- Přípravné zpracování plastů
3.1. Doprava materiálu
3.2. Sušení
3.3. Míchání a hnětení
3.3.1. Míchací stroje
3.3.2. Hnětací stroje
3.4. Granulace
3.5. Tabletování
3.6. Recyklace – mletí a drcení
3. Přípravné zpracování plastů
Plasty obecně nelze
bezprostředně zpracovávat v hotové výrobky, nejdříve musí projít
technologiemi přípravného zpracování, kdy se do plastů přidají
různé přísady, nebo se odstraňují těkavé podíly, voda, apod.
Dochází k ovlivnění fyzikální a chemické struktury plastů.
Polymerům musí být také dán tvar pro další zpracování (granulát,
prášek, kaše, atd.) Tyto technologie se potom označují jako
technologie přípravného zpracování a představují mezistupeň mezi
výrobou polymeru a vlastním zpracováním. Patří sem technologie
míchání a hnětení, granulace,
tabletování, recyklace a sušení a doprava
materiálu.
3.1. Doprava materiálu
Doprava materiálu slouží k dodání suroviny až ke
zpracovatelským zařízením. Materiál přichází z chemických závodů
již připravený pro zpracování a to buď ve formě granulí (PE, PP,
PS, POM, atd.), nebo prášku (plniva, saze, PVC, pigmenty,
apod.), balíků (kaučuky) nebo pasty, kapalin (změkčovadla,
rozpouštědla, latexy). Do výrobních závodů se pro další
zpracování plast (výchozí surovina) dodává buď v pytlích,
vážících 25 nebo 30 kg, nebo ve velkých pytlích o váze až 500 kg
a nebo v cisternách.
Vlastní manipulace s materiálem je manuálně jednoduchá a
vyndávání materiálu nemá vliv na kvalitu plastu. Velké
zpracovatelské společnosti mají k dispozici zásobníky materiálu
(sila)
o objemu kolem 20 t, které se plní přímo z železničních nebo
automobilových cisteren a z kterých je materiál pneumaticky
dodáván buď přímo ke strojům a nebo do sušáren a odtud po
provedeném sušení následně ke vstřikovacím strojům. Sila jsou
vhodná pro všechny typy plastikářských provozů a pro dopravu
všech typů a druhů plastů. Proti vniknutí cizích předmětů jsou
na vstupu sil umístěna síta a mají zařízení s automatickým
čištěním a zásobníkem pro prach. Zásobníky jsou vybaveny
zařízením pro kontrolu množství materiálu a zařízením pro
vyprazdňování zbytkového materiálu. Sila mají společný zdroj
podtlaku a společnou řídící jednotku. Kapalné systémy jsou
k dalšímu zpracování většinou dopravovány čerpadly. Přísady,
které jsou používány v menších množstvích, jsou nejčastěji
dodávány v pytlích.
Volba dopravního zařízení závisí na typu materiálu
(granule, prášek, …), množství dopravovaného materiálu,
vertikální a horizontální vzdálenosti dopravy, dalších
požadavcích na úpravu granulátu (barvení, sušení, přidávání
regenerátu, apod.).
K pneumatické dopravě se
používají buď vakuové nebo tlakové systémy a nebo jejich
kombinace. Potrubí mají většinou průměr do 100 mm a jsou buď
z oceli nebo ze slitin hliníku s možným vločkováním proti
opotřebení. Vakuový systém je možno použít do vzdálenosti 100 m,
zatímco přetlakový systém, pracující s větším tlakem vzduchu,
lze použít až do vzdálenosti 200 m. Je zde však mnohem větší
opotřebení potrubí, zvýšené tření může způsobit měknutí granulí,
příp. jejich drcení.

Schéma pneumatické dopravy
A) – podtlakový, B) – přetlakový, C) – kombinovaný systém
a – přijímací zásobník, b – cyklónový odlučovač, c – hlavní zásobník, d – dmýchadlo, e – tlumič hluku, f – čistič vzduchu,
h – dmýchadlo, i - odlučovač jemného prachu, k – rotační tlaková uzávěra
Vzrůstající spotřeba plastů vede výrobce k dopravě polymerů buď
automaticky pro každý stroj zvlášť ze
zásobníků u strojů nebo
centrálně k jednotlivým strojům do plnícího zařízení nad
násypkou. K dopravě plastu se využívá nejenom vakuových plnících
zařízení, ale i
spirálových dopravníků a sacích a přetlakových zařízení na
principu Venturiho trysky. Ve většině firem se upouští od
ručního doplňování materiálu z pytlů a přechází se
k automatickému zásobování strojů, kdy se kombinuje doprava
např. se sušením nebo barvením granulátu, resp. se kombinuje
originál polymeru s drtí, atd.
