- Technologie tváření kovů
1.1. Rozdělení technologií pro zpracování kovů
1.1.1. Rozdělení tvářecích procesů podle teploty
1.1.2. Rozdělení tvářecích procesů podle tepelného efektu
1.1.3. Rozdělení tvářecích procesů podle stupně deformace
1.1.4. Rozdělení tvářecích procesů podle působení vnějších sil
1.2. Struktura kovů a poruchy krystalové mřížky
1.3. Zotavení a rekrystalizace
1.4. Plastická deformace kovů
1.5. Schémata napětí a deformací
1.5.1. Stav napjatosti
1.5.2. Stav deformace
1.5.3. Parametry tvářecích strojů
1.6. Materiál a jeho kontrola
1.7. Druhy polotovarů
1.8. Dělení materiálu
1.8.1. Dělení řezáním
1.8.2. Dělení upichováním
1.8.3. Dělení lámáním
1.8.4. Dělení sekáním
1.8.5. Dělení stříháním
1.9. Ohřev materiálu
1.9.1. Zařízení pro ohřev materiálu
1. Technologie tváření kovů
Tvářením kovů rozumíme technologický (výrobní) proces, při kterém dochází k požadované změně tvaru výrobku nebo polotovaru, příp. vlastností, v důsledku působení vnějších sil bez odběru třísek. Podstatou tváření je vznik plastických deformací, ke kterým dojde v okamžiku dosažení napětí na mezi kluzu pro daný materiál. Tento děj je provázen fyzikálními změnami a změnami struktury materiálu, což ovlivňuje mechanické vlastnosti materiálu.
Výhodami tváření jsou vysoká produktivita práce, vysoké využití materiálu a velmi dobrá rozměrová přesnost tvářených výrobků. Nevýhodou je vysoká cena strojů a nástrojů a omezení rozměry konečného výrobku.
1.1.
Rozdělení technologií pro
zpracování kovů
Technologické tvářecí procesy je možné rozdělit podle:
- teploty
- tepelného efektu
- stupně dosažené deformace
- podle působení vnějších sil
1.1.1. Rozdělení tvářecích procesů podle
teploty
Při změně teploty se mění deformační odpor materiálu (oceli)
proti tváření. Se zvyšující se teplotou se zlepšují plastické
vlastnosti kovů a jejich slitin.
Rozdělení tvářecích procesů podle teploty
Rozdělení tvářecích procesů podle teploty je vlastně rozdělení
podle vztahu teploty tvářeného materiálu k teplotě
rekrystalizace (přibližně 0,4 teploty tání kovu - oK).
Rekrystalizační teplota je teplota, při které dochází
k regeneraci deformovaných zrn vzniklých tvářením za studena
beze změny krystalové mřížky. Potom tedy rozdělení tvářecích
technologií podle teploty je na:
-
tváření za studena
(tváření pod rekrystalizační teplotou, kdy teplota tváření
je pod hodnotou 30 % teploty tání tvářeného materiálu), kdy
dochází ke zpevňování materiálu, které se zachová a
k nárůstu odporu proti dalšímu tváření (nakonec dojde
k vyčerpání plastičnosti materiálu), zrna se deformují ve
směru tváření, vytváří se
textura, dochází k anizotropii mechanických
vlastností. Zpevněním se zvyšují mechanické hodnoty (mez
pevnosti a mez kluzu) a klesá tažnost. Zahřátím kovu je
možné obnovit deformační schopnost, kov získává opět
schopnost být plasticky tvářen. Výhodou je vysoká přesnost
rozměrů, kvalitní povrch (nenastává okujení) a zlepšování
vlastností zpevněním. Nevýhodou je nutnost používat velké
tvářecí síly, nerovnoměrné zpevňování a omezená tvárnost
materiálu.
