- Vstřikování plastů
4.1. Popis a vliv jednotlivých časů vstřikovacího cyklu
4.1.1. Strojní časy
4.1.2. Doba vstřikování
4.1.3. Doba dotlaku
4.1.4. Doba plastikace
4.1.4. Doba chlazení
4.2. Faktory ovlivňující vlastnosti a kvalitu výstřiku
4.3. Vstřikovací stroje
4.3.1. Vstřikovací jednotka
4.3.2. Uzavírací jednotka
4.4. Vstřikovací formy
4.
Vstřikování plastů
Vstřikováním se vyrábějí
takové výrobky, které mají buď charakter
konečného výrobku a nebo jsou
polotovary nebo díly pro další zkompletování samostatného
celku. Výrobky zhotovené vstřikováním se vyznačují velmi dobrou
rozměrovou i tvarovou přesností a vysokou reprodukovatelností
mechanických a fyzikálních vlastností. Technologie vstřikování
je nejrozšířenější technologií na zpracování plastů, je to
proces diskontinuální,
cyklický. Vstřikováním lze zpracovávat téměř všechny druhy
termoplastů. V omezené míře se vstřikují i některé reaktoplasty
a kaučuky.
Vstřikování je způsob tváření plastů, při kterém je dávka zpracovávaného
materiálu z pomocné tlakové komory vstříknuta velkou rychlostí
do uzavřené
dutiny kovové formy, kde ztuhne ve finální výrobek. Tlaková
komora je součástí
vstřikovacího stroje a zásoba vstřikovaného materiálu se
v ní stále doplňuje během cyklu.
Výhody vstřikování jsou krátký čas cyklu, schopnost vyrábět
složité součásti s dobrými tolerancemi rozměrů a velmi dobrou
povrchovou úpravou, ale i konstrukční flexibilita, která
umožňuje odstranění konečných úprav povrchu a montážních
operací. Hlavní nevýhodou v porovnání s ostatními metodami
zpracování plastů jsou vysoké investiční náklady, dlouhé doby
nutné pro výrobu forem a potřeba používat strojní zařízení,
které je
neúměrně velké v porovnání s vyráběným dílem.
Postup vstřikování je následující: plast v podobě
granulí je nasypán do násypky, z níž je odebírán pracovní
částí vstřikovacího stroje (šnekem, pístem), která hmotu
dopravuje do
tavící komory, kde za současného účinku tření a topení plast
taje a vzniká tavenina. Tavenina je následně vstřikována do
dutiny formy, kterou zcela zaplní a zaujme její tvar. Následuje
tlaková fáze pro snížení smrštění a rozměrových změn. Plast
předává formě teplo a ochlazováním ztuhne ve finální výrobek.
Potom se forma otevře a výrobek je vyhozen a celý cyklus se
opakuje.
Vstřikovací cyklus tvoří
sled přesně specifikovaných úkonů. Jedná se o proces
neizotermický, během něhož plast prochází teplotním
cyklem. Při popisu vstřikovacího cyklu je nutno jednoznačně
definovat jeho počátek. Za počátek cyklu lze považovat okamžik
odpovídající impulsu k uzavření formy.
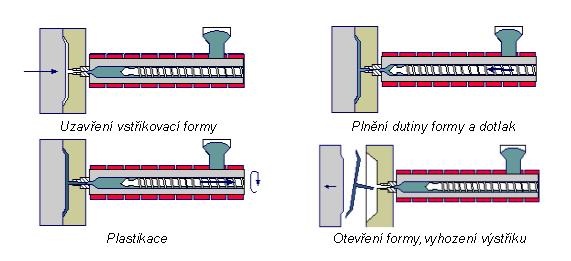
Vstřikovací cyklus
Vstřikovací cyklus však můžeme posuzovat i z hlediska
zpracovávaného plastu a s výhodou jej vyjádřit jako závislost
tlaku v dutině formy na čase. Tento tlak se nazývá vnitřní
tlak a značí se
pi.
Kromě vnitřního tlaku existuje i vnější tlak, označovaný
p, kterým se myslí tlak vztažený na jednotku
plochy průřezu šneku.
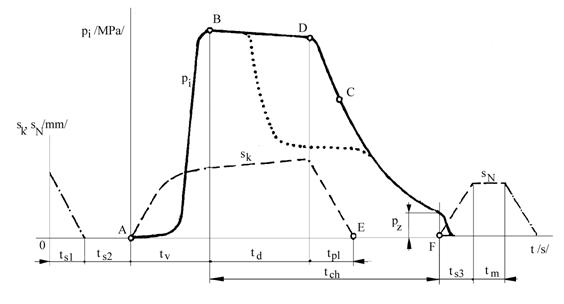
Průběh vnitřního tlaku pi v dutině formy během procesu
vstřikování
sk – pohyb šneku, sn – pohyb nástroje
Na počátku vstřikovacího cyklu je
dutina formy prázdná a forma je otevřená. V nulovém čase
dostane stroj impuls k zahájení
vstřikovacího cyklu, pohyblivá část formy se přisune
k pevné, forma se zavře a uzamkne
– strojní
časy. Tyto činnosti je nutné
odlišit, protože na přisouvání formy se musí vynaložit jen malá
přisouvací síla Fp,
zatímco na uzamknutí je nutno vynaložit značně vyšší uzavírací sílu
Fu
(až třikrát vyšší), neboť musí být zaručeno, že se forma vlivem
tlaku taveniny při vstřikování neotevře. Následuje pohyb šneku
v tavicí komoře a začíná vlastní
vstřikování roztavené hmoty do dutiny vstřikovací formy.