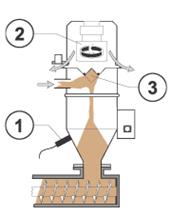
Plnící jednotka se sací jednotkou
1 – čidlo obsahu plastu, 2 – jednotka sání, 3 - filtr
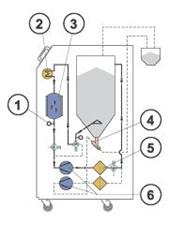
Plnící a sušící jednotka s Venturiho tryskou
1 – teplotní čidlo, 2 – topení, 3 – síto, 4 – Venturiho tryska, 5 – filtr, 6 - dmychadlo
Moderní dopravní systémy
umožňují provádět úpravy granulátu automaticky. Tak např.
nebarvený polymer lze barvit přímo na strojí v plnícím zařízení
pomocí pigmentů (masterbatche), kdy odpadá nutnost skladovat
velké množství granulátů různých barev. Pigmenty či jiné přísady
jsou dávkovány automaticky buď objemově nebo
hmotnostně do plnícího zařízení umístěného nad násypkou a po
zamíchání a promísení je upravený granulát plněn do násypky
stroje.
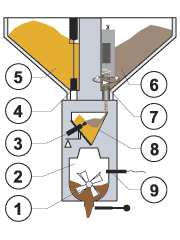
Směšovací jednotka pro barvení
1 – míchání, 2 – mísící prostor, 3 – píst, 4 – uzávěr, 5 – polymer, 6 – barvivo (masterbatch),
7 – odměřování barviva, 8 – prostor vážení, 9 - čidlo
Obdobně se do granulátu může přidávat i
recyklát, drť. Stroje přípravného zpracování většinou
nepracují samostatně, ale obvykle jsou zapojovány do výrobních
linek. Linky mohou plnit požadavky na přidávání plniv, aditiv,
barvení,
sušení, odstranění těkavých zplodin,
separaci kovů, přípravu směsí, koncentrátů,
granulaci, tabletování, apod. a vzájemnou kombinaci
jednotlivých přípravných operací.

Směšovací jednotka pro přísady
1 – přísada, 2 – polymer, 3 – mísící element, 4 – míchací kanál,
5 – násypka, 6 – míchací šnek
Polymer nemusí vždy do procesu vstupovat ve formě prášku a
vystupovat ve formě granulí, ale z polymerizačních zařízení může
vystupovat i tavenina nebo kaše, resp. roztok polymeru, pásy,
premixy, atd. Účinnost linek přípravného zpracování závisí potom
hlavně na přesnosti a reprodukovatelnosti dávkování jednotlivých
komponent. Kapalné přísady se dávkují většinou objemově, a to
většinou zubovými, membránovými nebo pístový čerpadly.
Práškové přísady se dávkují většinou hmotnostně pomocí
pásového nebo diferenciálního dávkovače nebo objemově pomocí
šnekového, spirálového nebo zubového dávkovače.
Granulát se dávkuje stejně jako prášky, tedy hmotnostně nebo
objemově. 3.2.
Sušení
Některé plasty jsou navlhavé, hydroskopické a před vlastním
zpracováním se musí sušit. To znamená zbavit
absorbované vlhkosti, neboť přítomnost vody se projevuje
zhoršováním kvality povrchu výrobků i poklesem mechanických
vlastností, zejména u plastů, u nichž voda při zvýšené teplotě
způsobuje štěpení makromolekul. Se
sušením, jako technologickou operací, se musí počítat
v případech, kdy hmota přišla v předchozí operaci do styku
s vodou, jako je tomu u suspenzí nebo emulzní polymerace anebo
při
granulaci hmoty, kdy vytlačovaný profil prochází vodní
chladicí lázní.
Průběh sušení závisí na charakteru spojení vlhkosti s materiálem. Voda
může být vázána buď přilnavostí a jedná se o vlhkost
povrchovou anebo kapilárními silami, kdy se nachází v mikrokapilárách
v celém objemu hmoty. V tomto případě je odpařování ztíženo,
protože voda v kapilárách je jakoby pod vyšším tlakem a při
sušení se musí použít vyšší teploty, než je bod varu při daném
tlaku okolí. Má-li docházet k sušení, je nutné, aby tlak páry,
který se ustaví těsně nad povrchem vlhkého materiálu, byl větší
než parciální tlak páry v okolním prostředí. Sušení může
probíhat jen do vyrovnání těchto tlaků. Materiál je tedy možno
vysušit jen do určité vlhkosti, zvané
rovnovážná vlhkost, která závisí na okolních podmínkách, a
to na teplotě okolí a na relativní vlhkosti. Jestliže se
vysušený materiál vloží do prostředí s vyšší vlhkostí, než-li
odpovídá rovnovážnému stavu, dojde naopak k navlhání.