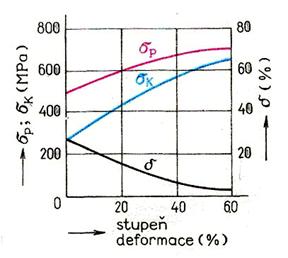
Změna mechanických vlastností v závislosti na stupni deformace
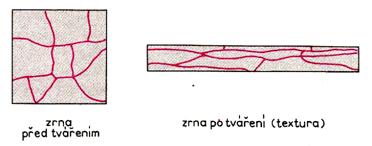
Změna tvaru zrn v důsledku tváření
-
tváření za tepla
probíhá nad
rekrystalizační teplotou, kdy rychlost rekrystalizace je
tak vysoká, že
zpevnění způsobené tvářením mizí již v průběhu tváření a
nebo bezprostředně po něm. Teplota tváření je nad hodnotou
70 % teploty tání daného materiálu. Materiál se nezpevňuje a
k tváření stačí síly až desetkrát menší, než u tváření za
studena. Může a nemusí vznikat textura, ale povrch je
nekvalitní vlivem okujení, navíc
hrubne zrno, což je problematické u dalších
technologických operací z hlediska kvality. Proces je
poměrně zdlouhavý a nákladný, na druhé straně však dochází
k odstranění trhlin, bublin, atd. Dalším vlivem tváření za
tepla je vznik
vláknité struktury z hrubé dendritické struktury ingotu,
která „kopíruje“ tvar výkovku. Vláknitou strukturu je
nemožné změnit tepelným zpracováním, ani tvářením. Vláknitá
struktura ovlivňuje mechanické vlastnosti a anizotropii.
Vzniká v důsledku nečistot, obsažených v povrchových
vrstvách krystalů.
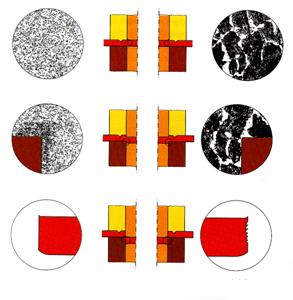
Vliv velikosti zrna na kvalitu střihu
-
tváření za poloohřevu představuje kompromis mezi tvářením za studena a za tepla.
Důvodem je zlepšení přetvárných vlastností oproti tváření za
studena, snížení přetvárných odporů, dosažení zlepšení
mechanických a fyzikálních vlastností, přesnosti a jakosti
povrchu. Horní teploty jsou omezeny oxidací povrchu.
1.1.2. Rozdělení tvářecích procesů podle
tepelného efektu
Část energie, vynaložené na tváření, se mění na teplo a množství
tepla závisí na rychlosti deformace a odporu materiálu proti
deformaci. Podle toho, kam se odvede vzniklé teplo, se tvářecí
procesy dělí na:
- izotermické tváření je tváření, kdy veškeré vyvinuté teplo je odvedeno do okolí a teplota tvářeného kovu se nemění. Deformace je dostatečně pomalá.
- adiabatické tváření je proces tváření, při kterém veškeré teplo zůstane v materiálu a dojde ke zvýšení teploty kovu. Deformace je extrémně vysoká.
- polytropické tváření je způsob tváření, u kterého se část tepla odvede do okolí a část tepla zůstane v tvářeném materiálu, což je nejčastější případ.
1.1.3. Rozdělení tvářecích procesů podle
stupně deformace
Kritériem je zde stupeň deformace při určité teplotě a rychlosti
deformace bez nebezpečí vzniku trhlin na povrchu materiálu. Část
energie, vynaložené na tváření, se mění na teplo a množství tepla závisí na rychlosti deformace a odporu materiálu proti
deformaci. Podle toho se tvářecí procesy dělí na:
- procesy, kdy tlak mezi nástrojem a materiálem je malý, ke vzniku deformace jsou potřeba malé síly a povrch volného materiálu je výrazně větší, než povrch, který je ve styku s nástrojem (např. volné kování),
- procesy, kdy tlak mezi nástrojem a materiálem je velký, ke vzniku deformace jsou potřeba velké síly a povrch volného materiálu je přibližně stejný jako povrch, který je ve styku s nástrojem (např. zápustkové kování),
- procesy, kdy tlak mezi nástrojem a materiálem je velmi vysoký, ke vzniku deformace jsou potřeba značně velké síly a povrch volného materiálu je menší, než povrch, který je ve styku s nástrojem (např. protlačování).
1.1.4. Rozdělení tvářecích procesů podle
působení vnějších sil
Z tohoto hlediska se tváření kovů dělí na:
- tváření objemové, při kterém deformace nastává ve směru všech tří os souřadného systému a patří sem válcování, kování, protlačování, tažení drátů.
- tváření plošné, při kterém převládají deformace ve dvou směrech. Patří sem tažení, ohýbání, stříhání, apod.
1.2.