V této fázi
šnek vykonává pouze axiální pohyb, neotáčí se a vlastně plní
funkci pístu. Po naplnění formy je tavenina v dutině ještě
stlačena a tlak dosáhne maximální hodnoty.
Jakmile tavenina vstoupí do dutiny formy, ihned začne předávat teplo vstřikovací formě a
chladne.
Chlazení trvá až do otevření formy a vyjmutí výstřiku.
V praxi se dělí na dobu chlazení při plném vstřikovacím tlaku a
na dobu chlazení při klesajícím tlaku. Doba chlazení je závislá
na teplotě formy
TF
a tloušťce stěny výrobku. Během chladnutí se hmota
smršťuje a zmenšuje svůj objem, a aby se na výstřiku
netvořily
propadliny a staženiny, je nutno zmenšování objemu
kompenzovat dodatečným dotlačením taveniny do dutiny formy
– dotlak.
Dotlak může být po celou dobu stejně vysoký jako maximální tlak
nebo se může po několika sekundách snížit a další chladnutí
probíhá při sníženém tlaku. Dotlak se proto rozděluje na
izobarický a izochorický. Abychom mohli dotlačovat, musí před
čelem šneku zůstat určitý objem plastu -
polštář, na který bude šnek působit svým čelem. Tento
objem nesmí být moc velký (obvykle kolem 10 až 15 %, méně než
jednonásobek průměru šneku D), aby nedocházelo
k tepelné degradaci hmoty.
Po dotlaku začíná
plastikace nové dávky plastu. Šnek se začne otáčet, pod
násypkou nabírá granulovanou hmotu, plastikuje ji a vtlačuje do
prostoru před čelem šneku. Současně ustupuje dozadu, přičemž
musí překonávat tzv. protitlak neboli zpětný tlak. Výška
protitlaku ovlivňuje dobu plastikace a tím i kvalitu prohnětení
roztaveného plastu. Příliš vysoký protitlak by však mohl
způsobit až degradaci plastu. Ohřev plastu během plastikace se
děje jednak převodem tepla ze stěn válce, jednak frikčním
teplem, které vzniká třením plastu o stěny komory a o povrch
šneku a dále přeměnou hnětací práce šneku v teplo. Jestliže je
tavicí komora opatřena samouzavíratelnou tryskou, může
plastikace probíhat i při otevřené formě. Dále může a nebo
nemusí následovat odsunutí tavicí komory od formy. Během
pokračujícího chlazení tlak ve formě dále klesá až na hodnotu
zbytkového tlaku
pz,
což je tlak, pod nímž se hmota nachází ve formě těsně před jejím
otevřením. Příliš vysoký zbytkový tlak je příčinou vysokých
vnitřních pnutí ve výstřicích, které u křehkých hmot mohou
způsobovat až samovolné praskání výstřiku. Zbytkový tlak lze
snížit buď zkrácením doby dotlaku anebo
programovaným průběhem tlaku během dotlaku. Po dokonalém
zchladnutí výstřiku se forma otevře a výstřik se vyhodí z formy.
4.1.
Popis a vliv jednotlivých časů vstřikovacího cyklu
Jednotlivé úseky vstřikovacího cyklu trvají různě dlouho a jsou mimo jiné
ovlivněny např. geometrií výstřiku a technologickými podmínkami
vstřikování.
4.1.1. Strojní
doby
Strojní doby
na zavření formy ts1 a na otevření
formy ts3 závisí na rychlosti
pohybující se formy a na dráze, kterou musí forma urazit. Dráha
otevření formy je dána rozměrem výstřiku ve směru otevírání
formy a musí být tak velká, aby bylo možno výrobek z
formy
vyjmout, případně aby bylo dost prostoru pro činnost
manipulátoru ve formě. Je snaha zkrátit strojní časy na
minimum. Toho se dá dosáhnout zvýšením rychlosti pohybující se
formy. U moderních strojů není tato rychlost po celé dráze
stejná, nýbrž při zavírání se forma z počátku pohybuje velkou
rychlostí, avšak těsně před dosednutím formy se rychlost sníží,
aby obě části formy na sebe dosedly měkce a forma se nárazem
nepoškodila. Podobně i při otevírání formy je nejprve její
rychlost vysoká a před dojezdem formy na doraz se rychlost
sníží, aby vyhození výrobku z formy probíhalo pomalu. Celková
doba strojních časů ts1, ts2,
ts3 nepřesahuje u strojů střední
velikosti několik málo sekund. Kromě strojních časů, jež jsou
součástí vstřikovacího cyklu, jsou další strojní doby překryty
dobou chlazení.