Obsah vlhkosti v materiálu se obvykle vyjadřuje v hmotnostních
procentech, udávajících počet dílů vody ve 100 dílech vlhkého
materiálu. Tato hodnota se však pro řešení problémů sušení a pro
výpočty nehodí. Pro tyto účely se vlhkost udává v kg vody
připadající na jeden kg absolutně suché látky neboli sušiny.
Toto značení má tu výhodu, že obsah sušiny je v celém procesu
sušení konstantní. Z technologického hlediska je nejdůležitější
určení doby sušení, nutné k dosažení požadované hodnoty
vlhkosti. K tomu je nutno znát rychlost sušení.
Hodnoty obsahu vlhkosti vzduchu v závislosti na ročním období
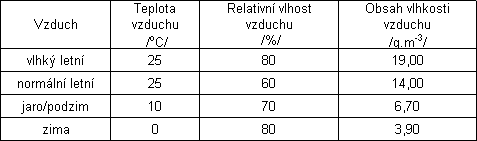
Doporučená doba sušení pro vybrané materiály

Pozn.: Podmínky pro sušení v této tabulce jsou zpracovány z materiálových norem, prospektů, doporučení výrobců.
Hodnoty označené * udávají teploty a doby sušení při nevhodném skladování, jinak se polyolefíny nemusí sušit
Sušení a navlhání jsou vratné děje a vysušený materiál
je nutno chránit před vlhkostí v ovzduší. Do
násypky zpracovatelských strojů se může dát jen takové
množství materiálu, které se zpracuje asi do 30 minut. Násypky
některých strojů jsou vyhřívány a teplota materiálu se udržuje
na potřebné výši proudem teplého vzduchu.
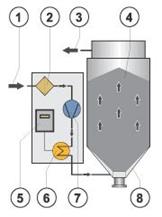
Sušící jednotka na násypce vstřikovacího stroje
1 – vstup vzduchu, 2 – filtr, 3 – výstup vzduchu, 4 – směr průchodu vzduchu, 5 – kontrola teploty,
6 – ohřev vzduchu s bezpečnostním termostatem, 7 – dmychadlo, 8 - násypka
Kromě vyhřívaných násypek strojů se používají i
stacionární sušárny, které mohou pracovat buď s nepřetržitým
nebo periodickým provozem a nebo podle vzájemného pohybu
sušeného materiálu a sušícího média dělí na souproudé,
protiproudé a nebo s kříženým proudem. Souproudé
sušárny se hodí k sušení polymerů, které snášejí intenzívní
sušení a mají malou hydroskopičnost. Výhodou je, že teplota
odcházejícího polymeru ze sušárny je nízká, protože se nakonec
materiál stýká s ochlazeným vzduchem. Při protiproudu se sušící
médium s nejvyšší teplotou a nejnižší vlhkostí stýká s vysušeným
materiálem. Neexistují zde velké rozdíly v obsahu vlhkosti a
teplotě, rychlost sušení je však oproti protiproudu nižší. Hodí
se pro polymery, které nesnášejí velkou rychlost sušení. Křížený
proud je kombinací souproudu a protiproudu. Další dělení sušáren
je podle oběhu vzduchu na sušárny s oběhem vzduchu otevřeným
nebo uzavřeným a podle tlaku se sušárny dělí na
atmosférické nebo vakuové. Vakuové sušárny se
používají k sušení plastů, u kterých je nebezpečí oxidace (změna
barvy, zhoršení mechanických vlastností, atd.) za zvýšených
teplot.
3.3. Míchání a hnětení
Při výrobě polymerů
polyreakcemi není míchání žádným problémem. Ve zbylých
případech použití technologie míchání je založeno na smíchání
základního polymeru s přísadami pro zlepšení vlastností plastu
(stabilizátory, plniva, změkčovadla, barviva, atd.) nebo pro
zlepšení a usnadnění zpracování (např. maziva). Míchání se
aplikuje u všech stavů polymerů – u tavenin, kapalin, prášků,
granulí, atd.
Míchání je proces, kdy dochází ke smíchání minimálně dvou složek v míchacím
prostoru zařízení tak, aby bylo dosaženo požadované
rovnoměrnosti rozložení jednotlivých komponentů ve výsledném
produktu s požadovaným stupněm homogenity. Konečný stupeň
homogenity nemusí být však dosažen již ve fázi míchání, ale
teprve v následných technologických operacích, jako vstřikování,
válcování, vytlačování, apod.
Míchání lze rozdělit podle odporu, který kladou promíchávané částice vnější síle, jež na ně
působí na dva extrémní případy, kdy prvním je míchání látek s nepatrným
odporem proti posunutí (např. prášky) a druhým jsou procesy
míchání s velkým odporem proti posunutí, které se dělí
na:
- intenzívní míchání – stupeň homogenity závisí na stupni smykového namáhání
(např. míchání kaučuků s přísadami), hmota je ve změklém stavu =
hnětení nebo také plastikace, používají se stroje označované jako hnětiče,
- extenzívní míchání – stupeň homogenity závisí na stupni tečení nebo na vytváření nového povrchu
(např. míchání prášků s barvivy), používají se stroje označované jako míchačky.