Struktura kovů a
poruchy krystalové mřížky
Plastická
deformace je ve své podstatě pohyb jednotlivých částeček kovů
vůči sobě a mechanismus vzniku plastické deformace je možné
vysvětlit na základě pohybu a vzniku mřížkových poruch. Stavba
krystalové mřížky není v reálných kovech dokonalá. Podle
velikosti a tvaru krystalografické neuspořádanosti atomů
rozeznáváme následující mřížkové poruchy:
- bodové (vakance, interstice, substituce)
- čárové (hranové, šroubové a kombinované),
- plošné (vrstevné vady, hranice zrn, subzrn, dvojčatní),
- prostorové (hranice krystalů, vměstky, amorfní částice, apod.).
Z hlediska teorie plastických přetvoření
mají největší vliv a význam čárové poruchy – dislokace.
Dislokace jsou poruchy, které se projevují vysunutím atomů
z pravidelných poloh krystalové mřížky a které se mohou
pohybovat, mohou vznikat a zanikat. Dislokace jsou buď hranové
nebo šroubové, resp. kombinované. Hustota dislokací
r
je celková délka dislokačních čar L, obsažených
v jednotce objemu V, tedy
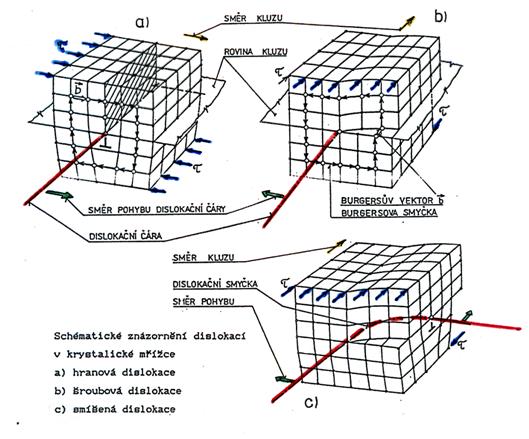
Rozdělení dislokací
Hustota dislokací ovlivňuje pevnost kovu. Tvářením se počet dislokací
zvyšuje a tím i odpor proti deformaci, tím dochází ke zpevnění a
ke zvýšení pevnosti.
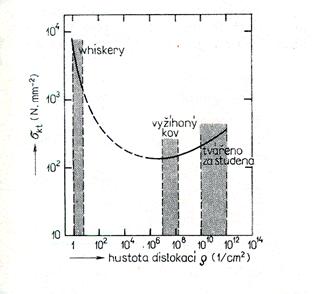
Vliv hustoty dislokací
Dislokace během tváření mohou vznikat následujícími procesy:
- krystalizací kovů, kdy vzniká růstová spirála a dochází ke vzniku šroubových dislokací,
- růstem zrn do bloků mohou vznikat hranové a šroubové dislokace,
- změnou shluku vakancí na dislokace,
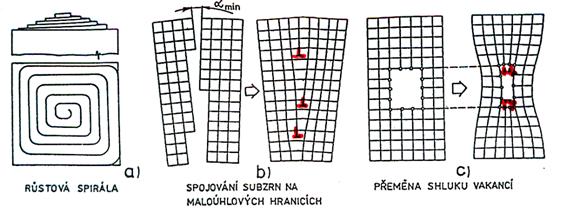
Mechanismy vzniku dislokací
-
Frank-Readovým zdrojem dislokací za působení smykového
namáhání, kdy dochází k rozdělení dislokační čáry na dvě
dislokace,
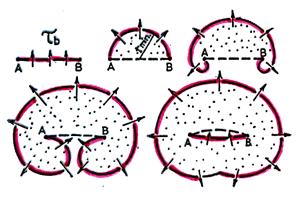
Frank-Readův zdroj dislokací
- v oblasti vysokých napětí v tom případě, kdy vznikají ostré trhliny.
- skluzem, kdy se dislokace pohybuje v rovině
skluzu za působení napětí. Rychlost pohybu závisí na typu
krystalové mřížky a na množství poruch, neboť kritické skluzové
napětí, tj. napětí potřebné k vyvolaní pohybu dislokace je tím
vyšší, čím více poruch brání pohybu (hranice zrn, počet
dislokací a jejich protínání, atd.),
- difůzí, nebo také „šplháním“ dislokací, což je naopak pomalý pohyb spojený s vakancemi a
intersticiálními atomy, závislý na teplotě a napětí.
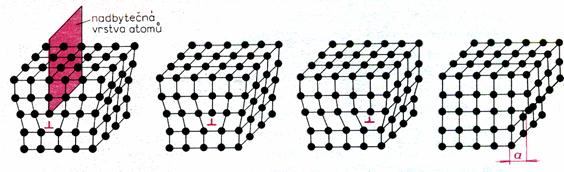
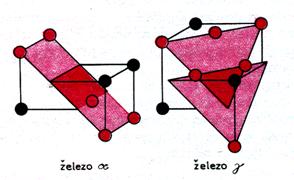
Posuv vrstvy atomů vyvolaný pohybem hranové dislokace (nahoře) a kluzné roviny v železe a a g (dole)
1.3.