4.1.2. Doba
vstřikování
Doba
plnění dutiny formy
tv se odvíjí od rychlosti vstřikování, tj. od
rychlosti pohybu šneku vpřed, která závisí na technologických
podmínkách, zejména na
teplotě taveniny Ttav a na
vstřikovacím tlaku p. Vliv však má i
teplota formy, objem výstřiku a jeho geometrický tvar, dále
řešení vtokové soustavy a
druh plastu. Je však nutné si uvědomit, že k určité hodnotě
vstřikovací rychlosti patří určitá hodnota vstřikovacího tlaku,
nebo-li nelze nastavovat velkou vstřikovací rychlost při nízkém
tlaku. U složitých výrobků a u výrobků s vysokými požadavky na
kvalitu povrchu a přesnost výroby je možné programovat průběh
rychlosti vstřikování. Vysoká vstřikovací rychlost má příznivý
vliv na orientaci makromolekul, ale je zde i nebezpečí přehřátí
a degradace materiálu.
Doba plnění se pohybuje od zlomku sekundy do několika málo
sekund u výstřiků s velkou hmotností. Doba plnění má být co
nejkratší, protože vstřikovaná tavenina se stykem s chlazenou
formou ochlazuje a ztrácí tekutost, takže při dlouhé době by
nezaplnila celou dutinu a vznikl by
nedostříknutý zmetek.
Proces plnění se musí řídit tak, aby tavenina nevtékala do formy
volným tokem, ale aby materiál vtékal do formy postupně. Při
postupném plnění, laminárním toku, se jedná o složitý
mechanismus tuhnutí vrstev taveniny. Teplota formy je mnohem
nižší, než teplota taveniny (zhruba 3 až 4krát) a tak tavenina
při styku se stěnou formy okamžitě ztuhne a vytvoří vrstvu
nepohyblivé hmoty
a zároveň i vrstvu tepelné izolace.
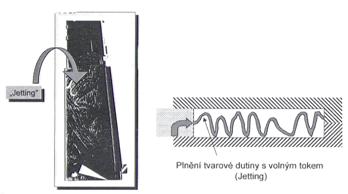
Plnění volným tokem
Uvnitř je potom plastické jádro s nízkou
viskozitou, umožňující další průtok taveniny plastu do dutiny
formy, která se potom roztéká směrem ke stěnám až dojde
k zaplnění tvarové dutiny formy. Vzhledem ke zvyšování viskozity
směrem ke stěně formy dochází k rostoucí rychlosti v plastickém
jádru a k zakřivení čela. Pokles tlaku je potom směrem ke stěně
formy.
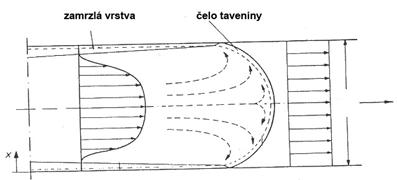
Laminární tok taveniny plastů
4.1.3. Doba dotlaku
Po naplnění tvarové dutiny
formy následuje stlačování hmoty, kdy tlak prudce stoupne
a rychlost náhle klesne. Pokud by tlak zůstal na původní
hodnotě, došlo by ke vzniku tlakové špičky, ke zvětšení
hmotnosti a rozměrů výstřiku a k vysokému namáhání formy, které
by mohlo vést k pružnému prohnutí formy, tzv.
dýchnutí. Aby se zamezilo těmto jevům je nutné v určité
době snížit vstřikovací tlak, tzn. přepnout na dotlak. Je-li
přepnutí opožděné stoupne tlak příliš vysoko a dojde k výše
popsaným jevům. Při předčasném přepnutí dochází k opačným jevům
a je zde až možnost
nedostříknutého výrobku. K přepnutí na dotlak může dojít buď
podle dráhy šneku, nebo podle vstřikovacího času, nebo podle
tlaku ve formě a nebo podle tlaku v hydraulice.
Doba dotlaku td
závisí hlavně na průřezu vtokového kanálu a zpravidla činí
několik sekund až desítky sekund. Účelem je dodávání materiálu
do formy a tím tedy kompenzování
smrštění během chladnutí, aby nevznikly propadliny a
staženiny. U strojů s optimalizací procesu lze průběh dotlaku
optimalizovat. V první fázi je dotlak vyšší, aby se využilo
vysoké tekutosti taveniny a ke konci se dotlak sníží, aby se
omezila orientace v okolí vtoku.
4.1.4. Doba
plastikace
Doba plastikace tpl
je čas, který je potřebný k tomu, aby došlo k zplastikování dávky plastu a
k jejímu rovnoměrnému zhomogenizování a umístění dávky před čelo
šneku, tzv. polštáře. Velikost zplastikované dávky musí
zabezpečit naplnění tvarové dutiny formy a vtokového systému,
ale i kompenzovat změnu objemu, vyvolanou smrštěním. Je však
nutné si uvědomit, že se posuvem šneku vzad snižuje účinná délka
šneku, a proto musí být zpětný tlak zvyšován.
Teplo, potřebné k roztavení jedné dávky, je asi z jedné třetiny
dodáváno z elektrického odporového topení a asi ze dvou třetin
z tření hmoty při hnětení.
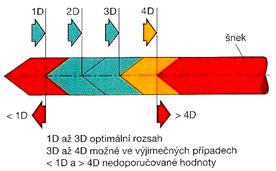
Možné dávkovací dráhy u vstřikovacích strojů
4.1.4. Doba
chlazení
Doba chlazenítch
představuje největší část cyklu a pohybuje se od několika sekund
u tenkostěnných výstřiků do několika málo minut. Závisí na
určující
tloušťce stěny výstřiku, na druhu plastu,
teplotě taveniny,
teplotě formy a na teplotě výstřiku v okamžiku vyjímání
z formy. Je snaha ji zkrátit na minimum účinným chlazením formy,
zejména těch míst, v nichž hmota chladne nejpomaleji.