Přechod mezi míchačkami a hnětiči není skokový. Stroje jsou v podstatě
konstruovány od lehké konstrukce až po nejtěžší konstrukce. Pro
hnětení je dále výhodné, aby hnětené materiály měly zhruba
stejnou viskozitu, jinak částice s vyšší tuhostí prokluzují
v měkčím materiálu. Při hnětení kaučuků s plnivem dochází
k zahřívání směsí, proto se proces provádí ve více stupních.
Používají se k míchání past, směsí PVC, lepidel, atd. Jsou lehčí
konstrukce, která je založena na pohybujícím se nástroji –
míchadlu a podle polohy osy otáčení se dělí na
horizontální a
vertikální. Speciální skupinu tvoří míchačky bez pohyblivých
elementů.
Mezi horizontální stroje patří bubnová míchačka, která se používá pro
míchání sypkých hmot. Dochází zde k minimálnímu smykovému
namáhání míchaného materiálu a někdy se používají uvnitř bubnu
úpravu na zlepšení promíchání hmot.
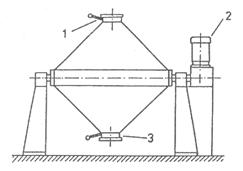
Bubnová míchačka
1 – plnící otvor, 2 – motor, 3 – výpustní otvor
Další horizontální míchačkou je pásová míchačka. Rotor tvoří pásy
spirálově navinuté do tvaru válce, který přehrnuje materiál
z jedné strany na druhou a tyto míchačky slouží k míchání
práškových hmot. K míchání kapalin, resp. past jsou pásy
nahrazeny lopatkami ve tvaru přerušované šroubovice.
Dvouramenná míchačka se používá k přípravě lepidel, past, kaší,
atd. Má masivní konstrukci s objemem nádrže do 10000 l. Dno
nádrže tvoří dva půlválce, v nichž se otáčejí míchadla. Míchadel
a jejich tvarů bývá velké množství.
Přední míchadlo se otáčí 1,5 až 2krát pomaleji než zadní. Nádrž
je vytápěná nebo chlazená a vyklápí se pootočením.
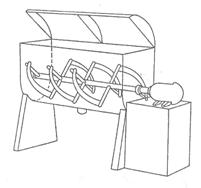
Pásová míchačka
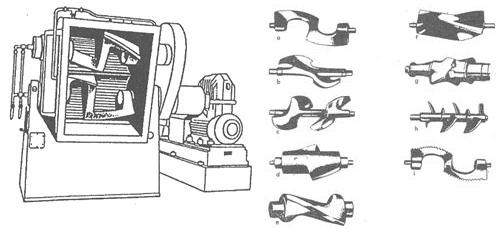
Dvouramenná míchačka a příklady konstrukce míchadel
Mezi vertikální míchací stroje patří lopatková míchačka s
lopatkovým
tvarem míchadel a s velmi jednoduchou výměnou míchací
nádrže. Používá se pro míchání kapalin, lepidel, past, atd.
Planetová míchačka slouží k míchání viskózních hmot, je
používána např. pro přípravu past, roztoků, tmelů, atd. Dvě
míchací ramena s lopatkami se pohybují kolem stěn nádoby a
přitom se otáčejí kolem své osy. Výhodou jsou opět jednoduché
míchací nádoby, které je možné snadno měnit a také uzavřít.
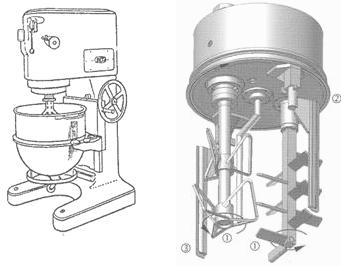
Lopatková míchačka(vlevo),Planetová míchačka(vpravo)
Fluidační míchačka je moderním typem vysokootáčkové míchačky
schopné míchat práškové hmoty, homogenizovat, barvit, apod.
Rotor se otáčí obvodovou rychlostí 30 až 60m.s-1
a uvádí práškový polymer do vířivého pohybu, při kterém nárazy
na rotor, stěny a mezi sebou vzniká třením teplo. Podle použité
teploty vzniká pak buď suchá směs nebo hrudkovitá směs. Míchačka
se plní horním víkem a výpust je dole. Cykly jsou krátké, 5 až
10 min.

Fluidační míchačka
1 – výpustní otvor, 2 – rotor, 3 – plnící otvor, 4 - motor
Speciální míchačky
dosahují míchacího účinku rozdělováním tekoucí taveniny do
několika proudů, jejich směšováním a opětovným rozdělováním.
