- Technologie objemového tváření – kování
3.1. Stupeň deformace a prokování
3.2. Výpočet síly a práce při kování
3.3. Rozdělení kování
3.3.1. Volné kování
3.3.2. Zápustkové kování
3.4. Speciální způsoby kování
3.4.1. Přesné kování
3.4.2. Kování na vodorovných kovacích strojích
3.4.3. Kování protlačováním
3.4.4. Kování za rotace
3.4.5. Vícecestné kování
3. Technologie objemového tváření -
Kování
Kováním rozumíme objemové tváření za tepla, prováděné úderem nebo klidně
působící silou. Kování má bohatou historii - ruční kování pomocí
kladiva kovadliny zná lidstvo několik tisíců let. Jedná se o
přetržitý způsob a výkovek má požadovaný tvar, příznivou
makrostrukturu, výhodnou mikrostrukturu a zvýšené mechanické a
fyzikální vlastnosti. Kováním lze zpracovávat téměř všechny
kovy.
 Kovací teploty v diagramu Fe – Fe3C
Strojní kování zproduktivňuje výrobu malých a středně velkých
výkovků a umožňuje zpracování těžkých odlitků. Hlavní důraz při
kování se klade na nejmenší spotřebu materiálu, optimální
přesnost výkovku, vysokou jakost tvářeného kovu, příznivý průběh
vláken a na ekonomii provozu. Kování nejenom umožňuje vyrábět
tvary požadovaného rozměru, ale zároveň i zlepšovat původní
mechanické vlastnosti a strukturu - kování má
velký význam nejenom pro tvarování výrobků, ale i pro zlepšení
jejich mechanických vlastností (stupeň prokování). Účelem
prokování je odstranění nestejnorodé hrubé licí struktury a
metalurgických vad u ingotů, které snižují tvárnost a fyzikální
a mechanické hodnoty a vlastnosti kovu.
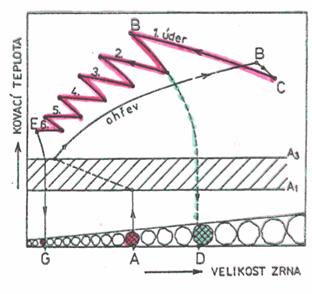 Kovací diagram
3.1. Stupeň deformace a prokování
Tvářením za tepla se tvar primárních
krystalů, dendritů, mění (dochází k jejich rozrušování) a
vytvářejí se vlákna. Protože však nastává dynamická
rekrystalizace, deformovaná zrna se změní na nová, jemnější a
textura zmizí. Avšak nečistoty v povrchových vrstvách krystalů
nepodléhají rekrystalizaci a proto nemění svůj tvar - vzniká
vláknitá textura, kterou nelze žádným tvářením ani tepelným
zpracováním odstranit.
Vláknitost
má vliv na anizotropii vlastností (mechanické vlastnosti,
tažnost, …) ve směru vláken a ve směru příčném a mění se stupněm
prokování p (praktická hodnota prokování je 3 až
4) a stupněm deformace. Proto se musí při tváření za tepla vždy
pamatovat na správný směr vláken. Směr největšího normálového
napětí má souhlasit se směrem vláken a tečné napětí má být
k němu kolmé. Vlákna nemají být přerušena a mají se shodovat
s obrysem součásti.
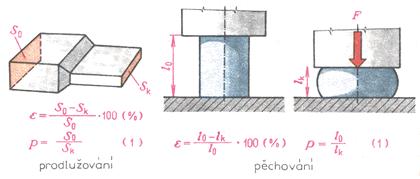 Stupeň
deformace a prokování pro základní operace kování
3.2. Výpočet síly a práce při kování
Velikost deformační síly
[N] je dána součinem přetvárného odporu (odpor proti tváření) a průmětu
plochy polotovaru do roviny kolmé ke směru působící síly:
F =
ko . S
kde ko = kp .
m
kde: ko … přetvárný odpor [MPa]
kp … přetvárná pevnost [MPa]
S … plocha kovadel [mm2]
m … koeficient závislý na způsobu tváření, tvaru a
rozměrech a na tření
3.3. Rozdělení kování
Kování dělíme na
volné, tj. na
kovadlině nebo pomocí univerzálních kovacích podložek, a
zápustkové, tj. ve tvarových dutinách (zápustkách).
