plastu je nastříknuta na jiný materiál (kov,
textilie, aj.) a dojde ke spojení těchto dvou materiálů a ke
vzniku jednoho
výrobku s lepšími vlastnostmi. Zároveň dojde k úspoře
hmotnosti materiálu plastu, ke zlepšení korozní odolnosti,
vzhledu, apod. Technologie je
založena na vkládání různých materiálů ve formě polotovaru nebo
předtvarovaného dílu do dělící roviny vstřikovací formy pro
zlepšení vzhledových vlastností výrobku nebo pro výrobu dílů
s vysokou kvalitou povrchu.
Rozeznáváme několik technologických postupů vytváření povrchů:
.: Jdi na začátek stránky :.
|