Zařazují se nejčastěji před trysky (torpédo) nebo před
vytlačovací hlavu.
3.3.2. Hnětací stroje
Tyto stroje jsou schopné tedy nejenom smísit plasty s přísadami,
ale i působením intenzivního smykového namáhání převést polymer
do plastického stavu. Hnětací stroje se podle způsobu práce dělí
na diskontinuální (jsou pružnější při změně materiálu,
ale kolísá kvalita v jednotlivých dávkách) a kontinuální
(přesný produkt, ale s nutností přesného dávkování).
Míchací dvouválce patří k diskontinuální hnětacím strojům a
používají se k míchání kaučukových směsí, k ohřevu, apod.
Výhodou je velká plocha válců, umožňující temperaci hmoty.
Nevýhodou je nebezpečná obsluha, dlouhé míchací časy,
nestejnoměrná kvalita. Obvodová rychlost válců bývá v rozmezí
0,4 až 0,6 m.s-1. Při hnětení se na předním válci
vytvoří souvislá vrstva plastu a přebytek hmoty ve nad mezerou
mezi válci. Povrch vrstvy má menší obvodovou rychlost než válec
zadní a tak dochází k hnětení. Poměr obvodových rychlostí se
nazývá skluz a bývá v rozmezí 1:1,1 až 1,3. Hnětení je tím
intenzivnější, čím větší je rozdíl obvodových rychlostí a čím
menší je štěrbina mezi válci.
Malá výkonnost dvouválců vedly ke konstrukci speciálních hnětacích
strojů –
hnětičů, které se používají u kaučukových směsí a u prášků.
Výhodou je vyšší výkon, menší spotřeba energie, lepší homogenita
směsi, atd. Nevýhodou je nestejnoměrný produkt a musí následovat
další operace pro úpravu. Diskontinuální hnětiče jsou
konstruovány jednak tak, že hnětadla do sebe nezasahují a mají
různou obvodovou rychlost a nebo do sebe hnětadla zasahují a
mají stejnou obvodovou rychlost. Materiál je vtlačován klínem do
procesu mezi rotory, proto jsou to zařízení tlaková.
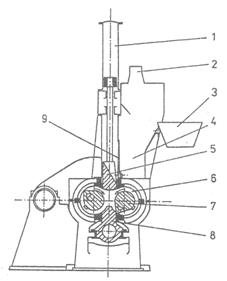
Tlakový hnětič
1 – vzduchový válec pro klín, 2 – odsávání prachu, 3 – plnění, 4 – plnící násypka,
5 – přítlačný klín, 6 – míchací komora, 7 – hnětadla, 8 – spodní výpust, 9 - klapka
Hnětení nastává hlavně na stěnách komory
roztíráním vlivem otáčejících se hnětadel. Komora je dutá pro
vytápění nebo chlazení, výstup je ve spodní části. Doba cyklu je
velmi krátká, kolem 2 až 3 min. Objem komory je kolem 600 l.
Kolísání kvality směsi je omezeno přesným dávkováním. Za hnětiči
se obvykle umísťuje dvouválec nebo vytlačovací stroj.
Kontinuální hnětiče odstraňují
nedostatky diskontinuálních strojů (nízkou výkonnost, omezenou
automatizaci, nestejnou homogenitu, atd.) a navíc dokáží
zplastikovat i špatně sypatelné materiály, nedochází zde
k přehřívání, umožňují odplyňování, jsou rychle a snadno
čistitelné, atd. Konstrukce kontinuálních hnětičů vychází ze
šnekových vytlačovacích strojů.
Konvenční šnekové stroje však mají malý hnětací účinek a
proto se používá různých úprav, aby byla hmota vystavena
intenzivnímu smykovému namáhání.
Šnekový vytlačovací stroj s planetovými
válci patří mezi jednošnekové hnětací stroje, kde termoplast je
plastikován při průchodu mezerami mezi šnekem, symetricky
uloženými válci a pevným pouzdrem. Ozubení má velký úhel
stoupání (45o), což umožňuje nejenom plastikaci, ale
i dopravu.
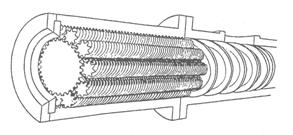
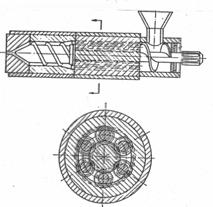
Šnekový vytlačovací stroj s planetovými válci
KO hnětič je šnekový vytlačovací stroj pro termoplasty i reaktoplasty s mezerami v závitech šneku, do
kterých zasahují v řadách uspořádané a vhodně dimenzované
hnětací zuby, upevněné na vnitřní straně pouzdra. Otáčející se
šnek vykonává oscilační pohyb tak, že mezery v závitu šneku
těsně míjejí hnětací zuby. Plášť stroje je rozpůlen v podélném
směru kvůli snadnému čištění. Šneky mají otáčky 100 až 120 min-1
a délku 7 až 11D. Nedostatkem KO hnětiče je pulsace hmoty na
výstupu, což se dá odstranit vytlačovacím strojem.