Zotavení a rekrystalizace
Po tváření za studena je kov strukturně nestálý,
stav zrn je nestabilní. Při působení vyšší teploty bude docházet
ke zvyšování pohyblivosti atomů, ke snižování energie
deformovaného kovu. Mohou nastat dva děje, zotavení (tj.
zánik mřížkových deformací a napětí) a rekrystalizace
(vznik zárodků a růst nových zrn). Zotavení a rekrystalizace je
závislá na teplotě a na předchozím stupni tváření.
Rekrystalizace může nastat jen při dosažení teploty
rekrystalizace, která je empiricky stanovená na 35 až 40 %
teploty tání daného kovu. Během rekrystalizace se netvoří
struktura nová fáze, nýbrž nová struktura stejné fáze za
tvářením deformovanou původní strukturu. Zotavením dochází k
uspořádání dislokací a ke snižování deformační energie, pevnost
a mez kluzu klesá a tažnost stoupá (prakticky klesá vnitřní
pnutí). Rychlost zotavení je závislá na teplotě a na čase. Během
rekrystalizace vznikají
zárodky nových krystalů (primární rekrystalizace),
které rostou na úkor původních deformovaných zrn a zpevnění
zaniká (sekundární rekrystalizace).
Navíc dochází ke změně velikosti zrna, která závisí na
předchozím stupni deformace. Při větším stupni deformace
dostáváme jemnější zrno a naopak. Při tváření kovů obecně
nastávají další dva děje, a to
zpevnění a odpevnění.
Výsledný efekt závisí na vzájemné rychlosti obou dějů.
Při tváření za studena odpevnění prakticky neprobíhá, proto se materiál zpevňuje zatímco při tváření za
tepla probíhá odpevnění okamžitě a materiál se nezpevňuje (dynamická rekrystalizace).
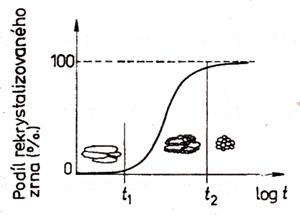
Velikost zrna v závislosti na čase
Pokud by mělo dojít k odpevnění materiálu po tváření za studena, musela by být provedena rekrystalizace podle rekrystalizačního
diagramu tvářeného materiálu mluvíme o rekrystalizačním žíhání. Důležitý z hlediska tváření je v rekrystalizačním diagramu
vztah mezi tvářecí teplotou, stupněm deformace a velikostí zrna.
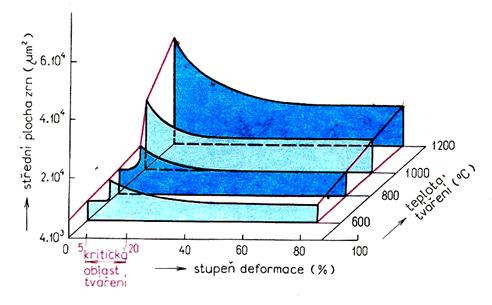
Rekrystalizační diagram
1.4.
Plastická deformace kovů
Změna tvaru mřížky, která se navenek projevuje změnou tvaru bez vzniku
trhlin, nazýváme deformací. Podle fyzikální povahy je
možné deformaci rozdělit na
pružnou (elastickou) deformaci, kdy se materiál bude
vracet do původního tvaru, pokud přestane působit síla, která
způsobila pružnou deformaci a na plastickou deformaci,
kdy změna tvaru zůstává zachovaná i po odstranění příčiny
deformace, pokud napětí vzroste nad určitou hodnotu (mez kluzu).
Z hlediska tváření kovů má největší význam plastická deformace,
i když vliv elastické deformace má vliv na konečný tvar
výrobku. Při vzniku trhlin a následné destrukci tělesa mluvíme o
porušení.
Velikost
deformace závisí na teplotě, rychlosti zatěžování, napjatosti,
chemickém složení, zpevnění a tření, atd. Tyto všechny vlivy se
navenek projevují odporem kovu ke změně tvaru – deformačním
odporem.
