- Technologie tváření práškových kovů
12.1. Zhutňování kovových prášků
12.1.1. Lisování
12.1.2. Válcování
12.1.3. Kování
12.1.4. Speciální způsoby konsolidace
12.2. Spékání
12.
technologie tváření
práškových kovů
Výchozí materiál je v práškovém stavu, což
dovoluje téměř libovolně volit chemické složení materiálu podle
požadavků na vlastnosti konečného výrobku. Navzájem lze mísit
prášky kovů, chemických sloučenin kovů i organické látky
v různých poměrech a kombinacích. První oblastí zpracování
práškových kovů, je zpracování materiálů, které nemohly být
zpracovány klasickou technologií tavení a lití, např.
vysokotavitelné kovy (Pt, W, Mo, Ta, apod.). Druhou oblastí je
zpracování práškových kovů i řadou jiných klasických
technologií, např. sléváním, tvářením, obráběním, ale
technologie práškové metalurgie je technicky a ekonomicky mnohem
výhodnější. Třetí oblastí je zpracování práškových kovů
tvářením, např. kováním, protlačováním, válcováním, apod. při
současném zlepšení užitných vlastností a ekonomie výroby.
Prášky jsou charakterizovány fyzikálními (distribuce a
velikost částic, tvar a morfologie povrchu, tvrdost, atd.) a
technologickými vlastnostmi (lisovatelnost, tekutost, sypný
objem, atd.). Podle způsobu výroby mohu mít prášky různý tvar
(kulový, lístkový, nepravidelný, zrna zaoblená, atd.). Prášky je
možno vyrábět fyzikálními, fyzikálně-chemickými, chemickými nebo
elektrochemickými způsoby. Z ekonomického hlediska má největší
vliv cena prášku. Vhodně upravené prášky se zpravidla lisují do
požadovaného tvaru a získaný tvar se následně zpracovává
spékáním, aby se dosáhlo potřebných fyzikálních a mechanických
vlastností. Největší výhodou práškové technologie je vysoké
využití kovu při nižší spotřebě energie, snížené pracnosti a
nákladech, čistota prostředí. Další výhodou je isotropie
mechanických vlastností.
12.1. Zhutňování kovových prášků
Velikost stykové plochy částic práškového kovu bude záviset na stupni a
kvalitě vazby mezi jednotlivými částicemi – stupni konsolidace.
U plně konsolidovaného tělesa se dotýkají všechny práškové
částice navzájem po celém povrchu (stejně jako u tuhých těles),
ale v sypkém stavu je velikost kontaktů jen velmi malou částí
celkového povrchu všech částic. Hodnoty fyzikálních a
mechanických vlastností budou vzrůstat v závislosti na
zvětšování kontaktních ploch částic. Stupeň konsolidace
práškového tělesa zpravidla zvyšuje působením tlakových sil
nebo spékáním, ve většině případů oběma způsoby. Většinou se
používá různých způsobů lisování.
12.1.1. Lisování
Těleso z práškových kovů má objem jednak pevných částic a jednak mezer
(pórů). Objem mezer je závislý na způsobu lisování a velikosti
lisovacího tlaku. Při stlačování prášku v dutině nástroje působí
vnější (mezi práškovým materiálem a stěnou dutiny lisovací
formy) i vnitřní tření (tření mezi částicemi). Tření, které je
možné snížit použitím mazadel, má za následek nerovnoměrné
rozdělení hustoty ve výlisku. Podle směru působícího tlaku
rozdělujeme lisování na jednosměrné, obousměrné a izostatické.
Při jednostranném lisování je nejvyšší hustota v oblasti pod
lisovníkem, při oboustranném lisování je nejnižší hustota ve
středu výlisku. Při izostatickém lisování je prakticky
odstraněno vnější tření a výrobek vykazuje rovnoměrnou hustotu.
Následuje spékání. Ke snížení pórovitosti se může lisování i
spékání vícekrát opakovat. Lisovací tlaky se pohybují od 50 do
1800 MPa a pórovitost je 50 až 8 %. K lisování se používají
mechanické nebo hydraulické
lisy.
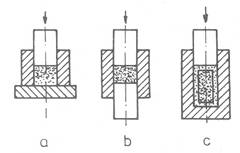
Základní způsoby lisování
(a – lisování jednosměrné, b – lisování obousměrné, c – izostatické lisování
12.1.2. Válcování
Válcováním se vyrábějí polotovary ve formě pásků,
tyčí, plechů, apod. Prášek je plynule dodáván ze zásobníku do
mezery mezi válci, kde je třecími silami unášen a tlakem válců
stlačován. Princip je znázorněn na obrázku. Poměrně pevný a
ohebný pás je veden do spékací pece. Podle požadované hustoty se
může válcování i spékání vícekrát opakovat. Vhodnou konstrukcí
násypky je možno vyrábět i vícevrstvé polotovary.
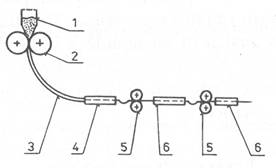
Schéma výroby polotovarů válcováním práškových kovů
1 – násypka, 2 – dvouválec, 3 – skluz, 4 – spékací pec, 5 – dvouválec, 6 – žíhací pec
12.1.3. Kování
Kováním se dosahuje
lepších mechanických vlastností a odstraňuje se zbytková
pórovitost. Výchozím polotovarem může být buď výlisek, který se
spéká v průběhu ohřevu na tvářecí teplotu nebo spékaný
polotovar, který je možné kovat přímo po vyjmutí ze spékací
pece. Volné kování se používá hlavně pro velké polotovary,
zápustkové kování pro výrobky s vysokými nároky na přesnost.
Volí se poměrně malé deformace.
12.1.4. Speciální způsoby
konsolidace
Lisováním za
tepla, které spojuje operaci lisování se spékáním, lze dosáhnout
i plné hustoty výlisků. Prášek je lisován poměrně nízkým tlakem
při teplotách až 2500 oC v ochranné atmosféře, vakuu
nebo vzduchu. Izostatické lisování za studena je vhodné
pro tvarově složité výrobky. Vibračně zhutnělý prášek je uzavřen
v tenkém elastickém obalu a vystaven postupnému hydrostatickému
tlaku kapaliny až 600 MPa. Výhodou je vysoká hustota a izotropní
vlastnosti. Izostatické lisování za tepla je vhodné
pro dosažení bezporézního stavu. Prášek v kovovém obalu je
vystaven působení tlaku a teploty. Jako tlakové médium se
používá argon. Protlačování za tepla se používá hlavně pro AL,
Mg, Ag, apod. Ve speciálních případech je možné použít
hydroimpulzivní lisování, lisování v magnetickém poli,
explozivní lisování, vstřikování, přetlačování, lití, lití se
zmrazením, technologie velmi vysokých tlaků, apod.
12.2. Spékání
Spékání je způsob tepelného zpracování zhutněných částic nebo práškového výlisku,
při kterém se z pórovitého výlisku stává souvislé těleso za
působení teploty a případně tlaku. Zvětšuje se celková plocha
styku částic, snižuje se pórovitost, zvyšují se fyzikální a
mechanické vlastnosti, dochází k objemovému smrštění. Teplota
spékání se volí v rozmezí 0,6 až 0,9 teploty tavení. Spékání
může probíhat za normálního tlaku nebo pod tlakem vnějších sil.
Spékání se provádí v elektrických pecích s ochranou atmosférou
redukčních či inertních plynů nebo vakuu. Nejdůležitějšími
parametry spékání jsou teplota, doba spékání a ochranné
prostředí.
.: Jdi na začátek stránky :.
|