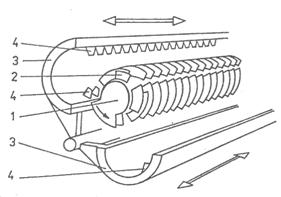
KO hnětič
1 – šnek, 2 – přerušovaná šroubovice šneku, 3 – dělené pouzdro, 4 – zuby na pouzdře
Výhodnější než jednošnekové stroje jsou
dvoušnekové stroje, jejichž šneky jsou vybaveny různými
hnětacími vložkami pro zvýšení hnětacího účinku. Trojúhelníkové
vložky mají větší hnětací účinek, než oválné. Dvoušnekový
hnětací stroj s
hnětacími
vložkami ZSK má stejný smysl otáčení obou šneků, které jsou
nad sebou a zasahují do sebe a jejichž vložky jsou pootočeny
tak, že jejich hřbety vytvářejí tříchodý nebo dvouchodý šnek.
Vlastní hnětení probíhá mezi hnětacími vložkami a komorou.
Axiální posun a tlak zajišťují dopravní vložky. Polymery lze
odplyňovat. Tyto stroje jsou používány ke zpracovaní polymerů
s různými aditivy. Výkon je pro šnek 300 mm průměru kolem 15000
kg PE. Někdy se kombinuje s kolmo postaveným jednošnekovým
vytlačovacím strojem nebo zubovým čerpadlem.
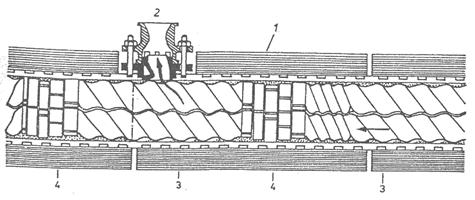
Dvoušnekový hnětací stroj s vložkami typu ZSK
1 – vytápění, 2 – odsávání plynových zplodin, 3 – dopravní vložky, 4 – hnětací vložky
Kontinuální hnětič typu FCM se
nejvíce blíží tvarem hnětadel diskontinuálnímu hnětiči. Dvojice
hnětadel do sebe nezasahuje a otáčí se proti sobě s odlišnými
rychlostmi. Intenzita hnětení se reguluje škrtící klapkou,
kterou se řídí odvod polymeru. Bývá vybaven pomocným
vytlačovacím strojem pro granulaci.
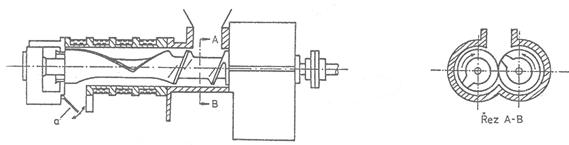
Hnětič FCM
3.4.
Granulace
Konečným stupněm
přípravného zpracování pro většinu plastů je granulace, kdy
materiál získává tvar
granulí, který je vhodný pro další zpracování, neboť granule
mají dobrou sypnou hmotnost, lze je dobře směšovat s dalšími
materiály, např. barvivy a lze je dobře dávkovat. Do tvaru
granulí se často převádí i
recyklát získaný mletím nebo drcením, potom mluvíme o
regenerátu. Tvar granulí jsou buď válečky, čočky, krychličky
nebo kuličky.
Výběr granulační metody závisí na vlastnostech zpracovávané taveniny,
na prostoru, na požadovaném výkonu, na ekonomii, atd. První
z možných technologií granulace je granulace z pásu. Tento
způsob je nevhodný pro tvrdé materiály a je málo produktivní.
Princip je založen na rozřezání materiálu na proužky, které jsou
rozsekány na granule.
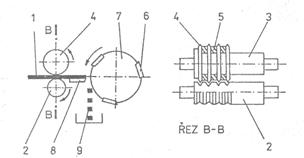
Pásová granulace
1 – pás plastu, 2 – podávací válec, 3 – hřídel, 4 – kotoučové řezací nože,
5 – distanční vložky, 6 – rotační nože, 7 – buben, 8 – pevný nůž, 9 - granule
Výkonnější metody jsou založeny na granulaci strun a rozeznáváme buď granulaci za
studena nebo granulaci za tepla. Při
granulaci za studena jsou struny vytlačené granulační hlavou
s mnoha otvory ochlazeny ve vodní lázni a po odstranění
přebytečné vody jsou sekány na granule. Nevýhodou je velké
množství strun, které se mohou slepovat nebo lámat. Výkon linek
je kolem 2000 kg.h-1.