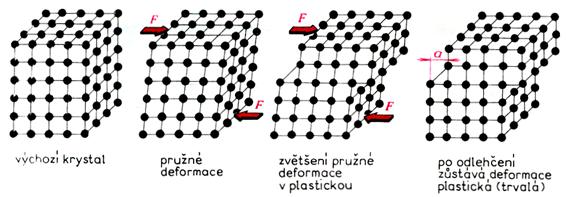
Schéma pružné (elastické) a trvalé (plastické) deformace
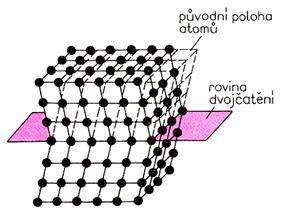
Schéma zrna polykrystalického kovu – vlevo (a – zrno deformované skluzem, c – zrno deformované dvojčatěním) a schéma dvojčatění (nahoře)
Rozeznáváme dva základní mechanismy plastické deformace a to skluzem
(amorfní, translační, složitý skluz) a dvojčatěním. Vždy
se rozvíjí ten mechanismus plastické deformace, který při daných
podmínkách vyžaduje nejmenší napětí. U skluzu se nadbytečná
vrstva atomů pohybuje ve směru působícího napětí až vystoupí na
povrch, pokud se nezachytí o překážky uvnitř krystalu, apod.
Atomy se tedy posunují proti sobě postupně, ne současně.
Jestliže se pohyb dislokací zastaví, je potřeba k další
plastické deformaci napětí zvýšit. Při tváření za studena kov
klade stále větší odpor, zpevňuje se. Přesuny atomů váznou,
plasticita (tvárnost) kovu se vyčerpává a může dojít k porušení
materiálu. U dvojčatění se přeskupuje část krystalu tak, že
se celá mřížka nejdříve natočí do příznivé polohy pro skluz a
následně se část natočeného krystalu skluzem deformuje.
1.5. Schémata napětí a deformací
Pro analýzu jednotlivých tvářecích procesů mají
veliký význam schémata napětí a deformací, která umožňují udělat
si grafickou představu o přítomnosti a smyslu hlavních napětí a
hlavních deformací. Pomocí těchto schémat je možné klasifikovat
jednotlivé technologické procesy tváření kovů.
1.5.1.
Stav napjatosti
Stav napjatosti poskytuje názornou představu o přítomnosti,
velikosti a smyslu hlavních napětí v tvářeném tělese. Tvářený
materiál se nahrazuje krychlí, z jejíchž stěn vycházejí vektory,
zobrazující směry hlavních napětí. Celkem lze zapsat devět
schémat hlavních napětí, kdy jen některé mají praktický význam
v procesu tváření kovů. Stav napjatosti má významný vliv na
tvářitelnost a deformační odpor. Tvářitelnost je tím vyšší, čím
menší úlohu hrají tahová napětí. Deformační odpor bude největší
u stejnorodého stavu napjatosti a naopak.
1.5.2. Stav deformace
Deformaci a její rozdělení jsme si již popsali
dříve. Na druhé straně rozeznáváme jak deformaci poměrnou, tak i
skutečnou. Poměrné deformace
e
ve směru hlavních napětí jsou deformace vztažené ke změně
rozměru v daném směru, podělené daným rozměrem. Jsou zatížené
poměrně vysokou chybou a proto se přistoupilo k výpočtu
skutečných deformací
j
pomocí diferenciálního způsobu příslušných deformací. Vlastní
stav deformace je popsán pouze třemi
schématy hlavních deformací, kdy se vychází ze
zákona stálosti objemu. Zákon stálosti objemu říká, že objem
tělesa před tváření (deformací) Vo se
rovná objemu tělesa po tváření V (Vo
= V). nepatrné změny objemu se zanedbávají. Potom platí,
že součet deformací v jednotlivých hlavních směrech je roven
nule:
j1
+ j2
+ j3
= 0
1.5.3. Parametry tvářecích strojů
Kromě schémat napětí a deformací rozeznáváme i
rychlost deformace (poměrnou rychlost tváření), která není
shodná s rychlostí tvářecího nástroje. Jedná se o rychlost,
s jakou se k sobě přibližují dva průřezy kovu, vzdáleného o
jednotku délky. Přetvárný (deformační) odpor je napětí v MPa,
potřebné k tomu, aby se dosáhlo v tvářeném materiálu trvalých
deformací. Přetvárný odpor závisí na teplotě, na deformační
rychlosti, tření, mezi kluzu, rozměrech tělesa. Přetvárná
pevnost (tvářecí napětí) je napětí, kterým se dosáhne
plastické deformace bez pasivních odporů (např. tření). Závisí
na druhu materiálu (mez kluzu za dané teploty a velikosti
deformace, někdy i napjatosti), teplotě, deformační rychlosti a
stupni deformace. Přetvárná síla je síla, kterou musí
vyvinout tvářecí stroj k dosažení trvalé deformace materiálu. Je
to součin přetvárného odporu a plochy styku materiálu
s nástrojem. Působí-li přetvárná síla na určité dráze, dostaneme
přetvárnou (deformační) práci. Podle vypočtených hodnot
přetvárné síly a práce se určují potřebné parametry tvářecích
strojů
1.6.