Chladnutí začíná již během fáze vstřikování a pokračuje
během dotlaku a dochází ke značným změnám stavových veličin,
tlaku, měrného objemu a teploty. Fáze chladnutí ovlivňuje
nejenom strukturu, tj. orientaci, krystalizaci a vnitřní pnutí,
ale také kvalitu povrchu, zejména lesk.
4.2. Faktory ovlivňující vlastnosti a kvalitu výstřiku
O mechanických a
fyzikálních vlastnostech výstřiku, a o jeho kvalitě rozhoduje
druh plastu,
technologické parametry,
konstrukce formy a volba
stroje. Jednotlivé parametry nepůsobí samostatně, ale vždy
se ovlivňují navzájem. Z hlediska volby druhu plastu má
na vlastnosti výstřiku vliv:
- rychlost plastikace polymeru, která by měla být co nejkratší,
- tekutost
(reologické vlastnosti) plastu, která má být dostatečná
a nesmí se měnit s teplotou příliš rychle a která je
ovlivňována technologickými parametry,
- dostatečná tepelná stabilita plastu v rozsahu zpracovatelských teplot, která by měla být co nejširší,
- uvolňování těkavých látek,
- velikost vnitřního pnutí, které má být co nejnižší,
-
smrštění plastu (změna rozměrů výrobku oproti rozměrům
tvarové dutiny formy) v jednotlivých směrech na výrobku,
které je ovlivněno technologickými podmínkami.
Z technologických
parametrů, které se mezi sebou výrazně ovlivňují, má na
vlastnosti výstřiku a jednotlivé fáze vstřikování největší vliv:
-
vstřikovací tlak (ovlivňuje rychlost plnění, uzavírací sílu,
vnitřní pnutí, smrštění, orientaci – tj. narovnávání
makromolekul do směru toku, atd.),
-
teplota taveniny (konkrétní teplota závisí na druhu plastu a
ovlivňuje tekutost plastu, vstřikovací tlak, dobu chlazení a
tedy dobu cyklu, smrštění, tlakové ztráty, dotlak, atd.)
-
teplota formy (konkrétní teplota závisí na druhu plastu a na
charakteru výrobku, ovlivňuje tekutost plastu, rychlost plnění,
dobu chlazení, lesk výrobku, povrch výrobku, teplotu taveniny,
dotlak, vnitřní pnutí, smrštění, atd. – z technologického
hlediska má být co nejvyšší, hlavně u semikrystalických plastů),
-
rychlost
plnění dutiny formy má být co nejvyšší, je však nutné
kontrolovat teplotu taveniny, aby nedošlo k degradaci hmoty,
nevýhodou je i vysoká orientace makromolekul,
- výše a doba trvání dotlaku (ovlivňuje hlavně rozměry výrobku, smrštění a vnitřní pnutí).
4.3. Vstřikovací stroje
Vstřikovací proces probíhá na moderních strojích většinou plně
automaticky, takže se dosahuje vysoké produktivity práce.
Pořizovací cena strojního zařízení i vstřikovací formy je však
značně vysoká. Technologie je proto vhodná pro velkosériovou a
hromadnou výrobu.
Vstřikovací stroj se skládá ze
vstřikovací jednotky,
uzavírací jednotky a z řízení
a regulace.
Schéma vstřikovacího stroje se šnekovou plastikací na obrázku.
Každý výrobce vstřikovacích strojů je schopen vybavit
vstřikovací stroj tak, aby plnil funkci částečně nebo plně
automatizovaného pracoviště, tj. dovybavit stroj
manipulátory,
roboty,
temperačním zařízením,
dávkovacím a
mísícím zařízením,
sušárnami,
dopravníky pro výrobky a vtoky,
mlýny, atd.
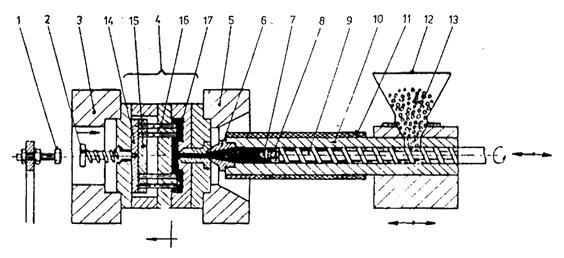
Schéma vstřikovacího stroje se šnekovou plastikací
(1 – doraz, 2 – tyč vyhazovače, 3, 5 – upínací desky, 4 – forma, 6 – vstřikovací tryska, 7 – špice šneku, 8 – zpětný uzávěr,
9 – šnek, 10 – tavící komora, 11 – topná tělesa, 12 – násypka, 13 – granule plastu, 14 – deska vyhazovačů,
15 – kotevní deska, 16 – vyhazovače, 17 – výstřik)
4.3.1.
Vstřikovací jednotka
Vstřikovací jednotka
plní dva hlavní úkoly: přeměňuje granulát plastu na homogenní
taveninu o dané viskozitě, vstřikuje taveninu vysokou rychlostí
a velkým tlakem do dutiny formy.
