- Technologie objemového tváření – válcování
2.1. Princip a metody válcování
2.2. Tvar a geometrie válců, válcovací tratě
2.3. Výroba polotovarů válcováním
2.3.1. Válcování drátů
2.3.2. Válcování plechů
2.3.3. Válcování profilů
2.3.4. Válcování trubek
2.3.5. Válcování kotoučů a kroužků
2.4. Speciální způsoby válcování
2.4.1. Příčné klínové válcování
2.4.2. Válcování kuličkových polotovarů
2.4.3. Válcování závitů
2.4.4. Válcování na kovacích válcích
2.4.5. Válcování metodou Slick-Mill
2. Technologie objemového tváření - válcování
Technologie objemového tváření se týká tváření, při němž je
trojosá napjatost. Jako polotovar se používá přístřih tyče,
sochoru, apod. Dále uvedené technologie mohou teoreticky
probíhat při libovolných teplotách, tedy za studena, za tepla a
za poloohřevu.
2.1.
Princip a metody válcování
Ztuhlé ocelové ingoty o hmotnosti kolem 10 t se prohřívají v hlubinných pecích
na teplotu tváření kolem 1100 oC a válcují se na
předvalky. Z těch se pak vyrábějí válcováním konečné výrobky –
vývalky (tyče,
kolejnice,
plechy, pásy,
trubky, apod.).
Válcováním rozumíme kontinuální proces, při kterém se tvářený materiál
deformuje mezi otáčejícími se pracovními válci za podmínek
převažujícího všestranného tlaku. Válcovaný materiál se mezi
válci deformuje, výška se snižuje, materiál se prodlužuje a
současně rozšiřuje a mění se i rychlost, kterou válcovaný
materiál z válcovací stolice vystupuje. Mezera mezi pracovními
válci je menší, než vstupní rozměr materiálu. Válcování se
provádí hlavně za tepla, ale i za studena. Výsledkem procesu je
vývalek. Podle směru, kterým válcovaný materiál prochází
pracovními válci, podle uložení os válců vzhledem k válcovanému
materiálu a podle průběhu deformace válcování dělíme na podélné,
příčné a kosé.
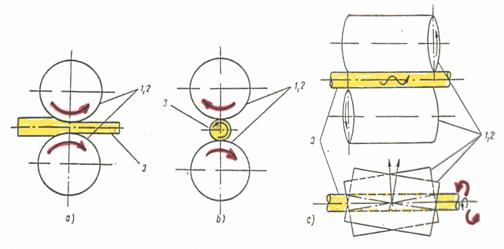
Princip podélného (vlevo),
příčného (uprostřed) a kosého (vpravo) válcování (1, 2 – válce, 3 – materiál)
U podélného válcování se materiál tváří ve
směru podélném a tímto způsobem se vyrábějí tyče, kolejnice, tj.
dlouhé polotovary. Příčným válcováním se redukuje radiální
průřez a tento způsob se používá např. pro osazené hřídele. U
kosého válcování jsou mimoběžné osy a takto se vyrábějí např.
trubky.
Při podélném válcování neprobíhá plastická
deformace současně v celém objemu, ale pouze v relativně malé
části, omezené body AA´a BB´. Největší rozměrová změna,
deformace, je ve směru tloušťky a menší rozměrové změny jsou ve
směru délky a šířky při zachování platnosti zákona o zachování
objemu. Napěťový stav závisí hlavně na tření a deformace s sebou
nese i změnu rychlostí materiálu vývalku na výstupu.
Proces válcování je umožněn jen v důsledku tření mezi pracovními
válci a válcovaným materiálem. Koeficient tření
f
je závislý na kvalitě povrchu válců, tedy na stykových plochách
a také na měrném tlaku, tedy na charakteru prokluzu. Součinitel
tření a měrný tlak způsobují vznik dvou sil v místě válcování, a
to normálové a tečné síly. Limitní podmínkou válcování, která
vychází ze silového působení normálových a třecích sil v místě
válcování je, že součinitel tření musí být vyšší (nebo minimálně
roven) než polovina úhlu záběru, tedy
f
>
tg
ao
/2
.