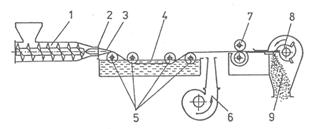
Granulace za studena
1 – šnekový vytlačovací stroj, 2 – granulační hlava, 3 – struny, 4 – chladící kapalina,
5 – vodící válečky, 6 - - ventilátor, 7 – podávací vlečky, 8 – nože, 9 – granule
Při granulaci za tepla (za horka) jsou
granule seřezávány přímo z čela granulační hlavy s mnoha
otvory.
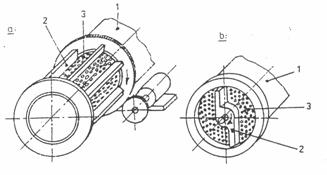
Granulační hlavy
a – obvodové řezání, b – řezání na čele, 1 – granulační hlava, 2 – nůž, 3 - granule
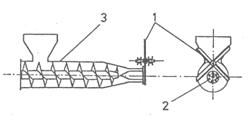
Granulace za tepla
1 – rotační nůž, 2 – granulační hlava, 3 – šnekový stroj
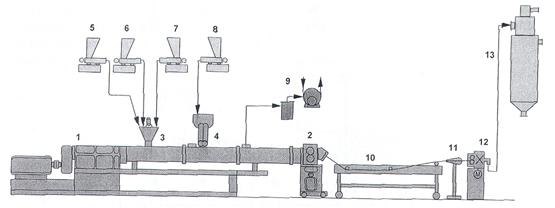
Linka pro míchání vyztužujících plniv do termoplastické matrice se současnou granulací
1 – KO hnětič, 2 – granulační hlava, 3, 4 – plnící šnek, 5, 6 - polymer,
7 – aditiva, 8 – vyztužující vlákna, 9 – odsávání, 10 – vodní chlazení, 11 – vzduchový nůž,
12 – sekání noži, 13 – sušení a chlazení
Pro tuto metodu nejsou vhodné polymery s velmi nízkou viskozitou
taveniny. Podle účinku chladící vody na nožích rozeznáváme
granulaci suchou a granulaci pod vodou. Při suché
granulaci za tepla je roztavený polymer seřezáván za sucha
nožovým zařízením, které se otáčí velkou rychlostí a odhazuje
granule od čela hlavy, které jsou potom ochlazeny ve vodní lázni
a sušeny. Při granulaci pod vodou (pro polymery, které mají
tendenci se roztírat) jsou odříznuté granule, ale i nože,
bezprostředně chlazeny vodou. Na obrázku je ukázána linka na
míchání a hnětení polymerů s následnou granulací.
3.5.
Tabletování
Pro zpracováni reaktoplastů je z hlediska rychlého a přesného dávkování,
z hlediska snížení prašnosti, z hlediska zmenšení plnícího
prostoru lisovací formy, z hlediska zkrácení doby lisování a
vytvrzování, z hlediska snadného předehřevu výhodné, aby
prášková hmota byla slisována do pevného tvaru – tablety. Stroje
používané pro tabletování jsou buď mechanické
(nejrozšířenější) nebo hydraulické pro tablety větších
rozměrů nebo s plnivy. Podle uspořádání jsou konstruovány buď s výstředníkem
nebo jako rotační (vyšší výkon, až 200000 tablet za
hodinu).
3.6.
Recyklace – mletí a drcení
Nezbytným předpokladem pro technicky i ekonomicky účelné využití odpadu je dobrá znalost
technologie výroby, zpracování i sortimentu výrobků. Je to
hlavně do značné míry vysoká cena plastů, která vede výrobce
k tomu, aby se zabývaly zpracováním odpadu z plastů a
recyklací nefunkčních výrobků. V současné době existuje
mnoho zařízení (mlýny,
regranulační linky, podavače, manipulátory, apod), které
dokáží zpracovat odpad na recyklát, resp. regenerát za
přijatelné náklady a ve vyhovující kvalitě.
Odpady, vznikající při výrobě lze rozdělit na technologický a
užitný odpad. Technologické odpady, vznikající při výrobě,
zahrnují v sobě vtokové systémy, vadné výrobky, odstřiky, aj. a
je tedy záležitostí každého výrobce, aby byly vráceny zpět do
výroby jako vstupní surovina už jenom kvůli energetické
náročnosti (na 1 tunu plastů se spotřebuje kolem 2,5 tuny ropy).
Kromě toho existuje i užitný odpad, což jsou výrobky po skončení
své funkční doby. Zatímco první skupina poskytuje relativně
kvalitní materiál, srovnatelný s původními dosud nezpracovanými
materiály, tak druhá skupina je obvykle znečištěna a polymer je
více či méně znehodnocen stárnutím.