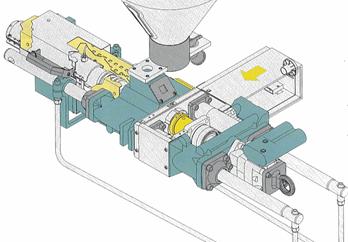
Schéma vstřikovací jednotky
První vstřikovací jednotky, které byly použity pro vstřikování plastů
již na konci minulého století, byly jednotky
pístové. Jejich princip byl převzat z lití roztavených
kovů pod tlakem. Udržely se až do poloviny 20. století, kdy byly
postupně zcela vytlačeny jednotkami
šnekovými. Dnes se používají jen výjimečně, a protože
význam pístových vstřikovacích jednotek je v současnosti
zanedbatelný, bude se další text týkat hlavně vstřikovacích
jednotek se šnekem. Rozdíl obou typů strojů je dán konstrukcí
tavicí komory. Jejím úkolem je převést do plastického stavu v co
nejkratší době co největší množství hmoty a zajistit maximální
teplotní homogenitu taveniny. Pohyb plastu v komoře je u
pístových strojů zajišťován pístem, u šnekových šnekem.
Konstrukcí šnekových vstřikovacích strojů byly s úspěchem
vyřešeny všechny hlavní nedostatky pístových strojů.
Mezi největší přednosti šnekových strojů patří:
- spolehlivá plastikace a dobrá homogenizace roztaveného plastu,
- zabránění přehřívání materiálu v tavicí komoře,
- vysoký plastikační výkon i velký zdvihový objem, takže velikost výstřiku lze teoreticky libovolně zvyšovat,
- odstranění potíží při čištění komory při výměně materiálu,
- zaručené přesné dávkování hmoty,
- nízké ztráty tlaku během pohybu hmoty,
- vyšší účinnost zásahu do vstřikovacího procesu, např. řízením dotlaku.
Činnost šnekového stroje je následující: Při plastikaci se
šnek otáčí a v hrdle
násypky nabírá granulovaný plast, který stlačuje a dopravuje
jej do vytápěných částí tavicí komory, kde materiál taje a jako
tavenina se hromadí před
čelem šneku a šnek během otáčení ustupuje dozadu. Po
zplastikování potřebného množství plastu se otáčivý pohyb šneku
zastaví a šnek se bez otáčení pohybuje dopředu jako píst a
vstřikuje taveninu do dutiny formy. Jelikož plastikace nové
dávky plastu může probíhat ještě ve fázi chlazení výstřiku ve
formě, je výrobní cyklus kratší oproti pístovým strojům.
K dalším přednostem patří jednoduché dávkování, možnost hmotu
dodatečně barvit a plnit plnivy nebo přidávat další přísady až
při zpracování
Vstřikovací jednotka se šnekovou plastikací je
charakterizována těmito parametry: průměrem D /mm/
a délkou L /mm/ šneku, vstřikovací kapacitou
Qv /cm3/, plastikační kapacitou
Qp /kg.h-1/, max.
vstřikovacím tlakem pvstř /MPa/,
objemovou vstřikovací rychlostí v /cm3.s-1/
a tím, zda je stroj vybaven universálním a nebo speciálním
šnekem. Vstřikovací kapacita Qv
představuje maximální objem taveniny /cm3/, kterou
lze na daném stroji vystříknout z tavicí komory do volného
prostoru při jednom pracovním zdvihu šneku nebo pístu. Je to
vlastně objem zásobního prostoru v komoře po odsunutí šneku do
jeho zadní krajní polohy. Plastikační kapacita stroje
Qp /kg.h-1/ udává maximální množství
taveniny v kilogramech, kterou je stroj schopen za jednu hodinu
přivést do plastického stavu. Představuje to množství hmoty,
které bylo zahřáté na teplotu vstřikování a bylo u ní dosaženo
požadované teplotní homogenity.
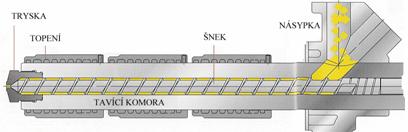
Řez vstřikovací jednotkou (kompresní poměr 1)
Nejdůležitější částí vstřikovací jednotky je tavicí komora,
šnek, tryska a topení včetně dalšího
příslušenství.
Konstrukce
šneku je přizpůsobena činnostem, který šnek musí
vykonávat, tj. dávkování a doprava materiálu, plastikace,
hnětení a vstříknutí do formy. Vývojem vstřikování se dospělo od
obyčejného šneku k diferenciálnímu šneku, pro
který je typický kompresní poměr, který je definován jako
poměr objemu šnekového profilu pro jedno stoupání závitu pod
násypkou k objemu profilu v části šneku před tryskou. Kompresní
poměr bývá v rozmezí od 1,5 do 4,5. Kompresního poměru lze
dosáhnout buď změnou úhlu stoupání závitu, což se však vzhledem
k obtížnější výrobě používá málo, nebo změnou průměru jádra
šneku, tedy změnou hloubky drážky, zatímco úhel stoupání je
konstantní.