Při volném kování může materiál tvářený údery nebo tlakem téct
volně hlavně ve směru kolmém k působení síly. Při zápustkovém
kování je materiál vtlačován údery nebo tlakem do kovové,
většinou dvoudílné zápustky.
3.3.1. Volné
kování
K volnému strojnímu kování se
používá různých tvářecích strojů, zejména bucharů a lisů.
Buchary působí na materiál údery (rázy) beranu, ale prokovou
jej jen do určité hloubky. Proto buchar působí více rázy a díky
tomu je možné dosáhnout vyššího stupně prokování. Při úderech
beranu odpadají z materiálu okuje a proto je povrch výkovků
čistý.
Lisy působí na materiál klidným tlakem a prokovou materiál
v celém průřezu.
Problematika kování je vázána
na vliv tření mezi tvářecími části nástroje a materiálem, které
způsobuje soudečkovitost výkovku nebo vyboulení u dlouhých těles
a dále rozdílné stupně prokování v jednotlivých oblastech
výkovku (je nutné otáčení) – mluvíme o
kovářském kříži.
Volně kované výkovky se navrhují vždy
v jednodušším tvaru, než jaký má mít výkovek. Tvarovanému
zjednodušení se říká technologický přídavek. Vedle
technologických přídavků má výkovek ještě přídavky na obrábění,
a to v náležitých tolerancích. Pro správné stanovení
technologického postupu je potřeba znát výkres obrobené
součásti, hmotnost součásti (pro stanovení kovacích časů), druh
a velikost stroje a chemické složení materiálu (pro stanovení
kovacích teplot).
K výrobě pomocí volného kování se používá jednoduchých
kovářských nástrojů, přípravků a strojů. Pi
volném kování docilujeme žádaný tvar výkovku pomocí
univerzálních kovadel a speciálním polohováním výkovku.
Úchylky rozměrů výkovků jsou velké,
povrch je hrubý, nerovný. Výchozím materiálem jsou buď předvalky
nebo ingoty.
Nejpoužívanější nástroje jsou kovadla (horní a spodní).
Kovadla jsou
jednoduchých geometrických tvarů, jako např. kovadla rovinná,
válcová, klínová, apod. – viz. obr. 3.4. Rybinovité části
kovadel slouží k upevnění na bucharu nebo lisu. Díry v čelní
stěně slouží pro manipulaci s nástrojem. Pracovní plochy kovadel
jsou kaleny. Docílení výsledného tvaru vyžaduje
uvědomělý sled operací, při kterém všechny prostorové změny
tvaru převádíme na pěchování.
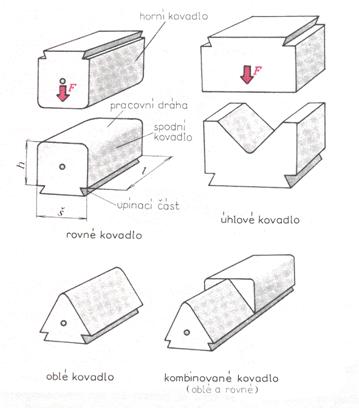 Tvary kovadel
Mezi základní práce a principy volného kování patří
pěchování. Pěchování je nejjednodušší tvářecí přetvárný proces,
při kterém dochází k plastické deformaci materiálu mezi dvěma
plochými nebo tvarovými čelistmi, resp. v dutině. Pěchování je na druhé straně silově a energeticky
nejnáročnější kovářskou operací. Je to buď přímá kovářská
operace při kování plochých výkovků a nebo předběžná operace pro
dokonalé prokování materiálu, snížení anizotropie a výhodnější
průběh vláken. Zmenšuje se výška a zvětšuje se plocha průřezu
Pro pěchování je nutné prohřát celý materiál rovnoměrně a zajistit
rovnoběžnost čelních ploch, omezit štíhlost polotovaru
(nebezpečí ohybu) a zajištění kolmosti k ose stroje.