Při použití jednotlivých odpadů k dalšímu zpracování je nutné si uvědomit
jejich původ a zvážit, jak byl materiál dříve zpracováván.
Záleží také na tom, zda byl materiál pouze drcený a nebo drcený
a regranulovaný. Použití drceného materiálu má výhodu u tepelně
citlivých materiálů (nejsou znovu tepelně namáhány při
regranulaci), ale nevýhodou je nestejná velikost drcených
(mletých) částí a zvýšený obsah prachových podílů. Tato nevýhoda
se dá odstranit použitím vhodných sít, pomalým mletím a nebo
odsáváním prachu. Na druhé straně regranulovaný materiál je
z hlediska tvaru vstupních částic rovnocenný materiálu
původnímu. Navíc lze použít různých aditiv (stabilizátory,
plniva, maziva, barviva, apod.) ke zlepšení užitných a
zpracovatelských vlastností. Nevýhodou regranulace je
energetická náročnost a u většiny plastů dokonalé vysušení
rozemletého odpadu. Při zvažování možností využití druhotných
surovin je třeba mít na zřeteli, že materiál prochází při
zpracování rozdílnými fyzikálními i chemickými procesy, které
vedou ke změnám struktury a složení.
Rozemleté a nebo regranulované plastové odpady a výrobky lze ve výrobním
procesu zpracovávat buď samostatně a nebo jako příměs
k originálnímu materiálu. První způsob je méně výhodný, protože
regenerací nejsou zaručeny původní vlastnosti materiálů.
Výhodnější je používat regenerátu jako příměsi, přičemž je nutné
míchat jen takový poměr, aby se objemové procento následně
regenerovaného materiálu rychle snižovalo. Většina předních
výrobců hmot, zpracovatelů a vědeckých a výzkumných pracovišť
doporučují přidávat maximálně 20 % regenerátu do původní hmoty,
čímž je zaručeno, že materiál se nevrátí k regeneraci více jak
desetkrát, což je pro většinu plastů vyhovující. Znovuzpracování
odpadu (drceného nebo regranulovaného) a výsledná kvalita
výrobků závisí na typu polymeru, jeho aditivaci a podmínkách
zpracování původního materiálu. Obecně platí, že degradace
polymerů závisí na obsahu a typu stabilizátorů, vlhkosti,
teplotě vstřikování a době prodlevy materiálu v tavící komoře.
Posouzení kvality zpracovávaného odpadu lze provést pouze pomocí
experimentů.
Pro zpracování odpadů drcením (mletím) se používají různé typy
mlýnů (kladivový,
třecí, nožový, kulový,
aj.), kdy zmenšování rozměrů lze dosáhnout tlakem, smykem
nebo řezem. Pro volbu drcení jsou důležité fyzikální vlastnosti
rozmělňovaného materiálu, jako je tvrdost a charakter lomu.
Jedním z nejvíce používaných mlýnů je nožový mlýn, který má jednak několik
nožů uložených radiálně kolem rotoru (na statoru) a jednak
nože umístěné přímo na rotoru. Velikost drtě je daná velikostí
ok síta, umístěného v dolní části mlýnu. Výhodou těchto mlýnů je
rovnoměrná velikost recyklátu s malým množstvím prachu, snadno
se čistí a jemnost je dána velikostí oka síta.
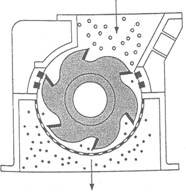
Nožový mlýn
Dále se používá talířový nárazový mlýn, jehož výhodou je schopnost
rozemlít materiál na rovnoměrnou zrnitost 100
mm,
vhodnou pro stříkání, fluidní nanášení, apod. Velikost
rozemletého materiálu je daná velikostí štěrbiny mezi bočnicemi.
Nepoužívají se síta a nedochází k přehřívání materiálu. Mezi
další konstrukce mlýnů patří nosový nebo kolíkový mlýn, které
se však používají v mnohem menší míře, než nožové mlýny.
Používají se k mletí měkkého odpadu.
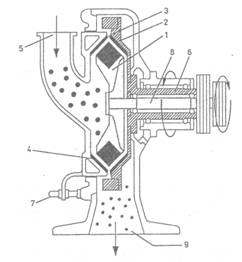
Talířový nárazový mlýn
1 – rotor, 2 – otáčející se rýhovaná bočnice, 3 – regulovatelná štěrbina,
4 – pevná axiálně posuvná rýhovaná bočnice, 5 – plnící otvor, 6 – hřídel bočnice,
7 – šrouby, 8 – hřídel rotoru, 9 – výpustní otvor
Při výrobě regranulovaných regenerátů se po operaci mletí nebo drcení
provádí následné zpracování na hnětacích strojích nebo na
jednošnekových nebo vícešnekových strojích, na které navazuje
granulační jednotka.
.: Jdi na začátek stránky :.
|
|