- Technologie objemového tváření – protlačování
5.1. Princip protlačování a vliv materiálu
5.2. Výpočet síly a práce
5.3. Vliv tření
5.4. Rozdělení technologických způsobů protlačování
5.4.1. Dopředné protlačování
5.4.2. Zpětné protlačování
5.4.3. Kombinované (sdružené) protlačování
5.4.4. Stranové a radiální protlačování
5.5. Speciální způsoby protlačování
5.5.1. Protlačování trubek
5.5.2. Hydrostatické protlačování
5.6. Stroje a nástroje pro protlačování
5. Technologie objemového tváření
- Protlačování
Protlačování je
technologie, kterou můžeme provádět
za tepla, za poloohřevu a za studena. Napjatost
v přetvářeném elementu materiálu je trojosá, všestranné tlaková.
Tvářený materiál se přemísťuje a jeho směr pohybu je určen
konstrukcí nástroje –
protlačovadla. Výrobek se nazývá protlaček .
Tuto technologii je možno dělit
do dvou skupin. První se týká výroby finálních výrobků, druhá
výroby polotovarů (trubek,
tyčí,
profilů, apod.). Protlačování za studena je u lehkých a
barevných kovů známo již přes 100 let. Tímto způsobem se
vyráběly a vyrábějí např. tuby, nábojnice, apod.
5.1. Princip protlačování a vliv materiálu
Principem protlačování je deformace materiálu v důsledku
působících sil do předem stanoveného směru s konečnými výhodnými
mechanickými a rozměrovými vlastnostmi konečného výrobku.
Protlačování je jedním z procesů, které přispěly k výraznému
snížení vlastních nákladů ve výrobě, tedy i k racionalizaci
výroby. Přesnost průtlačků je obvykle velmi vysoká (±
0,05 mm), takže není nutno před montáží průtlačky rozměrově
upravovat. Také využití materiálu je vysoké, 90 až 100 %
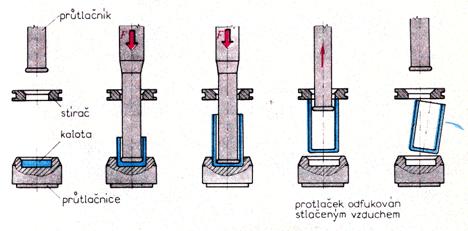
Princip technologie protlačování
Jakost a výchozí stav materiálu má výrazný vliv na technologii a proces protlačování. Vzhledem k velikosti přetvárných odporů
jsou pro protlačování vhodné materiály s tažností větší, než 10 % a kontrakcí větší, než 50 % (oceli s obsahem uhlíku do 0,2 % C).
Nevhodné jsou materiály, u kterých je nutno vynaložit specifický
tvářecí tlak větší jak 2500 MPa a nebo nelze během jedné operace
v důsledku chemického složení (tedy zpevnění) získat deformaci
alespoň 25 %. Materiály s nízkou přetvárnou pevností, hliník a
jeho slitiny, se dají protlačovat na jednu operaci. Oceli a
ostatní kovy se protlačují na více operací. Někdy je potřeba
provádět i mezioperační žíhání (nejdříve rekrystalizační a potom
na měkko). Maximální redukce na jednu protlačovací operaci je omezena přípustným namáháním nástroje. Redukce u oceli např.
s obsahem 0,1 % C je až 60 %. Před vlastním protlačováním je
nutná úprava materiálu
rovnáním a dělením na
kaloty včetně tepelného zpracování. Následuje povrchová
úprava.
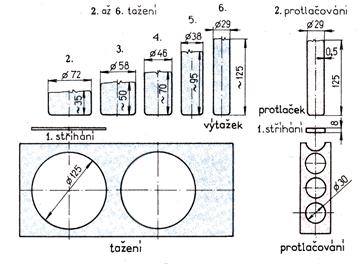
Porovnání protlačování s hlubokým tažením
5.2. výpočet síly a práce
Na protlačovaní za studena jsou potřebné
velké deformační síly, které závisí na chemické složení
materiálu, přípravě a tepelném zpracování, mazání, geometrii
nástroje (čím větší, tím větší síla), velikosti redukce (čím
větší, tím větší síla), tloušťka stěny (čím menší, tím větší
síla), druh stroje. Potřebné síly a práce se
vypočítají velmi obtížně a nebudou zde uváděny. Přetvárný odpor
při protlačování za studena vzrůstá se stupněm zpevnění
materiálu a potom počítáme kostř = (ko1
+ ko2) / 2, i když se nejedná o přímku, ale o
křivku. U protlačování za tepla je přetvárný odpor konstantní.