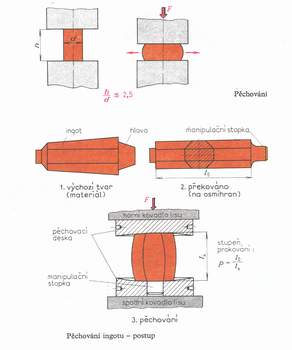 Pěchování válcových polotovarů
Další technologií volného kování je prodlužování (kování do délky, vytahování). Je to nejpoužívanější
operace při volném kování. Podstatou je provedení většího množství pěchovacích operací vedle sebe, čímž dochází
k prodlužování a zároveň ke zmenšení plochy příčného průřezu.
Polotovarem se nejčastěji střídavě otáčí o 90o a posouvá o posuv p, čímž se vyrovnává rozšíření.
Záběr p je vždy menší, než šířka kovadla s.
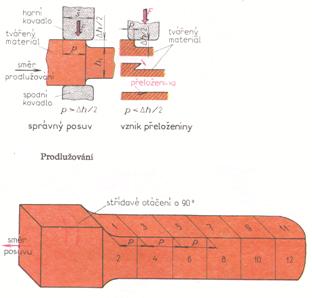 Prodlužování
Na obrázku je schéma operace osazování (naznačování) a prosazování, přesazování a děrování. Osazovat
můžeme buď jednostranně nebo oboustranně. Naznačením dvou míst na protilehlých stranách výkovku můžeme
vykovat přesazení, dvojím přesazením lze vykovat zalomení.
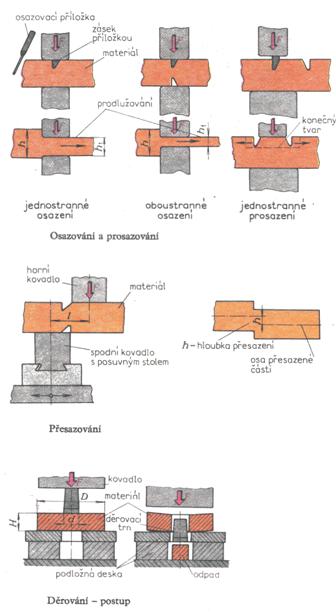 Operace volného kování
U děrování se mírně kuželový trn se vtlačí
do materiálu asi na 1/2 výšky. Poté se výkovek obrátí a z druhé
strany se děrování dokončí. Takto se vyrábějí otvory od průměru
40 mm, u menších hrozí zlomení děrovacího trnu. Zbylá blána se
následně prostřihne.
3.3.2. Zápustkové
kování
Zápustkové kování slouží k výrobě velkého
počtu tvarově stejných součástí z ocelí nebo jiných tvárných
slitin. Zápustka je většinou dvoudílný nástroj. Hlavní předností
zápustkového kování je vysoká výkonnost a snadná obsluha.
Výkovky mají však omezené rozměry a hmotnost.
Ohřátý materiál se tváří v dutině zápustky, jejíž tvar je shodný s tvarem
výkovku. Rozměry jsou však zvětšeny o hodnotu smrštění
vychladlého výkovku. Proti volnému kování se dosahuje
přesnějšího tvaru výkovku. Přesnost a jakost povrchu se dá
výrazně zlepšit následným kalibrováním tak, že se nemusí již
dále používat obrábění. Zápustkovým kováním se dosahuje vysokého
stupně prokování a průběh vláken sleduje obrys výkovku. Při
zápustkovém kování se postupuje tak, že se výchozí polotovar,
ohřátý na potřebnou kovací teplotu, vloží do dutiny zápustky a
působí se na něj tlakem nebo údery tvářecího stroje.
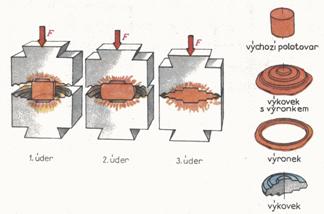
Postup kování v jednodutinové zápustce na bucharu
K zápustkovému kování používáme bucharů
(kování úderem) a lisů (kování klidným tlakem). Dutinu zápustky
je možno zaplňovat buď vtlačováním nebo pěchováním - z čehož
pěchování je lepší. Při kování na bucharech je zápustková dutina
vyplňována postupně během několika úderů beranu, při kování na
lisech je výkovek zhotoven v průběhu jednoho zdvihu nebo
několika zdvihů (postupová zápustka). Při konstrukci
zápustkových bloků je důležitou částí řešení způsob upnutí
zápustky na kovací stroj, hlavně na buchar. Rázy při kování
totiž velmi snadno upevnění zápustek povolují. Pro buchary se
zápustka opatřuje s úspěchem rybinou a upíná se pomocí pera a
klínu. Kování na lisech - tím se rozumí obvykle kování na
svislých klikových lisech, vhodné pro velké série a jednodušší
tvary výkovků. Zápustky mají jiný způsob upínání než na
bucharech. Upínají se pomocí stopek, šroubů a příložek. Výkovky
mohou mít menší úkosy, na lise je možno použít vyhazovačů.