 Deformace během válcování
Koeficient tření se během válcování mění, a to hlavně mezi
začátkem válcování a mezi ustáleným válcováním. Při válcování za
tepla se součinitel tření výrazně mění se změnou chemického
složení kovu (oceli s vyšším obsahem uhlíku mají nižší
součinitel tření) a zpětně, každé oceli přísluší maximální
součinitel tření pro dané podmínky a teplotu. Při vysokých
teplotách ovlivňuje součinitel tření vznik okují, součinitel
tření klesá. Při malých rychlostech se součinitel tření mění jen
nepatrně, potom nastává výrazný pokles a při vyšších rychlostech
je součinitel tření v podstatě stálý.
Úběr (změna
z původní tloušťky před válcováním na tloušťku po válcování) a
tím i produktivita procesu může být tím větší, čím budou válce
menšího průměru a čím více budou drsnější. Součinitel tření se
snižuje se stoupající tvrdostí povrchu. Válce malého průměru
však lze používat s ohledem na tuhost pouze při menších šířkách
válcovaného materiálu a drsný povrch válců není vhodný pro
dokončovací operace, protože by se tím porušil povrch vývalku.
Z této úvahy vyplývá nutnost válcování menšími úběry, ve více
válcovacích operacích. S výhodou se volí počáteční operace
s velkým úběrem při méně kvalitním povrchu vývalku a koncové
operace s malým úběrem.
2.2.
Tvar a geometrie válců,
válcovací tratě
Tvar a
velikost pracovních válců může být rozmanitý. Pracovní válce
mohou být buď válcové nebo válcové s kuželovým zakončením a nebo
mezi kotouči, zvanými „hřibové válce“. Po vlastním procesu
válcování musí následovat kalibrace rozměrů, jakosti struktury a
povrchu a tvaru a ta je vždy závislá na tvaru konečného
polotovaru.
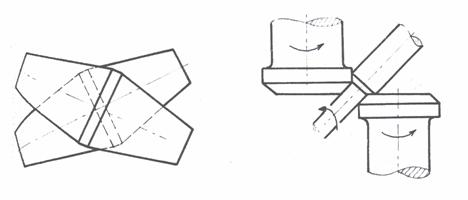 Válce s kuželovým zakončením a hřibové válce
Hlavní výrobní jednotkou je
válcovací trať, což je ucelený soubor strojů, potřebných
k válcování. Válcovacími tratěmi tedy rozumíme seskupení různého
počtu válcovacích stolic (seskupení hladkých nebo kalibrovaných
válců ve stolici s příslušenstvím) do výrobních linek v počtu od
jedné do dvanácti i více. Tratě pro hrubé předvalky mají
obyčejně počet válcovacích stolic nízký, úběry velké a počet
operací se provádí opakováním proběhů při stálém seřizování
válcovací mezery. Tratě pro jemné předvalky a vývalky mají počet
válcovacích stolic větší a každá stolice je seřízena pro jednu
operaci. Zařízení válcovacích tratí se dělí na základní a na
pomocná zařízení (pohyb materiálu, ohřev, dělení, rovnání,
apod.)
Válcovací tratě se dají rozdělit podle
těchto hledisek:
- podle konstrukce
válcovací stolice a počtu válců ve stolici na duo, trio,
kvartu, mnohoválcové stolice, planetové stolice a speciální
stolice,
- podle
druhu vývalků a průměru pracovních válců na stolice pro
výrobu drátů, plechů, univerzální, hrubé, střední, …,
- podle
způsobu otáčení válců na jednosměrné a zpětné
- a
podle uspořádání válcovacích stolic na tratě nad sebou nebo
vedle sebe, průběžné.
2.3.
výroba polotovarů válcováním
Válcováním lze vyrábět velké množství polotovarů rozmanitých tvarů. Mezi
základní patří profily, plechy, dráty, trubky.
2.3.1. Válcování drátů
Dráty se válcují na speciálních válcovacích tratích za tepla, které jsou
kontinuální, nepřetržité.
2.3.2. Válcování plechů
Plechy se válcují ve válcovacích stolicích s hladkými válci
z plochých předvalků. Nejprve se válcuje napříč, aby se dosáhlo
potřebné šířky plechu a potom se plech otočí o 90o a
válcuje se podélně. Tím se dosáhne stejnoměrné tloušťky a
rovnoměrnějších vlastností materiálu v podélném i příčném směru
válcování. Vyrábějí se jak plechy tlusté, tak i tenké. Hranicí
jsou 4 mm. Plechy mohou být pocínované, pozinkované, poolověné
nebo lakované. Válcování za studena se používá pro výrobu plechů
s hladkým povrchem a velkou přesností, i když výchozím
polotovarem jsou pásy válcované za tepla. Hlubokotažné plechy
jsou plechy s dobrými mechanickými vlastnostmi, např.
převálcované za studena.