5.3. vliv tření
Jedním z rozhodujících faktorů na proces
protlačování je
tření, které výrazně ovlivňuje vlastní proces, kvalitu
výrobku a ekonomii výroby, a to zejména u ocelí – musí se
provádět vhodná povrchová úprava, jinak dochází k suchému tření
a zadření nástroje. Povrchová úprava se skládá:
- odstranění povrchových vad (otryskávání, broušení, moření u Al, …),
- z chemického a mechanického čištění (omývání, sušení, …),
- z fosfátování (fosfátovaný povrch má vysokou přilnavost k
výchozímu materiálu, kterým je nejčastěji kotouč nebo kotouč
s otvorem, tzv.
kalota, což umožňuje mazání povrchu materiálu
v důsledku pórovitosti fosfátované vrstvy při velkých
tlacích, čehož bylo prvně použito v 30 letech dvacátého
století),
- z nanesení vrstvy maziva (např. ponořením do roztoku organického oleje a mýdla).
Velikost třecích sil dále závisí na drsnosti povrchu
průtlačníku a
průtlačnice a na jejich opotřebení v kritických místech.
Někdy se jako mazivo u hutnického protlačování za tepla používá
sklo vhodného chemického složení, které se při protlačování
roztaví (nutnost odstranit sklovitou kůru). U neželezných kovů
se používá tzv.
košilka, tj. mezera mezi průtlačníkem a průtlačnicí o
velikosti 2 až 4 mm, kam zateče materiál, který působí jako
mazivo.
5.4. Rozdělení tehnologických způsobů protlačování
Protlačování dělíme podle směru pohybu materiálu a nástroje na
dopředné, zpětné, kombinované, stranové
a radiální.
5.4.1.
Dopředné protlačování
Při
dopředném (přímém) protlačování se materiál pohybuje ve
stejném směru jako průtlačník. Výchozím polotovarem bývá kalota,
získaná např. lisováním plechu nebo upichováním z tyčí. Používá
se při tváření čepů, šroubů, pouzder, apod., tedy výrobků, u
kterých není konstantní průřez
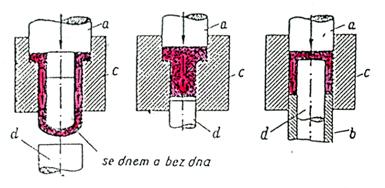
Princip dopředného protlačování
(1, 3 – průtlačnice, 2, 4 - průtlačník, a, – průtlačník,
b – stírač, c – průtlačnice, d - vyhazovač)
5.4.2.
Zpětné protlačování
Pří zpětném protlačování se pohybuje
materiál v opačném směru a používá se k výrobě dutých protlačků
i se žebry, kdy tloušťka stěny je v porovnání s průměrem velmi
malá anebo naopak.
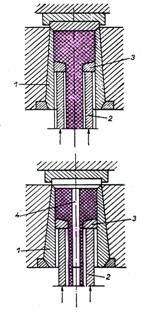
Princip zpětného protlačování
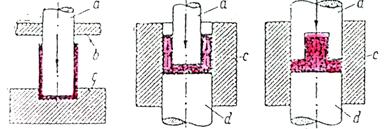
Princip zpětného protlačování
(1, 3 – průtlačnice, 2, 4 - průtlačník, a, –
průtlačník, b – stírač, c – průtlačnice, d - vyhazovač
5.4.3. Kombinované (sdružené) protlačování
Vyrábí se tím profilové výrobky, které
jsou velmi namáhané a které nemusí být válcového tvaru.
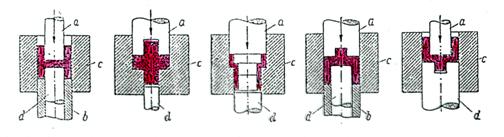
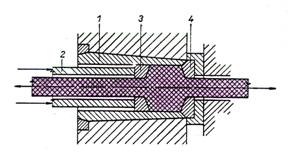
Princip kombinovaného protlačování
(1, 3 – průtlačnice, 2, 4 - průtlačník, a, – průtlačník, b – stírač, c – průtlačnice, d – vyhazovač)
Při kombinovaném protlačování se materiál pohybuje v obou
jmenovaných směrech, kdy musí platit, že stupeň deformace
v dolní části průtlačku na dně průtlačnice musí být menší, než
v horní části, kterou tváří průtlačník, jinak materiál do
tvarovaného dna nezateče.
5.4.4. Stranové a radiální protlačování
Při stranovém protlačování se tvářený
materiál pohybuje kolmo na směr pohybu průtlačníku a slouží
k výrobě průtlačků s vnějším i vnitřním oboustranným osazením.
Radiálním protlačováním rozumíme tváření, při kterém se materiál
i části nástroje pohybují v radiálním směru vzhledem k ose
materiálu.