Výkovky se často sdružují ve vícenásobných dutinách. Po vykování
spolu výkovky souvisí za výronek, takže k jejich oddělení dojde
po odstřižení výronku. Kovat lze též na třecích lisech.
Jedná se převážně o výkovky rotačních tvarů, kovaných ve svislé
poloze.
Pro složitější tvary výkovků v zásadě platí tato pravidla:
- v jedné dutině se nesnažíme deformovat kov v příčném i podélném směru současně
- rozdělení matriálu v podélném směru provedeme dříve než ve směru příčném
- tvar předkovku navrhneme tak, aby při kování docházelo k posuvu částic v příčných řezech a předkovek měl rotační tvar
Při zápustkovém kování záleží počet kovacích dutin na tvaru výkovku, ale
též na tvaru výchozího materiálu. Jen zřídkakdy se stane, že k
vykování výkovku stačí jedna dutina. Jednotlivé dutiny se často
umísťují do společného bloku oceli - nástroje, což je pro práci
na bucharu výhodné. Přenášení výkovku z jedné dutiny do druhé
netrvá příliš dlouho, výkovek nechladne rychle. V případě
složitějších tvarů je tedy nutno kovat ve více dutinách, které
zajistí tečení materiálu v dutině zápustky –
kování v postupových zápustkách.
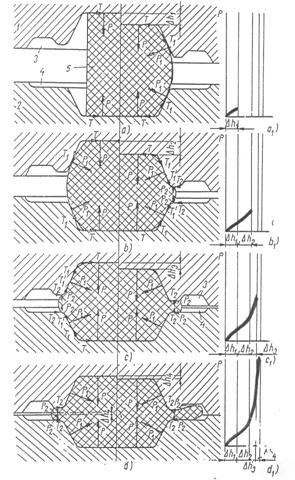 Schéma tečení materiálu v dutině postupové zápustky
Postupová zápustka může být někdy konstruována pomocí
výměnných tvarových vložek kruhového nebo obdélníkového tvaru.
Dochází zde k výrazné úspoře materiálu zápustky. Kování v
zápustkách bez dutiny pro výronek se říká tzv. kování
v uzavřených zápustkách. Je velmi náročné, protože objem
materiálu musí být velmi přesně stanoven. Na obrázku je ukázka
postupové zápustky pro buchar. V postupové zápustce nejsou
dutiny umístěny za sebou podle technologického postupu. Kovací
(dokončovací), tj. poslední dutina se umisťuje uprostřed tak,
aby její těžiště bylo blízko těžiště celého bloku. To proto, že
síla (nebo energie) na kování výkovku je větší, než na kování
předkovků. Jednak proto, že výkovek chladne a tedy roste jeho
přetvárná pevnost a dále proto, že výkovek včetně výronkové
drážky má největší plochu. Ostatní dutiny jsou rozmístěny kolem
této dokončovací dutiny. Operace zápustkového kování pak dělíme
např. na rozdělování, předkování, kování a odstřižení výronku.
Toto rozdělení je nejobvyklejší, avšak není jediné. Během kování
je možné výkovek přenášet a do dutin ukládat buď pomocí kleští
za zbytek tyče původního materiálu nebo pomocí robotů a
manipulátorů. K oddělení tohoto zbytku slouží utínka, tj. ostrá
hrana v pravém dolním rohu. Odstřižení výronku se provádí
v jiném nástroji. Předkování se může provádět volně,
v zápustkách nebo na kovacích válcích.