Na
šneku je možno rozlišit tři funkční pásma. Pod násypkou je
šnekový kanál (nazývaný také drážka šneku) nejhlubší a průměr
jádra šneku nejmenší. Hloubka je konstantní. Toto pásmo se
nazývá vstupní nebo také dopravní, někdy i
dávkovací. Zpracovávaný materiál je v něm hlavně stlačován, čímž
se vytěsňuje vzduch z prostoru mezi granulemi, a ohříván a
teprve na konci této části může začít i tát. Ve druhém,
prostředním pásmu, se průměr jádra šneku směrem k trysce
zvětšuje a hloubka šnekového kanálu se zmenšuje.
Důsledkem toho dochází ke značnému stlačování materiálu, a proto se této
části říká pásmo kompresní nebo přechodové. V ní
dochází k nejintenzivnějšímu tání granulátu. Vzniklá tavenina je
však zatím teplotně nehomogenní. Homogenizace je úkolem
posledního pásma šneku u trysky. Toto pásmo se proto jmenuje
hnětací neboli homogenizační anebo výstupní.
Hloubka šnekového kanálu je po celé délce výstupního pásma opět
konstantní, ale je menší, než-li ve vstupním pásmu.
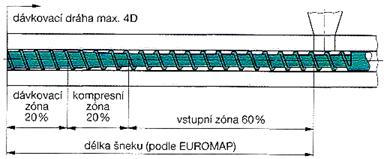
Diferenciální šnek
Důležitou částí šneku je jeho zakončení,
neboť tavenina má při vstřikování snahu téci šnekovým kanálem
zpět směrem k násypce. Tato tendence je tím větší, čím má hmota
vyšší tekutost. Proto se
zakončení šneku konstruuje tak, aby se tomuto jevu
zabránilo. Existují různá řešení, jako je tupé zakončení šneku
nebo prodloužené zakončení špičky šneku, ale nejspolehlivější je
zakončení se zpětným uzávěrem (ventilem).
Délka šneku se však nevyjadřuje v jednotkách délky, ale jako poměr délky
šneku a jeho průměru, tedy L / D. Délka šneku u
vstřikovacích strojů na termoplasty bývá obvykle 15 až 20 D.
Šneky, ať už obyčejné nebo diferenciální, mohou existovat
v různém provedení. Nejpoužívanější jsou šneky s normálně
dlouhým kompresním pásmem. jeho délka bývá 3 až 4 násobek
průměru šneku D. Šneky s krátkou kompresní částí,
rovnající se jednonásobku průměru šneku, jsou vhodné pro hmoty
s úzkým intervalem teploty tání, jako jsou krystalické polymery
PE a PA. Šnek s nevýraznou kompresní částí má jádro kónické po
celé délce a používá se u hmot se špatnou tekutostí nebo u hmot,
u nichž je nebezpečí degradace vlivem přiliž rychlého ohřevu,
např. PVC. Teplo potřebné k zahřátí a roztavení dostává
zpracovávaný plast jednak z odporových
topných pásů, jednak přeměnou mechanické práce šneku,
při čemž se ve vstupním pásmu jedná o teplo vzniklé třením a ve
výstupním pásmu o teplo z hnětací práce.
Tavicí komoraje pro účely vytápění obvykle rozdělena do tří zón (topných pásem)
samostatně vytápěných a se samostatnou regulací teploty, kdy
nejnižší teplota se nastavuje v pásmu u násypky a nejvyšší u
trysky. Teplota pásma u násypky, nesmí být příliš vysoká, aby
nedošlo k předčasnému natavení a následnému spečení granulí,
protože by to mělo za následek vytvoření zátky ve šnekovém
profilu a tím by se zamezilo přísunu dalšího materiálu do
kompresní části šneku. Proto se část tavicí komory, která
přiléhá k násypce, chladí.
Tavicí komora je zakončena vstřikovací tryskou. Trysky se konstruují buď jako
otevřené (vysoce viskózní materiály) s otvorem o průměru 3 až
8 mm, nebo jako uzavíratelné, které se otevřou pouze při dosedu vstřikovací
jednotky na formu. Tryska zajišťuje spojení mezi komorou a
formou, protože přivádí taveninu do vtokových kanálů ve formě.
4.3.2.
Uzavírací jednotka
Úkolem uzavírací jednotky je zavírat a otevírat formu dle
procesu vstřikování a zajistit uzavření formy takovou silou, aby
se při vstříknutí tlakem taveniny forma neotevřela. Při činnosti
formy je nutno rozlišovat sílu
přisouvací
Fp, a sílu uzavírací
Fu.
Současné moderní stroje mají programovatelnou rychlost a sílu
uzavírání vstřikovací formy.
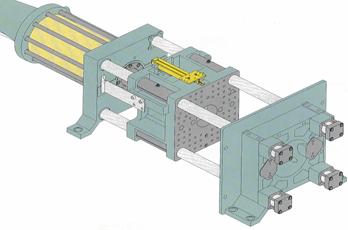
Schéma uzavírací jednotky
Uzavírací jednotka se skládá z těchto hlavních částí: opěrné
desky pevně spojené s ložem stroje, pohyblivé desky, na kterou
je upnuta pohyblivá část formy, upínací desky s otvorem pro
trysku stroje, na kterou se připevní nepohyblivá část
vstřikovací formy, vedení pro pohyblivou desku, z uzavíracího a
přidržovacího mechanismu. Vstřikovací stroje používají
v současné době různé uzavírací systémy, které např. mohou být
konstruovány jako hydraulické, mechanické, kombinace
hydraulického a mechanické způsobu (závorování) a v poslední
době se používají i elektrické systémy.