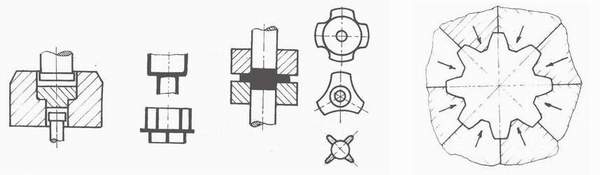
Princip stranového (vlevo a uprostřed) a radiálního protlačování
5.5. Speciální způsoby protlačování
Speciální
metodou protlačování je ražení (vtlačování),
protlačování trubek a
hydrostatické protlačování kovů.
Ražením se vyrábějí funkční tvary dutin nástrojů v důsledku zvýšení
životnosti.
5.5.1.
Protlačování trubek
U technologie
protlačování
trubek jsou výchozím polotovarem válcované špalky
potřebné délky. Následuje většinou ohřev a vlastní
děrování a
protlačování dopředným způsobem. Po skončení procesu zůstává
v matrici zbytek, technologický odpad, který se musí odstranit.
Stupeň deformace je velký, kdy součinitel prodloužení je 8 až 25
(z polotovaru o délce např. 700 mm a průměru 200 mm lze vyrobit
trubku délky 6 až 18 m).
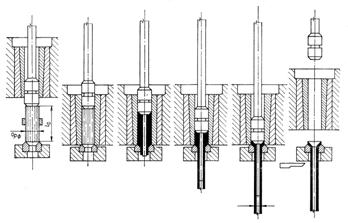 Technologie výroby trubek
protlačováním
5.5.2.
Hydrostatické protlačování
Další speciální technologií je
hydrostatické protlačování, kdy je polotovar obklopen
kapalinou o vysokém tlaku. Tím se v něm vytváří všestranné
napětí a tvárnost materiálu se zvýší. Technologické možnosti
hydrostatického protlačování jsou dnes již takové, že se může
protlačovat již bez fosfatizační vrstvy, nebo např. výrobky
plátované mědí. Hydrostatický tlak je až 3000 MPa. Přetvoření
v jedné operaci může dosáhnou až 80 %.
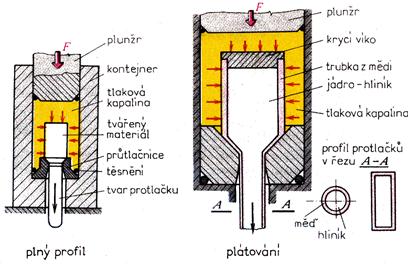
Princip hydrostatického protlačování
5.6. stroje a Nástroje pro protlačování
Důležitým faktorem je také konstrukce nástroje a geometrie
průtlačníku a průtlačnice. Nelze volit libovolné úkosy, rádiusy, zaoblení, apod. tvarových
částí nástroje. Nástroj, který je složen z průtlačníku a
průtlačnice jako hlavních částí, je namáhán vysokými měrnými
tlaky, proto závisí na jeho materiálu, tepelném zpracování a
drsnosti povrchu. Životnost tvarových částí nástrojů je od 3000
do 50000 kusů. Proces protlačování ocelí za studena je omezen
pevností materiálu průtlačnice, ale při zpětném protlačování i
pevností materiálu průtlačníku.
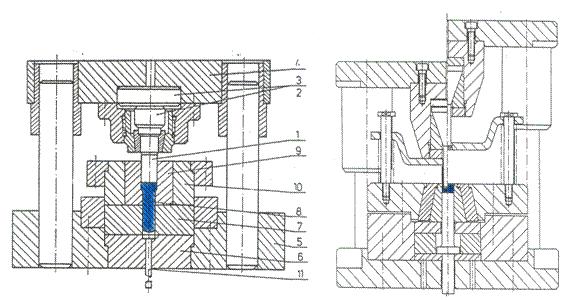 Konstrukce a schéma nástroje
pro dopředné a zpětné protlačování
K protlačování za studena se
používá většinou mechanických klikových a kolenových
vertikálních lisů a lisů hydraulických. Lisovací síla je 300 až
120000 kN. Při protlačování za tepla se zpracovávají materiály,
jejichž tvářitelnost je za studena omezená a např. válcování by
bylo příliš nákladné. Po protlačování jsou protlačky vysunuty
z pracovního prostoru vyhazovačem nebo sfouknuty stlačeným
vzduchem. Při kombinovaném protlačování se vyhazují protlačky
buď vyhazovačem nebo stěračem podle toho, zda ulpí na
průtlačníku nebo zůstanou v průtlačnici. Vnitřní stěny protlačků
jsou mírně kuželové s úkosem 1 až 2o. Nástroj musí
být opatřen otvory pro únik vzduchu a maziva.
.: Jdi na začátek stránky :.
|