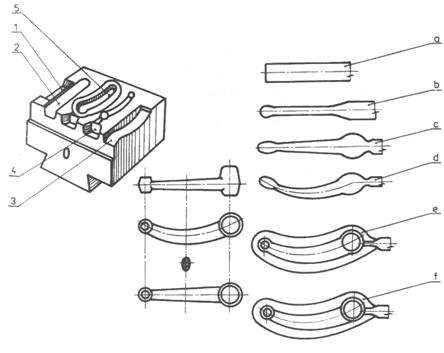 Postupová zápustka pro buchar (1 – prodlužovaní,
2 – rozdělovací, 3 – předkovací, 4 – kovací, 5 – dokončovací dutina, a – polotovar)
Kovací (dokončovací, finální) dutina je opatřena okolo obrysu tvaru
výkovku ještě výronkovou drážkou. Její průřez pro zvolený kovací
stroj je znázorněn na obrázku. Zúžená část se nazývá můstkem,
rozšířená zásobníkem. Funkce výronku je dvojí. Jednak pojmutí
přebytečného materiálu, neboť materiál musí dokonale vyplnit
dutinu a jednak ovlivnění toku materiálu uvnitř zápustky.
Výronek se dodatečně odstraňuje ostřihováním.
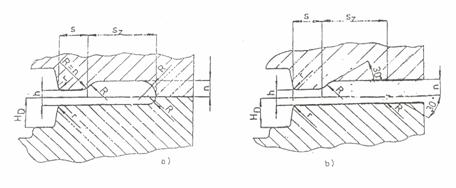 Výronková drážka (vlevo) v zápustce (a – buchar, b – lis) a
tok materiálu ve výronkové drážce (vpravo)
Konečné úpravy výkovků jsou tedy odstřižení výronku, popř. prostřižení blan v otvorech, rovnání výkovku, výkovek se
zbavuje okují (moření, otryskávání), tepelně zpracovává (normalizační žíhání) nebo za studena kalibruje.
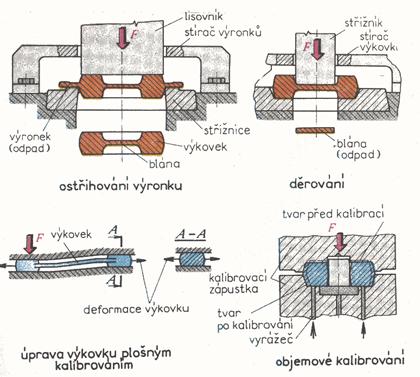 Úprava výkovků
Nejprve se pro žádaný tvar určí dělící rovina. Ve slévárenství
jsme s výhodou volili jako dělící rovinu jednu z hlavních rovin
odlitku.
V kovárenství naopak volíme dělící rovinu
středem nejhmotnější části výkovku. Ke zvolené dělící rovině
aplikujeme úkosy tvarů. Velikost úkosů pro zápustkové výkovky
kované na bucharech je 5 až 8o a při kování na lisech
asi 3o. Velikost úkosu je ovlivněna hloubkou dutiny,
možností použití vyhazovačů, apod. Otvory v zápustkovém výkovku
se nikdy nekovou. Do průměru asi 40 mm se vynechávají, od
uvedené hodnoty výše se naznačují. Otvor se následně vyrobí
třískovým opracováním. Úkosy vnitřních otvorů se dělají větší,
než úkosy stěn. Pro správné stanovení technologického postupu je
potřeba znát výkres výkovku, hmotnost součásti (pro stanovení
kovacích časů), zvolit ideální předkovek (aby nedocházelo k
rozstříknutí materiálu, musí mít předkovek co neideálnější tvar
ke konečnému výrobku), navrhnout zápustku, druh, velikost stroje
a chemické složení materiálu (pro stanovení kovacích teplot).
Zápustky se zhotovují z ocelí,
které mají zvýšenou odolnost proti otěru a pracovním teplotám a
jsou zušlechtěny.
3.4. Speciální způsoby
kování
3.4.1.
Přesné kování
Výkovky s minimálními přídavky na obrábění i úkosy se zhotovují
v uzavřených zápustkách, tzv. přesným kováním. Pro úspěšné
kování je třeba přesně dodržovat objem a středění vloženého
materiálu do zápustky. Nejvýhodnější jsou rotační tvary.