Materiál a jeho kontrola
Volba vhodného materiálu pro tváření
je závislá na volbě tvářecí technologie, která ovlivňuje nejenom
produktivitu výroby, ale i kvalitu a přesnost výroby.
Nejčastějším materiálem pro tváření je ocel, neželezné kovy a
v poslední době i kompozitní materiály. Vzhledem k tomu, že tato
literatura je věnována tvářecím technologiím, není možné zde
probírat a vyjmenovávat jednotlivé materiály – viz. předmět
Nauka o materiálu.
O každém materiálu je nutné znát jeho chemické
složení, mechanické vlastnosti, teplotu a způsob ohřevu.
Tvářitelnost se kvalifikuje ve čtyřech stupních jako zaručená,
velmi dobrá, dobrá a omezená tvářitelnost.
Kontrola materiálu
se provádí vždy na vstupu do výrobního procesu a obyčejně se
kontroluje množství a rozměry, chemické složení (důležité pro
tepelné zpracování), mechanické vlastnosti (kontrolují se proto,
aby se zjistili vlastnosti materiálu před tvářením, neboť hlavně
tvářením za studena dojde k výrazné změně mechanických hodnot) a
technologické vlastnosti (posouzení vhodnosti a vlastností
daného materiálu pro zvolenou technologii - technologické
zkoušky tvářitelnosti.
1.7. Druhy
polotovarů
Jako polotovary pro tvářecí technologie se používají
buď ingoty, vývalky nebo plechy.
Ingoty se odlévají v rozsahu hmotnosti od 0,5 do 300 t.
Ve strojírenských podnicích se zpracovávají ingoty volným
kováním o hmotnosti od 10 do 15 t. Těžší se zpracovávají přímo
v hutích. Vývalky jsou konečné hutnické výrobky z těžkých
ingotů, které jsou válcované za tepla. Používají se jako
polotovary pro volné a zápustkové kování, protlačování. Obvykle
se používají v přírodním stavu, neboť tepelně zpracovaný
materiál v důsledku tváření za tepla stejně změní svoji
strukturu. Tepelně zpracované vývalky se používají pro tváření
za studena. Plechy se používají hlavně u plošných
technologií tváření (tažení, stříhání, ohýbání). Zvláštní místo
zaujímají hlubokotažné plechy. Ocelové plechy se dodávají buď
v tabulích nebo ve svitcích. Do tloušťky 4 mm jsou plechy
označovány jako tenké, nad touto hodnotou jako plechy tlusté.
1.8.
Dělení materiálu
V technologii tváření se používají různé
polotovary, např. tyčový materiál, svitky, tabule, apod., které
se dělí na přesnou hmotnost, resp. na požadovaný rozměr. Dělení
materiálu má vliv i na kvalitu výrobku, a to kvalitou plochy
v místě dělení. Z hlediska dělení materiálu můžeme používat
následující způsoby: řezání, upichování, lámání, sekání,
stříhání.
1.8.1. Dělení řezáním
Materiál dělit řezáním můžeme na
okružních, rámových nebo pásových pilách. Při řezání se část
materiálu ztrácí ve formě třísek (nejde o tváření) a hmotnost
odpadu závisí na šířce pily. Řezat materiál lze jen do určité
tvrdosti, jinak se musí předem vyžíhat. Řezáním lze zajistit
hladký řez a přesnou hmotnost řezaného polotovaru a kolmost
řezu, což je u některých technologií dělení problematické.
1.8.2. Dělení upichováním
Používá se poměrně zřídka, neboť je to
drahý způsob dělení na upichovacích automatech nebo
univerzálních soustruzích. Ztráty materiály jsou poměrně značné,
na druhé straně lze získat velmi hladké plochy. Používá se pro
přesné rozměry polotovarů (např. pro protlačování), nedochází ke
stlačení.