2.3.3. Válcování profilů
Profily různých tvarů a rozměrů se válcují na
profilových válcovacích stolicích. Válcovaný materiál
prochází postupně kalibry, které se zmenšují, aniž se válce
k sobě přibližují. Poslední kalibr má tvar požadovaného profilu.
Válcují se jak profily kruhové, čtyřhranné, šestihranné, atd.,
tak tyče různých profilů jako I, U, L, kolejnice atd.
2.3.4. Válcování trubek
Trubky
(bezešvé) se také vyrábějí převážně válcováním. Rozměry trubek
jsou dány jejich průměrem a tloušťkou stěny. Podle použité
výrobní technologie rozdělujeme trubky z hlediska válcování na
válcované za tepla a za studena, redukované za tepla a za
studena a podle provedení na hladké, závitové, s tvarovými
konci, atd. Jejich výrobu můžeme rozdělit zhruba do dvou
základních operací:
-
výroba dutých polotovarů
s velkou tloušťkou stěny pomocí kosého nebo příčného
válcování na dvou nebo tříválcích - děrování a válcování
polotovarů,
-
zpracování těchto polotovarů na trubky poutnickým nebo
klasickým způsobem válcování děrovaného polotovaru (redukce
průměru, prodloužení), kalibrace rozměrů.
Rozeznáváme několik technologických způsobů výroby bezešvých trubek:
Nejčastěji se děruje polotovar kosým válcováním (základ Mannesmannova a
Stiefelova způsobu výroby), při kterém dochází v důsledku
jednosměrného stlačení materiálu (vznik velkých tahových napětí)
k rozrušení materiálu ve středu polotovaru a k posunu částic
materiálu ze středu průřezu ven směrem k obvodu, který se
zvětšuje a tím dochází k tvorbě vnitřních trhlin, tedy
k děrování. Díra má nepravidelný tvar a proto se kalibruje trnem
kvůli hladkému povrchu. Úhel natočení válců není velký, bývá
kolem 3 až 7o. Úhel sklonu válců se během tváření
nemění, ale mění se pouze vzdálenost mezi válci, aby se dosáhlo
potřebné deformace, potřebného smáčknutí. Děrovací trny mají
jednoduchý tvar. Stupeň deformace není velký, poměr tloušťky
stěny dutého předvalku a hotové trubky bývá kolem 5,5 až 7,3.
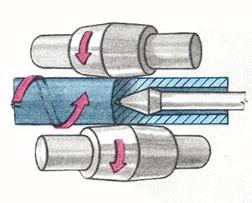
Princip kosého válcování trubek – Mannesmanův způsob, Stiefelův způsob(vpravo)
K další redukci průměrů a ke zvětšení
délky se používá tzv. poutnická stolice. Válcuje se opět na trnu
(tyči), jehož průměr odpovídá průměru trubky a délka je větší,
než je délka vyválcovaného děrovaného polotovaru, přičemž
dochází k redukci vnějšího i vnitřního průměru děrovaného
polotovaru. Při válcování se vývalek osově posouvá, částečný
návrat je proveden nuceným pohybem. Tím dochází k válcování po
přítržích nebo krocích odkud má též stolice název. Na povrchu
vývalku válcovaných na poutnické stolici jsou znát nepatrné
povrchové vlnky ve vzdálenosti válcovacího kroku. Počet otáček
je závislý na průměru trubky a platí, že pro menší průměry je
větší (od 50 do 150 min-1). Za dobu jedné otáčky se
materiál posune do záběru v rozsahu zhruba 10 až 35 mm a
velikost posuvu závisí na velikosti a tloušťce trubky.
Vlastní výrobní a technologický proces je rozdělen do tří hlavních částí (i když celkový výrobní
proces má mnohem více operací) a to na:
- výrobu dutého polotovaru
- válcování dutého předvalku na hotovou trubku
- a poslední operací je kalibrace a chlazení
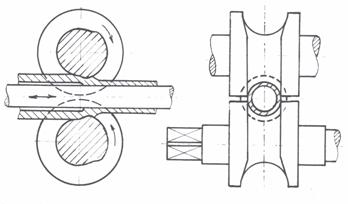
Schéma válcování na poutnické
stolici
Spojité válcování trubek je výhodné z hlediska vysokých rychlostí válcování,
z hlediska jednoduchého výrobního postupu, možnosti válcovat
trubky o malé tloušťce stěn (2 mm) a konečná jakost povrchu je
velmi dobrá. Nevýhodou je potřeba velkých zásob trnů a válců a
můžeme válcovat pouze trubky malých rozměrů (do 150 mm průměru).