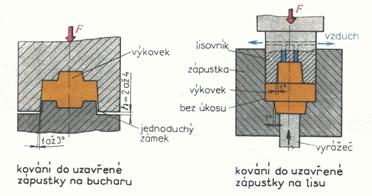 Přesné kování
3.4.2. Kování na vodorovných
kovacích strojích
Kování na
vodorovných kovacích strojích umožňuje částečnou nebo i úplnou
automatizaci výrobního procesu. Jedná se v podstatě o
horizontální klikové lisy vhodné hlavně pro pěchování z tyčového
materiálu a práci s uzavřenými zápustkami. Princip práce je
naznačen na obrázku. Zápustka je třídílná, uzavřená, kove se bez
výronku. Dutinová část zápustky je dvoudílná, dělená svislou
nebo vodorovnou dělící rovinou, opatřená zdrsněným průchodem pro
tyčový materiál. Po přiblížení obou polovin působí jako
sklíčidlo tyčového
materiálu. Třetí, pěchovací díl se do dutiny osově zasouvá.
Stroj pracuje tak, že se tyč posune do kovací polohy, na
zarážku. Tím je přesně určen objem kovaného materiálu. Potom
dvoudílný blok tyč sevře a zarážka se odsune. V této fázi se
vyčnívající konec tyče ohřívá, dnes nejčastěji indukčně. Po
zpěchování ohřátého konce tyče oddělí posuvný nůž výkovek od
tyče a pracovní cyklus se může opakovat.
 Kování na vodorovných kovacích strojích
3.4.3. Kování protlačováním
Dalším
technologickým procesem je kování - protlačování za tepla, kdy
tvářený materiál je v uzavřené zápustce stlačován průtlačníkem.
Je to vlastně kombinace protlačování a kování. Tento způsob se
používá pro slitiny hliníku a mědi, ale i pro ocel. Zvyšuje se
tvárnost kovu, protože materiál je vystaven prostorové tlakové
napjatosti. Může být řešeno jako dopředné, zpětné nebo sdružené.
Je zde velký vliv tření a je potřeba brát v úvahu vysokou
pevnost nástrojů a teplotní odolnost nástrojů.
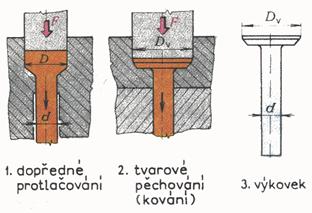 Kování protlačováním za tepla
3.4.4. Kování za rotace
Zvláštním případem kování je tzv. kování za rotace. Dochází při něm
k redukci průřezu na menší průměr nebo k vykování válcové části
na hranatém profilu. Na rozdíl od ostatních procesů kování se
kování za rotace provádí za studena. Součásti větších průměrů
(nad) se kovou za tepla. Mezi
kování je řadíme hlavně proto, že deformace nastává opakovanými
údery. Princip stroje je na obrázku. Dvě kovadla s možností
posuvu v radiálním směru se roztočí. Odstředivou silou jsou
unášena směrem k obvodu, kde však narážejí na kalené válce,
které jim udělují zpětný impuls. Tím vzniká opakovaný ráz.
Polotovar se pomalu otáčí a osově posunuje do procesu tváření.
Příklady rotačního kování a metody rotace jsou ukázány na
obrázcích.
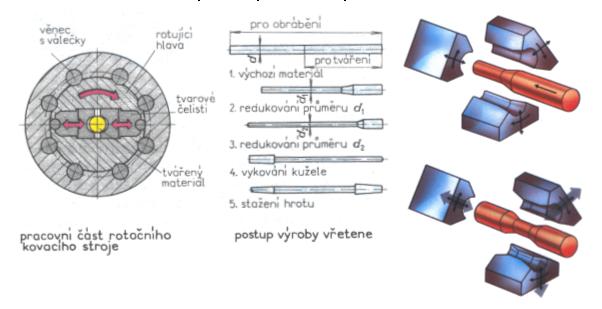 Princip kování za rotace
3.4.5. Vícecestné kování
Posledním speciálním způsobem kování je
kování vícecestné. Materiál je v uzavřené zápustce podroben
tlaku lisovníků z několika stran. Výkovky jsou přesné
s minimálními přídavky na obrábění.
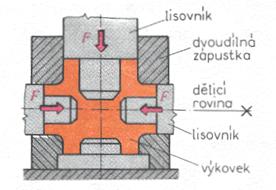 Vícecestné kování
.: Jdi na začátek stránky :. |