1.8.3. Dělení lámáním
K lámání se používají speciální lámací
stroje. Před lámáním se polotovar nahřívá kyslíkoacetylénovým
plamene v místě, kde dojde k ulomení. Tím se vytvoří vrub a
zmenší se plocha průřezu. Lámáním nelze dělit měkké materiály,
které se pouze ohnou. Mez pevnosti musí být vyšší, jak 600 MPa.
Nevýhodou je i nízká kvalita lomové plochy, možnost vzniku
trhlin a jejich šíření do materiálu. Používá se hlavně pro
přípravu polotovarů pro tváření za tepla.
1.8.4. Dělení sekáním
Používá se velmi málo, a to hlavně u
volného kování. Nástrojem je sekáč, který můžeme používat buď
ručně nebo pomocí stroje, např. bucharu. Nevýhodou je nízká
produktivita, nerovná plocha se záseky, vysoká fyzická námaha.
Nejčastěji se používá jako doplňková operace při odsekávání
přebytečného materiálu na konci výkovku.
1.8.5. Dělení stříháním
Stříhání je nejrozšířenější operace při
dělení materiálu, ale i v technologii tváření. Používá se na:
- přípravu polotovarů, např. stříhání tabulí plechu, dělení svitků,
stříhání profilů, stříhání vývalků, atd.,
- vystřihování součástek z plechů pro přímé použití nebo jako polotovarů pro
další technologie, jako ohýbání, tažení, protlačování, apod.,
- na dokončovací nebo pomocné operace.
Dělit materiál stříháním můžeme za tepla i za studena. Za studena se
stříhají pouze měkké oceli do pevnosti zhruba 400 MPa a nebo
plechy. Tvrdé materiály se ohřívají na teplotu asi 700 oC.
Dělit materiál stříháním můžeme rovnoběžnými noži, skloněnými
noži a nebo
kotoučovými noži, resp. noži na profilový materiál –podrobně
v kap. 6. Dělit materiál můžeme jak v podélném směru, tak i
v příčném směru.
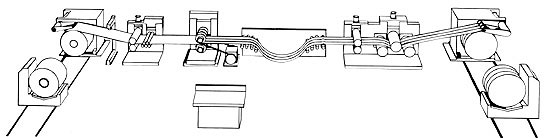

Schéma linek na podélné (nahoře) a příčné dělení stříháním (dole)
1.9.
Ohřev materiálu
Pro dodržení technologických podmínek zpracování je velmi
důležitá správná volba a dosažení tvářecích teplot. Oblast
tvářecích teplot uhlíkových ocelí je ukázána na obrázku. Odlitý
materiál (ingot) se tváří při teplotách přibližně o 100 až 150
oC vyšších, než materiál již jednou tvářený. Nižší
teploty jsou i pro volné kování, než pro zápustkové kování.
Teplota během tváření se snižuje k dolní hranici tvářecích
teplot a pokud ještě není práce skončena, je nutný nový
přiměřený ohřev.
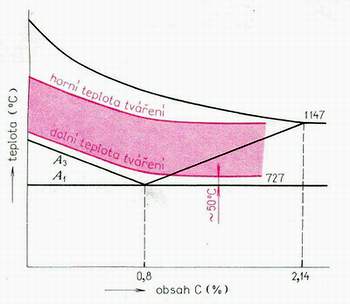
Oblast tvářecích teplot
Je nutné si však uvědomit, že sice při
vyšších teplotách jsou menší odpory proti deformaci, na druhé
straně hrubne struktura, klesá houževnatost, roste tvorba okují
a oduhličení. Ohřev musí být proveden tak, aby bylo zajištěno
rovnoměrné prohřátí v celém průřezu co nejrychleji, aby ztráty
opalem byly co nejmenší. Oceli s vyšším obsahem uhlíku a
legované oceli se zpočátku musí ohřívat velmi pomalu, aby
nedocházelo k praskání.
Doba ohřevu t
na teplotu tváření závisí na tepelné bilanci pece, tepelné
vodivosti materiálu a
jeho rozložení v peci:
t =
a
. k . D .

kde t – čas potřebný k ohřevu z 0 oC na 1200
oC [h],
a - součinitel závisící na průřezu materiálu a na jeho rozložení
v peci,
k – součinitel vlivu chemického složení materiálu (u
uhlíkových ocelí je roven 10, u legovaných 10 až 20),
D – průměr nebo délka strany průřezu ohřívaného materiálu [m].