Linka se skládá z ohřevu, děrovacího dvouválce s poutnickou
stolicí nebo tříválce s vlastní vícestojanovou válcovací
stolicí, se stolicí pro vytahování trnů a z ochlazení.
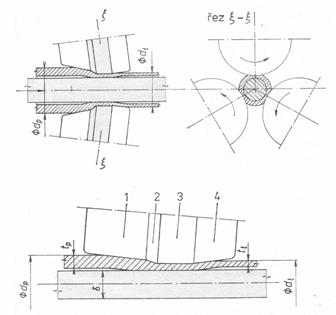 Tříválcová stolice s detailem
tvaru válce
Válcování na tratích s tříválcovou stolicí
(Asselův způsob), kdy kuželové válce jsou vzájemně mimoběžné a
šikmo umístěné pod úhlem 10 až 15o, umožňuje měnit
stupeň příčné deformace a to změnou úhlu sklonu válců. Kužele
plní následující funkce: kužel 1 je záběrový nebo také zaváděcí
kužel, kužel 2 je válcovací kužel, který provádí podstatnou část
deformace, kužel 3 je rozválcovací, kalibrační kužel, který
vyhlazuje povrch a kalibruje vnější průměr, kužel 4 je výstupní
kužel.
Tratě s příčnými válci, kotouči – Diescherův způsob válcování trubek
se používají pro trubky menších rozměrů - 50 až 150 mm, s malými
tloušťkami stěn – kolem 3 mm s velmi dobrou jakostí povrchu.
Válcovací stolice má dva pracovní mimoběžné válce, které válcují
podle kosého principu. Mezi tyto válce jsou ve svislé rovině
uloženy dva kotouče, které se otáčejí napříč a napomáhají tak
tváření.
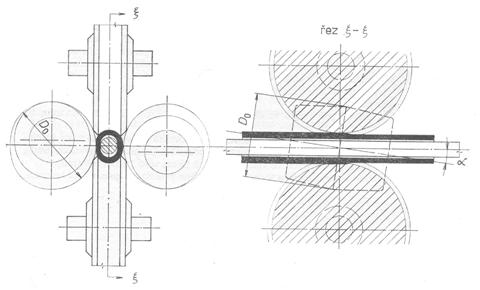 Válcovací trať s příčnými válci
Výroba trubek děrováním na tlačné válcovací stolici je nový způsob
výroby trubek (označovaný jako PPM), kdy však musí následovat
buď poutnická stolice nebo Stiefelův způsob kalibrace. Výhodou
je možnost děrovat čtvercové polotovary.
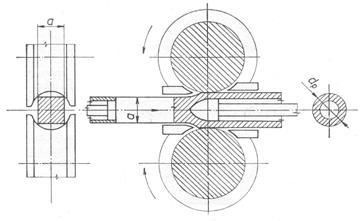 Schéma výroby trubek děrováním
2.3.5. Válcování kotoučů a
kroužků
Kroužky a kotouče se rovněž vyrábějí válcováním na speciálních válcovacích
jednoúčelových strojích. To se v podstatě provádí dvěma
dvojicemi kruhových nebo kuželových válců, které upravují
protilehlé plochy průřezů. Během válcování se vzdálenost trnů
nuceným způsobem mění, profil kroužku se zmenšuje a průměr se
zvětšuje. Tvar válců je profilován dle požadavků na konečný tvar
výrobku. Dochází zde ke zhutňování materiálu bez porušení
vláknité textury.
2.4.
Speciální způsoby
válcování
2.4.1. Příčné klínové
válcování
Válcováním lze vyrábět též speciální strojní a hutní výrobky. Například
tzv. příčné klínové válcování (Holubova metoda). Používá se pro
výrobu předkovků, vývalků, ale i pro výrobu polotovarů rotačních
tvarů v konečné kvalitě. Polotovar je a nebo může být indukčně
ohřát a posunut do tvářecího stroje. Maximální průměr vývalku je
40 mm, délka 320 mm, výkon je 10 až 20 kusů za minutu. Tímto
způsobem se vyrábějí např. osy šlapek jízdních kol.