Vstřikovací
a uzavírací jednotky mají vůči sobě určité umístění, polohu.
Nejčastější uspořádání u vstřikovacích strojů je horizontální
poloha vstřikovací i uzavírací jednotky, tedy vstřikování kolmo
na dělící rovinu formy. V některých případech (reologické
chování taveniny, zakládání zálisků, dvoukomponentní vstřikování
speciální způsoby vstřikování, apod.) však může dojít k jiné
vzájemné poloze. Sedm různých poloh mezi vstřikovací a uzavírací
jednotkou je ukázáno na obrázku.
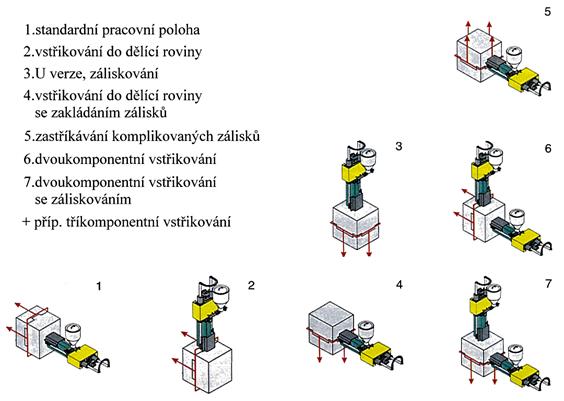
Vzájemná poloha mezi vstřikovací a uzavírací jednotkou
4.4. Vstřikovací formy
Formy pro zpracování musí odolávat vysokým tlakům, musí
poskytovat výrobky o přesných rozměrech, musí umožnit snadné
vyjmutí výrobku a musí pracovat automaticky po celou dobu své
životnosti. Jejich konstrukce a výroba je náročná na odborné
znalosti, ale i na finanční náklady. Volba
materiálu formy závisí na druhu zpracovávaného plastu, na
použité technologii, na velikosti výrobku a jeho složitosti, na
velikosti série, na tepelné odolnosti a odolnosti proti
opotřebení a korozi, na ceně, apod. Důležitým faktorem
životnosti formy je provedené tepelné zpracování na tvarových
částech nástroje. Dalším důležitým úkolem při konstrukci forem
je stanovení rozměrů a výrobních tolerancí tvarových částí. Pro
určení a výpočet těchto rozměrů jsou rozhodující
smrštění, tolerance jednotlivých rozměrů výlisku a
opotřebení činných částí nástroje. Nejdůležitější je však
smrštění zpracovávaného.
Vstřikovací formy jsou konstrukčně velmi rozmanité a lze je rozdělit do
následujících skupin:
- podle násobnosti na
jednonásobné a
vícenásobné,
-
podle způsobu zaformování a konstrukčního řešení na dvoudeskové, třídeskové,
etážové, čelisťové, vytáčecí, apod.,
- podle konstrukce vstřikovacího stroje na formy se vstřikem kolmo na dělící rovinu a na formy se vstřikem do dělící roviny.
Vstřikovací forma se skládá z dílů, vymezujících tvarovou dutinu formy, z
chladicího (temperačního) systému, z
vtokového systému, z
vyhazovacího systému a z upínacích a vodicích elementů.
Jednotlivé části vstřikovacích forem lze rozdělit do dvou skupin
na části konstrukční a na části funkční. Konstrukční části
zabezpečují správnou činnost nástroje a funkční části
se stýkají s tvářeným materiálem a udělují mu
požadovaný tvar. Pro představu o
tvarové a konstrukční složitosti vstřikovacích forem je na
obrázku ukázka konstrukce vstřikovací formy.
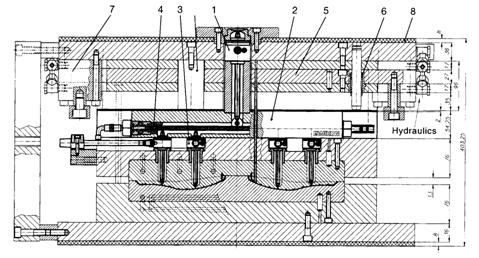
Ukázka konstrukce vstřikovací formy
Kvalitu a jakost výstřiku spolu s produktivitou výroby nejvíce ovlivňuje
vtokový systém, což je systém kanálů a ústí vtoku, který
musí zajišťovat správné naplnění dutiny formy, snadné odtržení
nebo oddělení od výstřiku a snadné vyhození vtokového zbytku.