Pro ohřev materiálu jsou také používány diagramy a nebo lze dobu ohřevu
určit z teplotního spádu. Při ohřevu studeného materiálu se
připouští teplotní spád v rozmezí 1,2 až 3,4 oC na 10
mm průměru, při ohřevu teplého materiálu 6 až 10 oC
na 10 mm průměru.
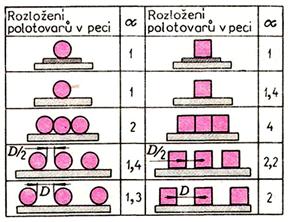
Závislost součinitele a na způsobu rozložení materiálu v peci
Při ohřevu mohou nastat nežádoucí procesy ovlivnění povrchu oceli
prostředím – oxidace, oduhličování. Vznik okují
během oxidace povrchu nepříznivě působí na tvářecí nástroje,
jakost povrchu a rozměrovou přesnost, navíc vede ke ztrátě
materiálu. Oxidace (okujení, tvorba oxidu železnatého) nastává
při teplotách vyšších, jak 600 oC a při teplotách nad
900 oC je rychlost tvorby okují již vysoká. Stupeň
oxidace závisí na době ohřevu, teplotě ohřevu, složení pecní
atmosféry, druhu materiálu. Pokud bychom chtěli mít bezokujový
ohřev, museli bychom materiál ohřívat v ochranné atmosféře.
Oduhličení vede k ochuzování povrchu materiálu o uhlík a závisí
na složení pecní atmosféry, na době a teplotě ohřevu a na obsahu
uhlíku v oceli.
1.9.1. Zařízení pro ohřev
materiálu
Pro ohřev
ingotů pro technologii válcování jsou nejvhodnější
hlubinné pece, kdy ingoty se ohřívají pomocí hořáků,
umístěných buď v čelní stěně, nebo ve spodku pece. Ohřev je
potom shora nebo středem.
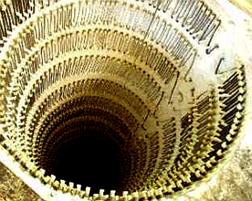
Ukázka hlubinné pece
Pro ohřev ingotů pro kovárny se používají
pece komorové a
pece narážecí. Komorové pece mají výkonné hořáky
umístěny buď v bočních stěnách a nebo v klenbě a pracují
s cirkulací spalin. Narážecí pece jsou průchozí pece s dveřním
otvorem a strkacím zařízením. Pec má pásmo předehřívací,
ohřívací a vyrovnávací. Spaliny jsou odváděny proti pohybu
polotovaru.
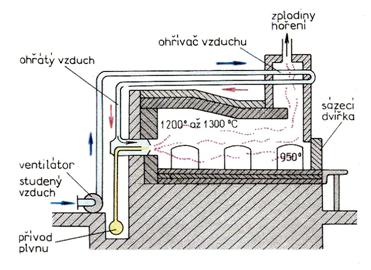
Schéma komorové pece
Pro ohřev materiálu pro
zápustkové kování se používají pece komorové,
narážecí,
karuselové, talířové a
štěrbinové. Karuselové pece jsou také průchozí pece, kdy
nístěj má tvar mezikruží a je otočná. Proces může být buď
nepřetržitý, kdy regulace se provádí změnou otáček a nebo
přetržitý, kdy se proces reguluje dobou klidu nístěje. Hořáky
jsou umístěny na vnějších stěnách. Pec má pásmo předehřívací,
ohřívací a vyrovnávací. Nevýhodou je poměrně velký zastavěný
prostor. Talířové pece mají otočnou nístěj a pouze jeden otvor
pro vkládání a vyjímání polotovarů. V celém prostoru je téměř
stejná teplota. Štěrbinové pece se používají k ohřevu konců
tyčí, trubek, tyčoviny. Konstruují se jako uzavřené nebo
průchozí.
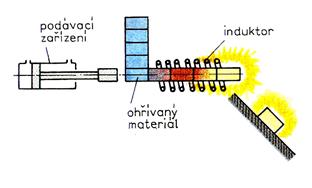
Pohled na polotovar a schéma karuselové pece (vlevo) a schéma indukčního ohřívacího zařízení (vpravo)
Kromě pecí, kdy zdrojem tepla je hoření
plynů, se používají i pece elektrické odporové a pece
indukční. Výhodou těchto pecí je jejich snadná a přesná
regulace, snadná obsluha. U indukčních pecí je polotovar uvnitř
indukční cívky, kterou prochází střídavý proud dané frekvence a
vzniklé elektrické ztráty se přeměňují v teplo.
.: Jdi na začátek stránky :.
|