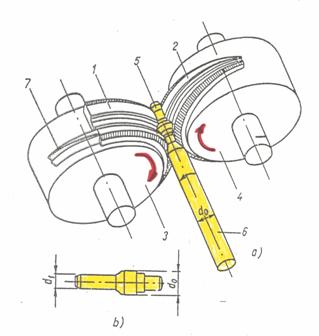 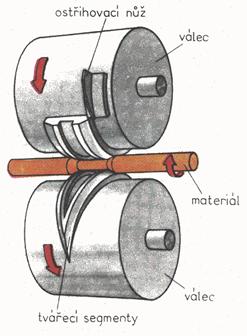
Příčné klínové válcování (a – princip, b – vývalek)
2.4.2. Válcování kuličkových
polotovarů
Válcování kuličkových předvalků kosým válcováním válci se šroubovicovým
profilem z tyče. Kuličkové předvalky jsou určeny pro další
výrobu kuliček pro kuličková ložiska. Vysoká přesnost kuliček je
dána tvářením za studena, dochází zde ke zpevnění materiálu a
k jeho pěchování. V poslední profilové části válců dojde
k ustřižení kuličky od zbytku tyče.
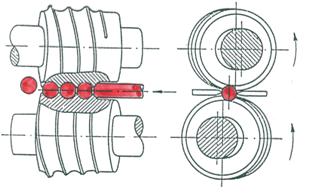 Válcování kuličkových polotovarů
2.4.3. Válcování závitů
Zvláštním případem válcování je
výroba tvářených závitů. Závity lze válcovat jedním, dvěma
nebo třemi kotouči opatřenými negativem reliéfu požadovaného
závitu. Nástroj se při odvalování postupně zatlačuje do
polotovaru, přičemž postupuje i osově podle stoupání závitu.
Zatlačování je vyvozeno hydraulikou. Tvářené závity mají vyšší
únosnost, nežli závity vyráběné obráběním, nedochází k porušení
vláknité textury a při tváření za studena dochází ke zlepšení
mechanických vlastností v důsledku zpevňování.
Následující speciální způsoby technologie
válcování jsou metody, které se dají zařadit i mezi technologii
kování. První z nich je válcování výkovků (vývalků), kdy
se požadovaný tvar získá tvářením na kovacích válcích, na
kterých je několik tvarových segmentů. Druhou metodou je
metoda Slick-Mill (tváření kývavým pohybem), která se
používá pro výrobu rotačních výkovků.
2.4.4. Válcování na kovacích
válcích
Při válcování na
kovacích válcích se dosahuje velkého stupně deformace tvářeného
materiálu a probíhá nejčastěji na několik průchodů. Výroba
předkovků na kovacích válcích je 5krát rychlejší, než na
bucharech. Spojením kovacích válců se svislými nebo vodorovnými
kovacími lisy představuje velmi výkonnou kovací jednotku.
2.4.5. Válcování metodou
Slick-Mill
Metoda Slick-Mill je v podstatě založena na kombinaci hydraulického lisu
s válcováním. Spodní rotační zápustka je vyplňována tvářeným
kovem za působení tlaku horního rotujícího disku. Vývalek
rotačního tvaru obvykle velkého průměru) je zhotoven na tomto
zařízení za 60 až 80 s.>
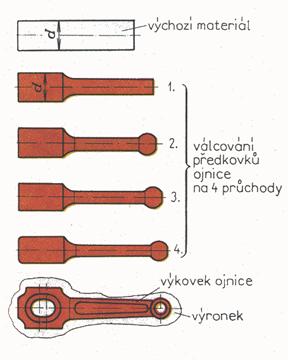 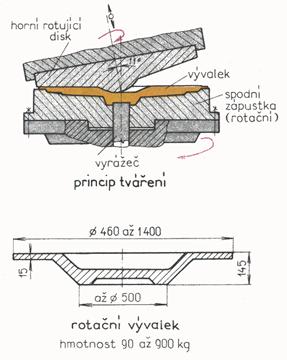
Vlevo - Princip a postup kování na kovacích válcích Vpravo - Tváření pomocí metody Slick-Mill
.: Jdi na začátek stránky :. |