Vtoková soustava je navrhována podle počtu tvarových dutin,
podle jejich
rozmístění a podle toho, zda bude konstruována jako studený
nebo horký rozvod. Konstrukční řešení vtokového systému závisí
na konkrétním tvaru výstřiku a na násobnosti formy. Při
vstřikování termoplastů má druh a umístění vtoku podstatný vliv
na proudění taveniny ve formě, vytváření tzv. studených spojů,
orientaci makromolekul a plniva, rovnoměrnost krystalizace,
anizotropii vlastností a rozměrů, povrchový vzhled, apod. Vtok
má být zásadně řešen tak, aby tavenina naplnila formu nejkratší
cestou bez velkých teplotních a tlakových ztrát, co nejrychleji
a pokud možno všude ve stejném čase. U
vícenásobných vstřikovacích forem je nejdůležitějším
požadavkem, aby všechny tvarové dutiny byly plněny současně a
při stejných technologických podmínkách, což znamená při stejné
teplotě taveniny a při stejném vnitřním tlaku. Při vstřikování
termoplastů má typ a umístění vtoku podstatný vliv na proudění
taveniny ve formě vytváření tzv. studených spojů, orientaci
makromolekul a plniva, rovnoměrnost krystalizace, anizotropii
vlastností a rozměrů, povrchový vzhled apod.
Pokud bude vstřikovací forma vícenásobná, tak umístění tvarových dutin je možné buď do
hvězdy, nebo v řadě.
Z hlediska plnění tvarových dutin je lepší uspořádání do hvězdy,
protože k zaplnění dochází ve stejném čase a při stejném tlaku,
kdežto u uspořádání v řadě se musí provést korekce ústí vtoku,
tzn. změnit rozměry rozváděcích kanálů směrem ke vzdálenějším
dutinám.
Pro zajištění opakovatelnosti výroby musí hmota v dutině formy zchladnout z technologického a
ekonomického hlediska co nejrychleji a proto vstřikovací formy
obsahují
temperační systém. Temperačním systémem se rozumí systém
kanálů a dutin, umožňujících přestup a prostup tepla z taveniny
do formy a temperovací kapaliny.
Teplota formy se udržuje na požadované výši pomocí
chladicího média, které protéká soustavou chladicích kanálů.
S ohledem na vlastnosti výrobku by bylo žádoucí, aby se hmota
ochlazovala ve všech místech stejnou rychlostí. Důsledky
nerovnoměrného ochlazování se projevují např. tím, že výrobek
obsahuje vnitřní pnutí nebo se deformuje a nebo vzniknou
trhliny. Temperační systém bývá rozdělen do dvou dílčích okruhů,
a to na okruh pro
pevnou neboli vtokovou část formy a na okruh pro
pohyblivou část. Každý z okruhů se dále může dělit na
podokruhy, které se řeší podle způsobu zaformování výstřiku ve
formě a podle polohy dělicí roviny.
Rozmístění temperačních kanálů a jejich rozměry je nutno
navrhnout s přihlédnutím k celkovému řešení formy, např.
umístění vtokové soustavy, vyhazovacích systému, tvarových
vložek a jiných dílů, ale i k požadavku na těsnost temperačního
okruhu.
Vzdálenost kanálů od líce formy má být navržena tak, aby
nedošlo k porušení povrchu tvarové dutiny formy a aby v tvarové
dutině nevznikala podchlazená místa. Výhodnější je použít větší
počet malých kanálů, než-li naopak. Kolem dutiny formy se kanály
rozmísťují rovnoměrně a v optimálním případě je jejich
vzdálenost od líce formy všude stejná. Pouze tam, kde je třeba
zvýšit intenzitu chlazení, se kanály přiblíží líci formy
nebo se zmenší vzdálenost mezi nimi. Průřez kanálů se volí
zpravidla kruhový a bývá 6 až 20 mm. Vedle kruhových kanálů se
používají i kanály s obdélníkovým průřezem. Celková délka kanálů
má být taková, aby rozdíl teplot temperační kapaliny na vstupu a
na výstupu byl max. 3 až 5 oC.
Mimo výše popsaných částí obsahují vstřikovací formy i různé
mechanismy pro vyhazování výstřiků, protože výrobky se při
ochlazování smršťují a zůstávají na tvarových součástech formy.
Nejčastější způsob vyhazování výstřiků je mechanický princip buď
pomocí vyhazovacích kolíků nebo pomocí stíracích desek,
stíracích kroužků, apod. V řadě případů se jednotlivé způsoby
kombinují. Vyhazovací síly a jejich výpočet se odvozuje od
měrných tlaků mezi formou a výstřikem, kdy síla na vyhození bude
záviset na pružnosti tvárníku a tvárnice, na průběhu tlaků a
teplot během vstřikování, na rozměrech výstřiku a na teplotní
závislosti koeficientu tření mezi oběma plochami.
Odvzdušnění tvarové dutiny u vstřikovacích forem je velmi důležité, protože doba vstřiku je
velmi krátká a mohlo by dojít k nedokonalému vyplnění tvarové
dutiny taveninou plastu, k nebezpečnému zvýšení tlaku, k poklesu
pevnosti v místech studených spojů nebo k tzv.
diesel efektu, kdy může dojít až ke spálení materiálu. Proto
je nutné zajistit intenzívní odvod vzduchu z tvarové dutiny
formy, a to nejenom netěsnostmi v dělící rovině, ale i
konstrukcí odvzdušňovacích kanálků, které však nesmějí být
příčinou vzniku otřepů na výrobku. Odvzdušnění má být provedeno
v dělící rovině na protilehlém místě vtoku. Na dostatečné
odvzdušnění formy má vliv umístění vtoku, způsob zaformování
výstřiku, umístění vyhazovačů, přítomnost tvarových vložek,
apod.
.: Jdi na začátek stránky :.
|